- Publié le 10 janv. 2023
- Mis à jour le 9 oct. 2024
- 10 min
Qu'est-ce que la maintenance prédictive et peut-elle prévenir des pannes imprévues et optimiser les opérations?
La petite histoire des types de maintenance inclut une discussion sur ce qu'est la maintenance prédictive, cette différence entre la maintenance prédictive et la maintenance préventive est fondamentale. Le déploiement de la maintenance prédictive en France en quelques chiffres, les paramètres scrutés par la maintenance prédictive ? les avantages de la maintenance prédictive ?Quelles sont les étapes pour démarrer un plan efficace de maintenance prédictive basé sur l'analyse des données ?
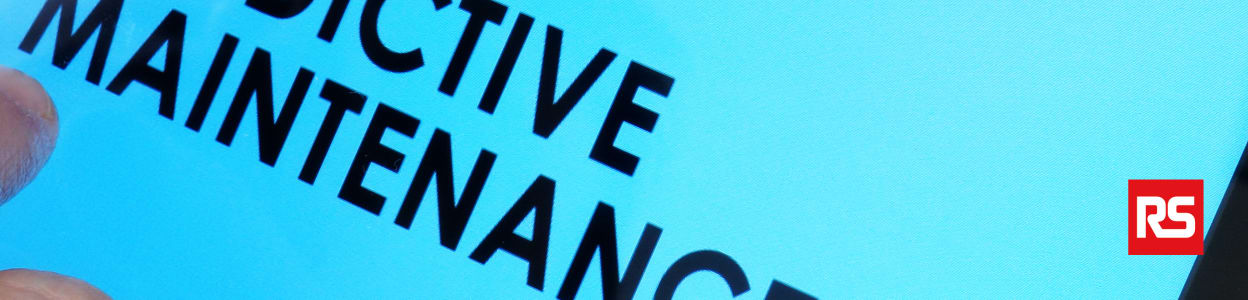
Parmi les différentes typologies de maintenance présentes aujourd’hui dans les entreprises, la maintenance prédictive est la plus récente de toutes. Les objectifs globaux d’un programme de maintenance consistent à éviter au maximum l’arrêt de la production, rationaliser les coûts et améliorer la productivité de l’entreprise. La maintenance prédictive permet une approche encore plus fine en analysant en temps réel le comportement d’un matériel pour estimer de manière plus fiable la survenue d’une panne. Focus sur la plus pro-active des maintenances, la maintenance prédictive !
La petite histoire des différents types de maintenance
Au siècle dernier, les usines de production mettaient en place une maintenance corrective, à la suite de la survenue d’une défaillance ou la détection d’une panne sur une chaîne de production. La remise en état de la machine (maintenance curative) pouvait alors générer des dysfonctionnements supplémentaires si elle n'est pas bien analysée. Des temps d’attente à cause de pièces de rechange non disponibles, et des coûts importants. En cas de dépannage provisoire, la mise en œuvre d’une stratégie de maintenance réactive peut être nécessaire. La maintenance palliative, elle**,** permettait d’attendre l’arrêt programmé suivant pour effectuer une réparation définitive.
Face au constat qu’une panne subie est désastreuse en termes de coût et de rendement de production, est alors apparue la maintenance préventive. Les opérations d’entretien sont effectuées lors des arrêts programmés, sans attendre l’occurrence d’une panne. Sont surveillés ainsi les matériels les plus sensibles du process de production.
La maintenance prédictive est une suite logique de la maintenance préventive. Elle permet d’anticiper la survenue de défaillances, non pas en fonction de la « théorie de fonctionnement » d’un composant, mais en fonction de son état réel d’usage. Il s’agit donc de mettre en place des systèmes de surveillance des matériels ayant un taux d’usure important.
Le déploiement de la maintenance prédictive en France en quelques chiffres
Selon l’Association française des ingénieurs et responsables de maintenance, la maintenance prédictive utilise l'intelligence artificielle pour prévenir les pannes. L’ia **sera présente **dans la prochaine décennie, toutes les entreprises devraient adopter une approche proactive de la maintenance.
Selon une enquête menée par l’institut de sondage international OnePoll pour Reichelt Elektronik, les trois quarts des responsables d’entreprises du secteur industriel en France l’utilisent déjà. Les entreprises doivent intégrer la maintenance prédictive dans leurs activités de production pour améliorer les performances. Parmi celles-ci, près de la moitié prévoit d’augmenter son utilisation au niveau des équipements comportant des capteurs intelligents et 44 % envisagent de traiter plus d’équipements en utilisant la maintenance prédictive.
Parmi les 25 % qui n’ont pas encore mis en place de maintenance prédictive, un peu moins d’un tiers ne l’envisage pas du tout, alors que 63 % souhaitent l’intégrer sous un délai d’un à deux ans. Elles y voient les avantages suivants :
- Limiter les arrêts de production pour 39 % est une stratégie de maintenance efficace.
- rendre leur process de production plus efficaces (38 %),
- éviter de remplacer des composants inutilement (36 %),
- faire gagner du temps aux équipes de maintenance (35%),
- améliorer la planification des travaux de maintenance (32 %).
Selon une autre étude du cabinet McKinsey, la maintenance prédictive permettrait de faire baisser les coûts de maintenance de 10 à 40 % et de diminuer de moitié le nombre de pannes de matériel.
Quels sont les paramètres scrutés par la maintenance prédictive ?
La maintenance prédictive se focalise sur le comportement en temps réel des composants à fort taux d’usure ou de ceux qui sont utilisés en dehors des plages de fonctionnement préconisées par le constructeur (ambiance radioactive ou fort taux d’hygrométrie, par exemple).
Elle mettra donc en place des surveillances telles que :
- Des capteurs de vibrations : sur des lignes de machines tournantes, toute vibration détectée peut constituer un signal de désalignement,
- Des capteurs de température : une élévation de la température peut représenter un avertissement d’un mauvais refroidissement moteur,
- Des capteurs acoustiques : ils ont pour but de détecter un manque de lubrification ou l’usure d’un roulement.
Quels sont les avantages de la maintenance prédictive ?
Grâce à son caractère anticipateur, la maintenance prédictive présente des avantages indéniables.
Réduction des durées d’arrêt de production
Dans la mesure où elle permet aux intervenants de détecter les problèmes très en amont pour les résoudre avant toute panne, les durées d’arrêt sont ainsi considérablement réduites et optimisées, toute casse brutale étant rendue moins probable. La diminution du nombre de pannes permet de diminuer les temps d’immobilisations des matériels, avec les répercussions qui en découlent au niveau financier.
Améliorer de la productivité des équipes
Étant donné que les défaillances machines seront plus rares, les intervenants perdront moins de temps sur des tâches inutiles, ce qui augmentera la productivité globale.
Diminution des coûts d’intervention des services d’entretien
L’anticipation de l’entretien permet de faire des économies substantielles et contribue ainsi à augmenter le retour sur investissement. La gestion des pièces de rechange est également facilitée, ce qui implique une diminution globale des coûts de maintenance.
Amélioration de la conception du produit
L’allongement de la durée de vie des matériels entraîne une hausse de leur fiabilité, et donc une optimisation du process de production.
Contribution à une meilleure sécurité pour les salariés
La maintenance est effectuée par les équipes avant qu’une casse ne rende une ligne de production dangereuse pour les opérateurs intervenant à proximité, ce qui renforce la sécurité des travailleurs.
Définition de la maintenance prédictive
La maintenance prédictive est un type de maintenance avancé qui repose sur l’analyse des données en temps réel issues des équipements pour prévoir les défaillances avant qu’elles ne surviennent. Contrairement à la maintenance corrective, qui intervient après une panne, ou à la maintenance préventive, qui se base sur des calendriers d’intervention prédéfinis, la maintenance prédictive utilise des technologies telles que l’intelligence artificielle et le machine learning pour anticiper les problèmes potentiels. Grâce à la maintenance prédictive, les capteurs intelligents installés sur les machines permettent de collecter des informations comme les vibrations, la vitesse de rotation, et les changements de température, permettant ainsi de détecter les signes avant-coureurs d’un dysfonctionnement.
En tant que stratégie de maintenance proactive, la maintenance prédictive vise à optimiser la durée de vie des équipements tout en réduisant les coûts de maintenance. En analysant les données transmises par les capteurs et en modélisant les comportements à risque à l’aide d’algorithmes prédictifs, cette approche offre un retour sur investissement significatif. Selon une étude du cabinet McKinsey, la maintenance prédictive permet de réduire de 10 à 40 % les coûts d'entretien et de diminuer de 50 % le nombre de pannes, améliorant ainsi les performances globales des systèmes de production.
Exemples de maintenance prédictive
Les exemples de maintenance prédictive sont nombreux et illustrent l’efficacité de cette méthode dans diverses industries. Dans le secteur de l’énergie, les parcs éoliens utilisent des capteurs de vibrations pour surveiller en permanence les turbines. En analysant ces données, les opérateurs peuvent détecter des anomalies telles qu’un désalignement des pales ou des problèmes au niveau des roulements, ce qui permet d’intervenir avant que la panne ne survienne. Grâce à la maintenance prédictive, les arrêts imprévus sont considérablement réduits grâce à une stratégie de maintenance prédictive, assurant une production continue et une gestion optimisée des ressources.
Dans le secteur industriel, des innovations en matière de maintenance prédictive sont essentielles. capteurs de température et des capteurs acoustiques sont souvent utilisés pour surveiller les moteurs et autres équipements rotatifs. Un léger ajustement dans la stratégie de maintenance prédictive peut avoir un impact significatif. Le changement de température ou un bruit inhabituel peut indiquer une usure excessive ou un manque de lubrification. En détectant ces signaux à temps, les techniciens peuvent planifier les travaux de maintenance de manière plus précise, évitant ainsi des interruptions coûteuses de la chaîne de production. L'internet industriel des objets (IIoT) joue également un rôle crucial dans ces projets, car il permet de connecter et d'analyser les machines à distance, garantissant une surveillance en continu et une réponse rapide en cas d'anomalie.
Quelles sont les étapes pour démarrer un plan efficace de maintenance prédictive ?
Clé n°1 : disposer de l’accord de la Direction
Même si cela peut paraître trivial, la mise en œuvre d’un plan de maintenance va mobiliser de nombreuses ressources dans l’entreprise (humaines, financières) et le budget associé peut s’avérer conséquent !
Clé n°2 : rassembler les données indispensables à la maintenance prédictive
Cette étape cruciale consiste à établir un inventaire détaillé des équipements critiques pour la production. Il est essentiel de lister les matériels ayant un historique de défaillances élevées avec leurs causes pour assurer une gestion efficace de la maintenance prédictive. Pour chaque équipement essentiel à la production dont les coûts de réparation sont élevés, il faut répertorier :
- la fréquence des pannes et les durées d’utilisation,
- L'analyse des données historiques est essentielle pour la stratégie de maintenance prédictive.
Les sources d’information sont nombreuses : des documents du constructeur aux logiciels internes, en passant par les connaissances mémorisées par les plus anciens collaborateurs.
Clé n°3 : effectuer l’analyse des modes de défaillance AMDEC (Analyse des Modes de Défaillance de leurs Effets et de leur Criticité)
Grâce à l’analyse des actifs critiques, les modes de défaillance doivent être identifiés, en particulier les défaillances qui occasionnent les plus gros impacts sur la production et celles qui ont la plus forte probabilité d’occurrence.
Clé n°4 : installer les capteurs de surveillance IoT
Cette mise en œuvre s’effectue à partir des analyses d’anticipation de défaillances des matériels. Pour aller encore plus loin, des systèmes de « machine learning » ajoutent de nouveaux schémas d’anomalie grâce aux informations déjà collectées. Ces capteurs intelligents identifient en continu l’apparition de signes préalables à une défaillance, comme des vibrations anormales ou une élévation de température.
Clé n°5 : développer des algorithmes prédictifs
L’étape suivante consiste à travailler avec des « data scientists » Il est essentiel de développer des algorithmes prédictifs de maintenance en utilisant l'internet des objets pour surveiller les équipements. Ils s'appuient sur les mesures des capteurs IoT et les analyses précédentes pour concevoir la modélisation des phénomènes de défaillance.
Clé n°6 : disposer des bons outils de maintenance prédictive
On ne le redira jamais assez, mais un bon logiciel de GMAO est la base de la réussite d’un tel projet. Des compétences informatiques dans l’entreprise sont donc nécessaires, surtout pour travailler sur les autres outils tels que :
- Les capteurs IoT, qui surveillent les machines en continu,
- La plateforme IoT, qui collecte les données,
- L’application qui prévient en temps réel les intervenants de maintenance.