- Publié le 7 juin 2023
- Mis à jour le 6 sept. 2023
- 10 min
Normes et règles de sécurité en entrepôt : les incontournables
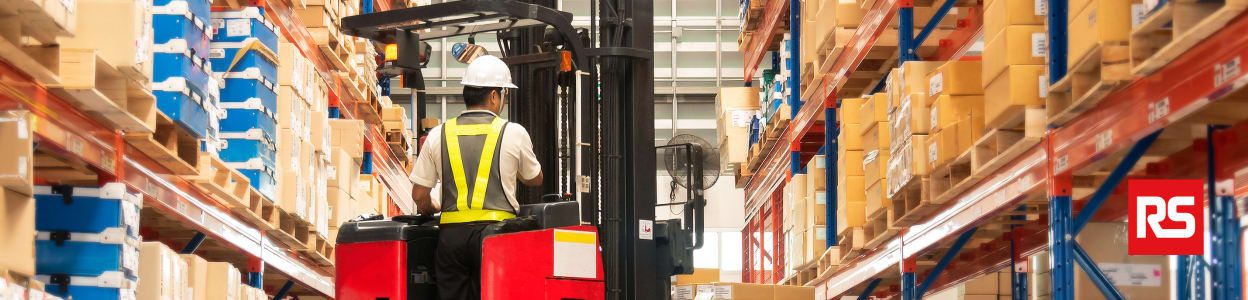
Article publié le 02/06/2023
Dans un entrepôt logistique, la sécurité du personnel est la priorité numéro 1 ! Le moindre manquement au respect des règles peut entraîner des risques graves pour l’entreprise et les employés. Dans cet espace de travail où l’homme et les machines œuvrent à l’unisson, fixer un cadre strict pour faire respecter la réglementation et les normes de sécurité est une obligation. RS vous aide à mettre en place des mesures de prévention et de protection efficaces.
Quelles sont les règles et normes de stockage ?
Le fonctionnement d’un entrepôt est très réglementé. Chutes, collisions, écrasement, électrocution, incendie… le risque est partout présent ! Néanmoins, en appliquant certaines règles de stockage, bon nombre d’accidents peuvent être évités. En tant que dirigeant, préserver les bonnes conditions de travail et de santé de vos travailleurs est de votre ressort.
Une obligation légale de l’entreprise
Au regard des dispositions générales du Code du travail, c’est à l’employeur de tout mettre en œuvre pour assurer la sécurité de son entrepôt, comme le précisent les extraits suivants.
- Article L. 4121-1 : « L’employeur prend les mesures nécessaires pour assurer la sécurité et protéger la santé physique et mentale des travailleurs » ;
- Article L. 4321-1 : « Les équipements de travail et les moyens de protection mis en service ou utilisés dans les établissements destinés à recevoir des travailleurs sont équipés, installés, utilisés, réglés et maintenus de manière à préserver la santé et la sécurité des travailleurs, y compris en cas de modification de ces équipements de travail et de ces moyens de protection » ;
- Article L. 4321-2 : « Il est interdit de mettre en service ou d’utiliser des équipements de travail et des moyens de protection qui ne répondent pas aux règles techniques de conception du chapitre II et aux procédures de certification du chapitre III du titre Ier » ;
- Article R. 4321-1 : « L’employeur met à la disposition des travailleurs les équipements de travail nécessaires, appropriés au travail à réaliser ou convenablement adaptés à cet effet, en vue de préserver leur santé et leur sécurité ».
Les normes de stockage
De très nombreuses normes de stockage existent. Elles sont consultables sur le site de l’Association française de normalisation (AFNOR). Il est par exemple possible de citer :
- La norme NF EN 15 635 qui oblige le propriétaire de l’entrepôt à effectuer une Inspection technique annuelle des rayonnages (ITR) par un technicien qualifié.
- Les normes NF EN 15 878 et NF EN 15 629 qui fournissent des éléments pertinents relatifs au vocabulaire, à la conception et à l’utilisation des rayonnages, sur lesquels il est recommandé de s’appuyer pour la rédaction d’un cahier des charges.
- Les normes NF EN 15 620 et NF EN 15 512 qui regroupent tout un ensemble de règles d’implantation, d’installation, de dimensionnement et de sécurité des rayonnages.
- La norme NF X 35-103 qui fixe les valeurs d’éclairage recommandées des lieux de travail.
Non-respect des règles de stockage : qu’encoure l’entreprise ?
L’inspection du travail, qui est rattachée aux Directions régionales des entreprises de la concurrence, de la consommation, du travail et de l’emploi (Direccte), réalise régulièrement des contrôles des entrepôts. Toutefois, le rôle des agents n’est pas uniquement répréhensif ! Ils vous accompagnent pour trouver des solutions efficaces et pertinentes à mettre en œuvre afin de faire respecter la réglementation.
En revanche, si des infractions portant atteinte aux dispositions réglementaires ou à la santé physique et mentale de vos employés sont constatées, les sanctions peuvent alors s’avérer très lourdes !
Bon à savoir
L’Assurance Maladie — Risques professionnels met gratuitement à disposition sur son site internet des recommandations par secteur d’activité pour adopter les bonnes pratiques de prévention.
RS ScanStock® - Secteur transport
Une société leader dans le secteur de l'eau a réduit de 70 % ses coûts de processus depuis l'adoption de la solution innovante RS ScanStock® de RS.
Concevoir un entrepôt respectant les règles et normes de stockage
Toute personne travaillant dans un entrepôt doit nécessairement prendre connaissance des directives sur la santé et la sécurité au travail de son entreprise. Le dirigeant, de son côté, doit faciliter l’accès à ces informations et veiller à ce que les consignes soient respectées.
L’implantation et la conception de l’entrepôt logistique
L’implantation d’un entrepôt requiert une autorisation d’exploitation, à obtenir auprès de la préfecture de la région concernée. Selon le volume de stockage demandé et la nature des marchandises stockées, les règles diffèrent ! Elles sont notamment renforcées par le code de l’environnement (classement IPCE) en cas d’entreposage de produits dangereux (produits combustibles, explosifs, inflammables, etc.).
Plusieurs paramètres sont donc à réunir pour concevoir un entrepôt sécurisé.
- L’implantation des voies de circulation. Une distance maximale de 20 m entre les rayonnages de stockage et l’accès à une allée de circulation, de service ou de secours est à respecter ;
- La sécurisation des rayonnages, avec :
- Des verrous de sécurité, pour éviter le décrochement des lisses et des entretoises de leur point d’attache ;
- Des dispositifs de retenue adaptés aux charges stockées en cas de chute (panneaux grillagés ou pleins, grillage, filet…) ;
- Des échelles en bordure d’allée de circulation d’une longueur au moins égale à la hauteur des charges stockées ;
- Une plaque de charge informant du type de support, des dimensions, de la charge maximale des étalages et du numéro d’identification de l’installation à chaque entrée de rangée. D’autre part, il faut également placer une plaque précisant les règles de calculs appliquées, la température limite d’utilisation, le lieu et la date d’installation à l’état neuf ou reconditionné, les coordonnées du constructeur, etc.
- Un dispositif de détection d’incendie et des extincteurs faciles d’accès, en nombre suffisant ;
- Un système de ventilation et d’éclairage performant ;
- Une installation électrique aux normes, régulièrement contrôlée. La protection électrique doit être réalisée par un électricien agréé. Il est également utile de prévoir une protection de type parafoudre et des générateurs de secours en cas de coupure de courant.
La signalétique de sécurité dans les zones de stockage
Très importante, la signalétique de sécurité joue à la fois le rôle d’information et de sensibilisation du personnel. Dans un entrepôt, elle peut prendre différentes formes :
- Les panneaux de prévention incendie (panneaux d’évacuation, alarme-incendie, point de rassemblement, etc.), qui rappellent les consignes à suivre en cas de départ de flamme ;
- Les panneaux de prévention/secours, pour signaler l’emplacement d’un défibrillateur, par exemple ;
- Les bandes de couleur sur des poteaux ou les chaînes de délimitation, pour sécuriser certaines zones de stockage sensibles ou en interdire l’accès ;
- Les amortisseurs de chocs, pour recouvrir toutes les surfaces dangereuses (angles saillants, coins tranchants, etc.) et éviter ainsi les blessures ;
- Les marquages au sol, pour indiquer les zones de chargement et de déchargement de marchandises, par exemple ;
- Les panneaux d’interdiction de fumer, le plan de circulation, etc.
Bon à savoir
L’article R.125.3.1 du Code de la construction impose à ce qu’un marquage au sol composé d’une alternance de bandes jaunes et noires matérialise l’aire de débattement de portes automatiques. Ce marquage sert également à signaler les endroits où le trafic est intense et où seuls certains engins de manutention peuvent circuler.
Les règles de stockage des produits dangereux
Le Règlement européen REACH (Règlement CE nº 1907/2006) oblige l’entreprise à identifier les produits dangereux qu’elle entrepose, dans une « fiche de données de sécurité ». Leur condition de stockage est spécifique, en fonction de leur classe (9 classes de produits chimiques). Pour chacun d’entre eux, il est nécessaire :
- De respecter une distance de sécurité minimale avec les autres types de marchandises. Les matériaux inflammables et les carburants sont à stocker séparément ;
- De prévoir des conteneurs ou des récipients étanches adaptés (bacs de rétention) ;
- D’installer un système de contrôle d’humidité, de température et anti-incendie ;
- De réaliser des inspections régulières.
Le stockage des équipements de protection
Les équipements de protection assurent la sécurité des opérateurs dans leurs tâches quotidiennes. On distingue :
- Les équipements de protection collective ou « EPC » (rambarde de sécurité, balisage, garde-corps, sols antidérapants, etc.) ;
- Les équipements de protection individuelle ou « EPI » (casques, gants, ceintures de soutien lombaire, chaussures de sécurité, vêtements réfléchissants, etc.).
Ces équipements doivent être continuellement disponibles et accessibles. RS vous recommande l’installation de distributeurs automatisés ou de magasins autonomes. Ainsi, vous êtes alertés en cas de stock faible et vous n’aurez plus à vous soucier des réapprovisionnements qui deviennent automatiques. De plus, vous contrôlez les accès grâce avec l’utilisation de badges.
Les autres mesures de prévention à mettre en place
En plus des règles et conseils de stockage cités précédemment, d’autres mesures de protection peuvent être appliquées :
- Tenir un registre de sécurité relevant tous les articles stockés (dont les produits dangereux) avec leur emplacement. Ce travail peut être grandement facilité avec l’utilisation d’un logiciel de gestion des stocks ;
- Créer un comité de sécurité, composé idéalement d’un gestionnaire des produits, d’un responsable de la sécurité, d’un gestionnaire d’entrepôt, d’un responsable logistique et d’un salarié représentant le personnel. L’idée est de rassembler en interne des personnes aux compétences multiples pour identifier les problèmes de sécurité rencontrés, apporter des solutions et répondre aux besoins en formation du personnel ;
- Mettre en place des actions de prévention contre le risque d’incendie, avec un rappel de la procédure à suivre et une formation sur l’utilisation des extincteurs, selon leur classification (A, B, C, D ou K).
- Former les opérateurs sur les méthodes de stockage (capacité des rayonnages, positionnement des charges, hauteur de pose, règles de circulation, etc.) et l’utilisation des engins de manutention (transpalette, chariot de manutention, gerbeur électrique, etc.).
- Former plusieurs membres du personnel aux premiers secours. Cette formation peut être dispensée par l’association la Croix-Rouge française, par exemple.
- Sensibiliser les employés au respect des règles et au port obligatoire des EPI.
En somme, faire respecter les règles de stockage n’est pas une mince affaire. Toutefois, en élaborant un cahier des charges le plus complet possible et en consignant chaque équipement de travail, vous y parviendrez plus facilement !
(1) Source : INRS (Institut national de recherche et de sécurité).
(2) Source : ministère du Travail.
Services associés
Distributeur automatique industriel
Une solution de distribution automatique de vos produits industriels à proximité de vos lignes de production pour une meilleure gestion des stocks
Solution de stockage en bacs ouverts
Découvrez une solution dédiée à la gestion des fournitures industrielles de faible valeur et à rotation rapide
Magasin Autonome
Offrez l'accès à un magasin autonome où la gestion et le contrôle de vos consommables sont réalisés via l'Intelligence Artificielle