- Publié le 16 sept. 2024
- Mis à jour le 15 oct. 2024
- 10 min
Comment éviter les arrêts de production d'énergie ?
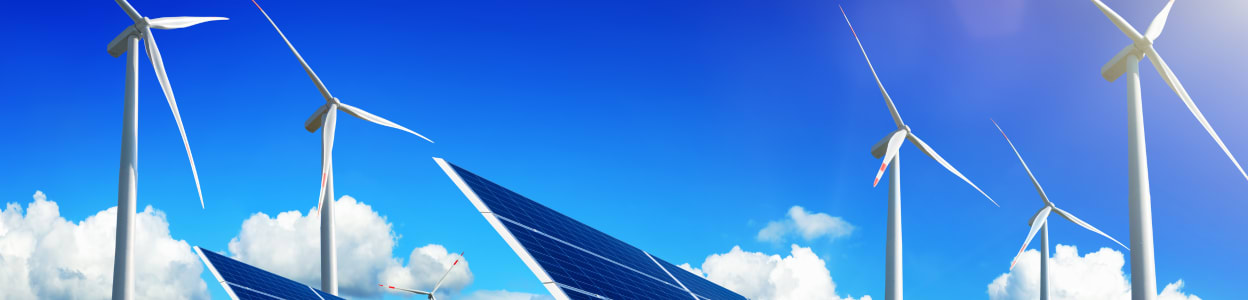
La demande énergétique mondiale a augmenté de manière significative ces dernières années, avec une croissance de +4 % en 2022 (agence internationale de l’énergie), portée par la reprise économique post-pandémie et l’augmentation des besoins en électricité. Parallèlement, aux États-Unis, les interruptions de production et les pannes non planifiées ont coûté plus de 150 milliards de dollars en 2020. De leur côté, les parcs éoliens et solaires sont confrontés à des variations importantes (-15% de production éolienne en Allemagne en 2021 du fait de conditions de vent moins favorables). Face à ces défis, les entreprises de production d’énergie doivent mettre en place des stratégies robustes pour éviter les arrêts de production, qu’ils soient causés par des défaillances techniques, des pannes de matériel ou des facteurs environnementaux.
Les différents types d'entreprise de production d'énergie
Le secteur de la production d’énergie se décline en plusieurs types d’entreprises, chacune jouant un rôle clé dans l’approvisionnement en électricité et en chaleur. Ces entreprises se répartissent en plusieurs catégories en fonction des sources d’énergie qu’elles exploitent et des technologies qu’elles utilisent pour produire et gérer l’énergie.
Les entreprises de production d’énergie conventionnelle (ou fossile)
Ces sociétés reposent principalement sur les combustibles fossiles comme le charbon, le gaz naturel ou le pétrole, mais aussi le nucléaire, qu’elles exploitent avec des centrales thermiques dans lesquelles la combustion génère de la chaleur, convertie ensuite en électricité.
Bien que ces entreprises représentent encore une part importante du mix énergétique mondial, leur contribution tend à diminuer en raison de l’impact environnemental significatif des émissions de gaz à effet de serre et la transition vers les sources d’énergie renouvelables. En France, le nucléaire représente 36,6 % de la consommation en 2023, le pétrole 30,3 % et le gaz naturel 15,5 % (source).
Les entreprises produisant des énergies renouvelables
Avec la montée en puissance des préoccupations environnementales et des politiques visant à réduire les émissions de gaz à effet de serre, les producteurs d’énergies renouvelables se sont multipliés. Ils exploitent des sources d’énergie inépuisables comme l’éolien, le solaire, l’hydraulique ou la géothermie.
On peut intégrer dans les énergies renouvelables celles produites à partir de biomasse, c’est-à-dire de la matière organique comme les déchets agricoles, le bois ou même les ordures ménagères. Ce type de production est particulièrement intéressant pour réduire les déchets tout en générant de l’énergie.
Les énergies renouvelables et la biomasse représentent 13,9 % de la consommation française en 2023 (source).
Les entreprises d’énergie de secours et de stockage de l’énergie
Elles garantissent la continuité des services énergétiques en cas de défaillance du réseau principal en installant et exploitant des générateurs de secours, souvent alimentés par du combustible fossile, pour fournir de l’énergie pendant les pannes ou en situation d’urgence. Leur importance ne doit pas être sous-estimée, notamment dans des secteurs critiques (santé, centres de données, transport...).
Le stockage d’énergie est devenu un enjeu majeur avec l’essor des énergies renouvelables. Ces entreprises développent et gèrent des systèmes capables de stocker l’énergie produite en excès pour la redistribuer lorsque la demande est forte ou la production plus faible. Les batteries lithium-ion, les volants d’inertie ou les centrales de pompage-turbinage assurent une fourniture d’énergie fiable et stabilisent les réseaux électriques.
Les arrêts de production d’énergie : des causes diverses
Les arrêts de production dans les entreprises de production d’énergie peuvent avoir de graves conséquences. Les causes sont multiples, en fonction du type d’installation, des technologies et des conditions d’exploitation.
Les pannes techniques (mécaniques, électriques et électroniques)
Les pannes mécaniques sont l’une des causes les plus fréquentes d’arrêts de production, notamment dans les installations d’énergie conventionnelle et biomasse. Elles résultent généralement de l’usure des composants (turbines, pompes, compresseurs, rotors...).
Les pannes électriques sont dues à des courts-circuits, des surtensions ou des défaillances des systèmes de câblage ou de distribution. Des coupures de courant non maîtrisées endommagent les équipements et prolongent les arrêts de production.
Les systèmes de contrôle et de gestion électronique supervisent et optimisent le fonctionnement des installations, mais ils sont sujets à des défaillances logicielles, des erreurs de communication ou des failles de sécurité. Par exemple, une panne dans le système de gestion d'une centrale éolienne peut désynchroniser les turbines du réseau et entraîner un arrêt automatique. Les infrastructures énergétiques sont par ailleurs régulièrement ciblées par des cyberattaques entraînant des conséquences dévastatrices sur la continuité de la production.
Les arrêts de production d’énergie dus à des défauts de maintenance ou à des erreurs humaines
L’entretien des installations est une cause majeure des arrêts de production. La maintenance préventive, qui consiste à inspecter et à remplacer les pièces avant qu’elles ne tombent en panne, est essentielle pour éviter les arrêts imprévus. Cependant, dans de nombreuses entreprises, la maintenance est délaissée pour des raisons budgétaires ou le manque de personnel qualifié.
Des interventions trop espacées sont susceptibles de provoquer une usure prématurée des équipements et réduire leur durée de vie.
Le facteur humain joue un rôle qu’il ne faut pas négliger : formation insuffisante, fatigue, mauvaise prise de décision, réglage imprécis suffisent à causer un dysfonctionnement et un arrêt de production. Le manque de coordination entre les équipes de maintenance et d’exploitation peut retarder la détection de problèmes potentiels et aggraver les interruptions.
Enfin, les entreprises exploitant des énergies renouvelables sont particulièrement vulnérables aux conditions météorologiques extrêmes (tempêtes, inondations, chaleur...). Mais de la simple neige ou de la poussière accumulée sur des panneaux solaires réduit aussi leur efficacité. Les centrales conventionnelles ne sont pas non plus à l’abri, comme on a pu le constater avec la catastrophe de Fukushima.
Faire face aux arrêts de production : 6 leviers à actionner
Les entreprises du secteur doivent garantir une fourniture continue et fiable tout en minimisant les pertes financières associées aux interruptions. Plusieurs stratégies permettent de réduire la fréquence et la durée de ces arrêts.
Opter pour la redondance des équipements critiques
La redondance des équipements critiques garantit la continuité de la production d'énergie, puisqu’elle consiste à installer des systèmes ou des composants en double. En cas de défaillance d'un équipement, un autre prend le relais sans interruption de service.
Par exemple, dans les centrales thermiques, avoir des turbines de secours permet de maintenir la production en cas de panne de l'unité principale. De même, dans les parcs éoliens, des systèmes de contrôle redondants assurent que les turbines continuent de fonctionner même si un des systèmes tombe en panne. Cette approche entraîne des coûts initiaux plus élevés, mais elle se justifie largement par la réduction des risques d'arrêt imprévu.
Stocker les pièces critiques
En parallèle de la redondance, le stockage de pièces critiques joue un rôle clé dans la réduction des temps d'arrêt. Disposer d'un inventaire de pièces de rechange (roulements, vannes, composants électroniques...) permet de remplacer rapidement les éléments défectueux, sans attendre les délais de livraison.
Des stratégies de gestion des stocks avancées comme le juste-à-temps (JAT) se combinent aisément avec des réserves de sécurité pour les pièces les plus critiques. Dans le secteur de l'énergie, chaque minute d'arrêt peut coûter des milliers d'euros : réduire la durée est donc essentiel.
Former le personnel à la gestion des risques
Un personnel bien formé est indispensable pour prévenir et gérer efficacement les arrêts de production. La formation continue permet aux équipes de maintenance et d'exploitation de rester à jour sur les dernières technologies et méthodes d’intervention.
La culture d’entreprise doit également intégrer la gestion des risques, avec des évaluations régulières des menaces potentielles et des simulations d'incidents. Un plan d'urgence clair et détaillé définit des procédures spécifiques pour réagir rapidement aux pannes, en incluant des protocoles de communication, des rôles et responsabilités définis et des étapes pour le rétablissement rapide de la production.
Passer à la maintenance conditionnelle ou prédictive avec la GMAO
Traditionnellement, les entreprises se contentaient de la maintenance préventive, basée sur des interventions à intervalles fixes. La maintenance conditionnelle repose sur l'état réel des équipements, évalué grâce à des inspections régulières et des capteurs qui mesurent les vibrations, la température, et d'autres paramètres.
La maintenance prédictive va encore plus loin, en utilisant des algorithmes d'intelligence artificielle (IA), le machine learning et des données historiques pour prédire les pannes avant qu'elles ne surviennent, permettant une intervention ciblée et opportune.
Pour cela, on utilise une application de GMAO (gestion de maintenance assistée par ordinateur), un outil puissant pour organiser, planifier et suivre toutes les activités de maintenance. La GMAO :
- centralise toutes les informations relatives aux équipements ;
- gère les inventaires de pièces de rechange ;
- planifie les interventions ;
- analyse les performances des équipements.
Grâce à la GMAO, les entreprises peuvent non seulement améliorer l'efficacité de la maintenance, mais aussi réduire les coûts et prolonger la durée de vie des équipements. Cet outil facilite de plus la transition vers la maintenance conditionnelle ou prédictive, en intégrant les données des capteurs et les résultats des analyses prédictives.
Surveiller en temps réel
Grâce à des capteurs connectés et à l'Internet des objets (IoT), les entreprises peuvent surveiller en continu l'état de leurs équipements et détecter immédiatement toute anomalie. Par exemple, dans les parcs éoliens, des capteurs installés sur les pales et les nacelles permettent de surveiller les vibrations, la température et l'usure, alertant les opérateurs en cas de dysfonctionnement potentiel. Ce type de surveillance permet de réagir rapidement aux problèmes émergents, souvent avant qu'ils ne provoquent un arrêt de production.
Les drones et les robots autonomes sont également de plus en plus utilisés pour inspecter les équipements dans des environnements difficiles d'accès, comme les éoliennes offshore ou les pipelines. Enfin, les jumeaux numériques, des répliques virtuelles des équipements physiques, permettent de simuler différents scénarios de panne et de tester des stratégies de maintenance avant leur mise en œuvre sur le terrain.
Faire face aux arrêts de production d'énergie nécessite une combinaison de stratégies robustes, allant de la redondance des équipements à l'utilisation des technologies les plus avancées. En adoptant une approche proactive et en restant à l'avant-garde des innovations, les entreprises peuvent non seulement limiter l’impact des interruptions, mais aussi améliorer l'efficacité opérationnelle et la rentabilité à long terme.