- Publié le 27 févr. 2024
- Mis à jour le 27 févr. 2024
- 11 min
Quels moyens de surveillance et de contrôle mettre en œuvre pour assurer le bon déroulement du process ?
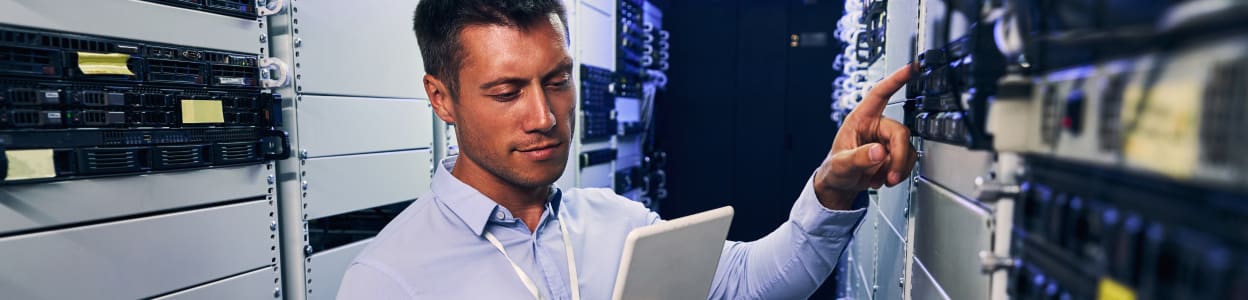
Dans le monde de la production industrielle, la surveillance et le contrôle de la production sont essentiels pour assurer l'efficacité opérationnelle, la qualité des produits et la conformité aux normes imposées dans l'industrie. Heureusement, différents moyens existent sur le marché, allant des solutions IoT et automatisées aux logiciels de surveillance de l’état de santé de l’équipement jusqu’à l’ensemble du process, et ce en temps réel.
Si contrôler sa production est indispensable pour éviter – notamment – la mise au rebut de produits, les pertes de matières ou encore les problèmes de qualité, surveiller celle-ci au plus près de la machine et de chaque équipement pendant son fonctionnement (maintenance conditionnelle), si possible en temps réel voire en amont d’une panne à venir, sont des enjeux auxquels la production mais aussi et surtout la maintenance sont aujourd’hui confrontés.
La maintenance prévisionnelle (ou « anticipée ») répond à une norme européenne de 2018 bien spécifique, l’EN-13306 X 60-319. Celle-ci porte plus précisément sur la manière de mettre en place tous les moyens permettant de détecter le moindre signe de défaillance afin d’intervenir en amont de la panne – et donc d’un arrêt de production coûteux à la fois financièrement et en conséquences vis-à-vis des clients finaux
Mais avant même de parler de surveillance en amont d’un quelconque problème, il existe déjà des moyens permettant de surveiller le bon déroulement de la production. Pour assurer cette tâche, il existe plusieurs moyens et instruments de surveillance, de mesure et de contrôle qu’il est possible de mettre en œuvre, à commencer par l’analyse vibratoire.
L’analyse vibratoire, pilier de la surveillance du process
Élément clef de la maintenance conditionnelle, l’analyse vibratoire est un moyen permettant, à partir d’une mesure périodique du niveau de vibration d’un équipement, de prévenir des usures mécaniques, de la stabilité géométrique de l’équipement de production.
Plus précisément, les vibrations, dont l’apparition indique bien souvent l’arrivée impromptue d’un problème, provient à la fois de la machine mais aussi de causes extérieures ; d’où l’un de ses avantages. L’analyse vibratoire donne ainsi la possibilité de détecter des phénomènes d’usure, de déséquilibres, de desserrement ou de fatigue de certains composants.
Pour ce faire, plusieurs moyens permettant de détecter un signal et d’en délivrer une signature vibratoire de l’équipement existent, tels que la méthode spectrale. Plus simples, d’autres instruments s’offrent aux ateliers tels que les stylos mesureurs (pour l’état de température d’un palier par exemple), les testeurs de vibrations (plus précis), les vibromètres, notamment les vibromètres laser ou encore l’instrumentation miniature qui offrent des moyens de contrôle non destructif (CND). Pour l’analyse vibratoire des machines tournantes et la mesure du déplacement des arbres, il est recommandé de recourir à des capteurs à courant Foucault. Mais il existe une alternative à cette méthode complexe à mettre en œuvre, celle d’utiliser un accéléromètre dans le but d’identifier les vibrations subies lors de l’accélération de la machine.
Les avantages de l'analyse vibratoire sont donc multiples : détecter les signes précurseurs de défaillances mécaniques telles que les déséquilibres, les défauts de roulement et les problèmes d'alignement (etc.), surveiller en continu les équipements afin de détecter rapidement tout changement ou anomalie dans les vibrations et d'effectuer les actions correctives nécessaires.
Enfin, cette méthode offre un diagnostic précis en identifiant la source du problème. Néanmoins, la mise en place d'un système d'analyse vibratoire peut nécessiter un investissement initial significatif pour l'achat d'équipements et de logiciels spécialisés, mais également un niveau d’expertise élevé pour interpréter les données vibratoires. Enfin, elle demeure limitée à certains équipements ou processus de production pouvant ne pas être facilement surveillés par l'analyse vibratoire en raison de contraintes techniques ou de facteurs environnementaux.
Non par opposition mais en complément, la technique des ultrasons peut être utilisée pour détecter les fuites de fluides, y compris dans des environnements bruyants, et ainsi prévenir des pertes de production ou risques potentiels. Il est possible de recourir aux ultrasons dans le but de surveiller différents types d'équipements, tels que les vannes, les réservoirs, les tuyaux, les moteurs, etc. Ceux-ci se révèlent simples d'utilisation grâce à des dispositifs portables ne nécessitant pas – généralement – une expertise approfondie pour interpréter les résultats. Ils sont toutefois limités aux surfaces accessibles aux capteurs uniquement et dépendent des conditions environnementales (bruit ambiant, variations de température) et nécessitent une calibration régulière afin de garantir des résultats précis.
Une multitude de capteurs
Les capteurs sont utiles dans l’analyse vibratoire et les ultrasons, mais pas seulement. De nombreux paramètres permettent directement et indirectement de surveiller l’état de santé de l’outil de production, à commencer par les capteurs de température ; ceux-ci peuvent être intégrés à la fois sur l’équipement, les matériaux ou même en périphérie de la ligne de production, dans le bâtiment afin de contrôler l'environnement de l’atelier et assurer que les conditions sont maintenues dans une plage optimale.
Les capteurs de pression jouent également un rôle essentiel dans l’usine en mesurant la pression des fluides ou des gaz dans les systèmes de production afin de s'assurer qu'ils fonctionnent dans les limites spécifiées. Il en est de même pour les capteurs de débit de liquides ou de gaz, lesquels veillent à ce que les quantités nécessaires soient fournies aux différents stades de la production.
Toujours dans le domaine du contrôle des matières, les capteurs de niveau mesurent quant à eux le niveau de liquides ou de matériaux dans des réservoirs ou des cuves afin de garantir un approvisionnement adéquat et éviter alors les problèmes de sur ou de sous-approvisionnement.
Aussi, les capteurs d'humidité s’avèrent bien utiles en mesurant le taux d'humidité dans l'air ou dans les matériaux. Moins fréquents mais tout aussi efficaces pour détecter d’éventuelles anomalies, en particulier liés aux signaux électriques ou en matière de communication sans fil : l’analyseur de spectre électromagnétique.
Enfin, il semble tout aussi important de rappeler le rôle des capteurs de présence. Souvent utilisés pour éviter toute intrusion sur des lignes de production (avec aussi l’utilisation des barrières immatérielles de sécurité), ceux-ci détectent aussi la présence ou l'absence d'objets ou de matière indésirables ayant pu s’introduire et perturber tout le process. Il est dans ce cas recommandé d’installer des capteurs optiques ou des caméras de surveillance permettant d’observer visuellement les différentes étapes du processus industriel et ainsi détecter rapidement des problèmes potentiels ou tout défaut de production.
Acquisition et traitement des données en temps réel pour intervenir au bon moment
L’ensemble de ces capteurs ont pour objectif de collecter et de transmettre des données aux systèmes de contrôle pour une surveillance en temps réel et une régulation appropriée du processus de production. Mais sans un système d’acquisition et de traitement de ces précieuses données pour les transformer en informations utiles et pertinentes, cette multitude de capteurs et autres objets connectés n’a pas de raison d’être.
Les systèmes d’acquisition de données en temps réel offrent aux ateliers la capacité de mesurer précisément les temps de production, les quantités produites et les quantités de matières utilisées mais pas seulement puis qu’ils permettent d’enregistrer, d’identifier, d’analyser et de quantifier les rebuts. Sans oublier la garantie de davantage de traçabilité. Des outils d'analyse de données en temps réel permettent ensuite de traiter les informations provenant des capteurs et des autres instruments de surveillance automatisée afin d’en tirer des tendances, détecter des anomalies ou toutes déviations par rapport aux paramètres de production.
Pour ce faire, il existe différentes solutions de monitoring et d’outils logiciels permettant de surveiller la production industrielle en temps réel, à l’exemple des systèmes SCADA (Supervisory Control And Data Acquisition). Ces logiciels permettent de collecter, surveiller et analyser les données en temps réel provenant des équipements et des processus de production. Ils offrent des fonctionnalités telles que la visualisation, l'alarme et l'enregistrement des données pour faciliter la gestion du process.
Autre système de plus en plus en vogue, le MES (Manufacturing Execution System). Ces outils logiciels sont pleinement conçus pour superviser et contrôler l'ensemble des opérations de production. Concrètement, ils permettent de collecter des données de production en temps réel, de planifier les ordres de fabrication, de suivre les performances, de gérer les stocks et de générer des rapports analytiques. Ils établissent un lien direct avec l’ERP de l’entreprise offrent ainsi une vue à la précise et complète du process, des matières consommées et de l’état de santé de chaque équipement. Ils représentent également un atout important pour la maintenance qui, à l’aide de la GMAO (logiciel de gestion de la maintenance assistée par ordinateur), va pouvoir maximiser ses prises de décision en matière de stratégie de maintenance préventive, de planification des interventions, de calibration des instruments de mesure et de contrôle mais aussi en termes d’investissement dans des pièces détachées.
Quelques conseils et bonnes pratiques à adopter
Surveiller et contrôler le process industriel est une tâche essentielle pour éviter les arrêts de production (et les coûts qu’ils engendrent), éviter les interventions lourdes de maintenance curative et risquer à la fois d’altérer la qualité des produits finis et de désorganiser l’ensemble de la production.
Avant tout, il est important d’établir et de définir des objectifs de production clairs et mesurables afin de bien orienter ses efforts de contrôle et de choisir les outils de mesure à mettre en place. Il est également important d’utiliser des indicateurs clés de performance (KPI) pertinents afin de suivre les progrès réalisés et d'identifier les domaines nécessitant une quelconque amélioration ou opération de maintenance préventive.
Une fois cette étape passée vient le choix et l’intégration des outils de mesure nécessaires ainsi que des systèmes d’acquisition et de traitement des données, de surveillance en temps réel et des logiciels adaptés. Le choix de la solution de monitoring et du logiciel dépendra des besoins spécifiques de l’usine et des objectifs de surveillance et de contrôle de la production. Il est conseillé de consulter des experts en la matière afin de déterminer la meilleure solution adaptée aux besoins. Aussi, il est important de compléter les systèmes automatisés par des vérifications manuelles régulières dans le but de s'assurer que les équipements fonctionnent correctement et respectent les normes de sécurité.
Du côté de l’organisation du process cette fois, il est recommandé de réaliser des audits réguliers ayant pour objectif d’évaluer l'efficacité des processus de production et d’identifier les zones d'amélioration ; mais ce n’est pas tout. Mener des changements dans l’usine nécessite d’impliquer – c’est-à-dire d’informer puis de former – les employés dans ce nouveau processus de contrôle, faire que leur participation soit proactive et les inciter à se montrer vigilants quant aux risques d’une mauvaise surveillance du process. Cela suppose de les rendre plus attentifs aux signaux d'alerte précoces tels que les fluctuations inhabituelles des données de production.
Car ignorer ces signaux avant-coureurs peut conduire à des problèmes plus importants à l'avenir. Pour ce faire, la mise en place d’un système de gestion de la qualité peut aider à garantir la conformité aux normes et la satisfaction des clients. Plus précisément, les moyens de contrôle de l’ensemble du processus de fabrication d’un produit font remonter des données – transformées en informations – de traçabilité, lesquelles sont ensuite répertoriées dans des rapports qu’il est ensuite possible de générer en format PDF afin de pouvoir être présenté en cas d’un contrôle obligatoire de qualité ou, comme cela arrive malheureusement parfois, en cas de litige avec un client, un donneur d’ordres ou un fournisseur.