- Publié le 9 janv. 2023
- Mis à jour le 10 oct. 2024
- 9 min
Mise en œuvre d'un plan de maintenance préventive efficace
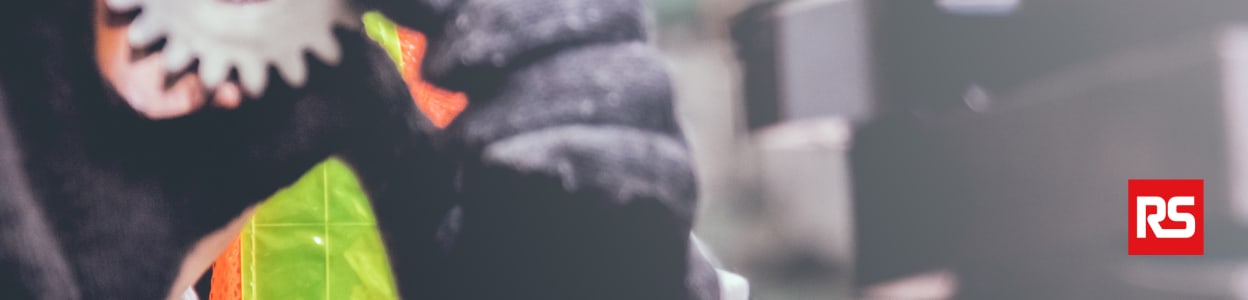
Depuis le début des années 1990, la concurrence industrielle s'est fortement intensifiée. Les critères de coût, qualité et délais ne suffisent plus pour optimiser les stratégies commerciales des entreprises. Avec la nécessité supplémentaire des contraintes réglementaires, la pérennité d'une entreprise nécessite aujourd'hui une grande réactivité au niveau de la production. La maîtrise de ses outils et des coûts de production est ainsi devenue un enjeu majeur. Ces besoins d’un genre nouveau ont un impact fort sur la maintenance des lignes industrielles. De curative, la maintenance est progressivement devenue préventive, intégrant des éléments de maintenance prédictive. Le besoin d'outils de surveillance et de diagnostic se révèle ainsi indispensable. Découvrez comment la GMAO est-elle devenue un pilier de la maintenance préventive ? Voici quelques explications.
Les 4 objectifs de la maintenance préventive
Les lignes de production d’une entreprise industrielle nécessitent de respecter les quatre composantes suivantes : un bon planning de maintenance préventive, la gestion de maintenance, la formation des équipes et l'optimisation des ressources :
- Moins de défaillances, de manière à réduire les interventions urgentes ;
- Moins de dépenses, pour minimiser le coût global de production ;
- Plus de disponibilité, pour obtenir un rendement maximum ;
- Une meilleure qualité de service, afin de satisfaire les exigences client.
Le respect de ces objectifs nécessite ainsi la mise en place de procédés de maintenance préventive.
Les principales techniques en maintenance préventive
Elle concerne principalement les machines tournantes ; des relevés vibratoires permettent d'identifier une éventuelle dégradation du matériel avant la survenue d'un incident. Selon le niveau vibratoire relevé, une possible détérioration du matériel peut être anticipée.
L'analyse thermographique
Grâce à des mesures par caméra thermique, elle permet de mesurer l'intensité du rayonnement infrarouge d'un matériel. La détection d'un échauffement de composants permet d'identifier un dysfonctionnement et d'anticiper la survenue d'une panne.
L'analyse des fluides lubrifiants
Elle permet de faire apparaître des phénomènes de contamination ou de pollution (morceaux de métaux provenant d'une usure prématurée, par exemple).
Quelles sont les différentes opérations de maintenance préventive ?
Il existe quatre types d’opérations principales de maintenance préventive.
- Les opérations de surveillance: elles consistent en des relevés de paramètres de fonctionnement.
- Les opérations d’entretien: il s’agit d’opérations simples telles que le remplacement d’un filtre, le graissage de joints ou la vidange de l’huile moteur.
- La révision d’un matériel: ces opérations peuvent nécessiter un diagnostic de panne.
- La réparation: il s’agit d’opérations complexes, réservées à des techniciens spécialisés et dotés d’outillages spécifiques.
La gestion des pièces de rechange
Il est excessivement important pour une entreprise de production d'avoir une bonne gestion de stock des pièces détachées. Il s’agit là d’un exercice d'optimisation qui permet de disposer in situ des matériels critiques pour la production, sans stocks importants. Il est possible d'appliquer à la gestion des stocks le principe de Pareto : 20 % des matériels en stock sont les plus demandés et permettent de maintenir 80 % de l'activité de l’entreprise.
Là encore, un logiciel de GMAO adapté à la gestion des pièces de rechange est indispensable pour conférer à l'entreprise une réelle efficacité de sa maintenance préventive.
La gestion des pièces de rechange peut se baser sur 2 indicateurs :
- MTTR (Mean Time To Repair), c'est-à-dire le temps moyen de la réparation ;
- MTBF (Mean Time Between Failure), qui est le temps moyen entre 2 pannes.
Le MTTR est un indicateur de la capacité de l'entreprise à intervenir vite sur des pannes potentiellement coûteuses. Pour réduire le MTTR, il est indispensable de comprendre pourquoi la panne survient, de mettre l'accent sur la surveillance et d'élaborer un plan d'actions pour y remédier.
Un autre moyen d'optimiser la gestion des stocks est d'utiliser la démarche d'amélioration continue LEAN, qui comporte aussi un volet d’optimisation des pièces de rechange.
La planification des opérations
La création de la planification des opérations de maintenance préventive s’effectue via un logiciel de GMAO performant et adapté aux besoins de l’entreprise. Les différentes étapes sont les suivantes.
- Créer un événement: choisir sa périodicité, son nombre d’occurrences, le matériel concerné et l’échéance. La fréquence est déterminée à partir de toutes les données de fonctionnement à disposition sur chaque matériel.
- Pour chaque événement identifier l’intervenant concerné, le temps prévisionnel d’intervention et le temps d’arrêt prévu de l’installation. Il est nécessaire d’y adjoindre la documentation d’intervention adéquate, qui constituera le document opérationnel pour le technicien qui interviendra in situ.
Une fois tous les événements identifiés et saisis dans le logiciel de GMAO, une synthèse de toutes les opérations pourra en être extraite, associée au planning d’intervention. Les arrêts de production sont ainsi préparés par extraction des informations saisies précédemment dans le logiciel, sur la période de l’arrêt donné. Au quotidien, les techniciens de maintenance auront donc des tâches de maintenance préventive à réaliser selon un planning donné.
L’organisation de la maintenance préventive en cas de sous-traitance et les freins associés
Selon les chiffres de l’AFIM (Association Française des Ingénieurs et responsable Maintenance), le secteur de la maintenance industrielle représente l’équivalent de 22,6 milliards d’euros de dépense dans l’industrie, soit 2,3 % de la production en valeur. Plus d’un tiers de ces dépenses (8,5 milliards d’euros) est sous-traité à des prestataires de maintenance industrielle indépendants.
Sous-traiter la maintenance industrielle de son site à un prestataire comporte des risques. Les opérateurs de maintenance prestataires, qui se déplacent de site en site, peuvent ne pas être disponibles au moment d’intervenir sur une intervention. Cela représente également un risque de perte de compétences pour l'entreprise principale, qui perd la maîtrise de son outil industriel. Il est cependant possible d'envisager de sous-traiter certaines opérations techniques à faible valeur ajoutée. En cas de sous-traitance d’une opération élémentaire, il est indispensable que les équipes prestataires intervenantes interviennent en présence du technicien de maintenance de l'entreprise.
Dans le cas d'une sous-traitance globale de la totalité d'un service maintenance, un contrat doit être rédigé. Il comporte des obligations de moyens de la part du prestataire ainsi que des obligations de résultat.
Vous souhaitez en savoir plus sur ce sujet ? Vous trouverez des informations complémentaires sur la maintenance préventive.
Pourquoi mettre en place un plan de maintenance préventive ?
La mise en place d'un plan de maintenance préventive est une étape cruciale pour toute entreprise industrielle cherchant à optimiser la gestion de ses équipements. En effet, un plan de maintenance bien conçu permet de prolonger la durée de vie des machines tout en réduisant les pannes imprévues, qui sont souvent coûteuses et perturbent le planning de production. Par exemple, selon une étude du cabinet McKinsey, la maintenance préventive peut réduire de 10 à 40 % les coûts liés à des interventions correctives, tout en augmentant la disponibilité des équipements est cruciale pour la planification de la maintenance préventive. de 20 %.
Un logiciel de GMAO Un logiciel de maintenance performant est indispensable pour gérer efficacement les différentes opérations de maintenance. opérations de maintenance et anticiper les besoins en pièces de rechange. Ce type de solution permet d’organiser les tâches de maintenance en fonction des données recueillies par les capteurs, dans le cadre d’une maintenance conditionnelle ou prédictive, et d'optimiser ainsi la charge de travail des équipes techniques.
Optimiser la maintenance des équipements avec la maintenance préventive conditionnelle
La maintenance préventive conditionnelle est une sous-catégorie de la maintenance préventive qui s'appuie sur la surveillance continue des équipements. Grâce à des outils de mesure avancés comme l'analyse vibratoire ou la thermographie, les opérateurs peuvent identifier les signes avant-coureurs de dégradations et planifier les interventions de maintenance selon une stratégie de maintenance prédictive ciblée.
Ce type de maintenance efficace réduit non seulement les coûts de réparation, mais permet également de maximiser la durée de vie des machines tout en minimisant les interruptions de production.
Par exemple, la détection précoce d'un problème grâce à un suivi vibratoire permet de planifier une opération de maintenance avant qu'une panne ne survienne, ce qui réduit le temps d'arrêt imprévu et optimise les opérations La gestion de maintenance au sein de l'entreprise est essentielle pour assurer la continuité des opérations. Une étude de l'AFIM montre que les entreprises adoptant une maintenance préventive systématique voient leurs pannes diminuer de 25 %, tout en augmentant la productivité de leurs installations.
Comment un logiciel de GMAO optimise les opérations de maintenance
Un logiciel de GMAO est indispensable pour coordonner toutes les opérations de maintenance. Il permet de planifier les tâches de maintenance à l’avance, en tenant compte des types de maintenance préventive à effectuer sur chaque équipement. En plus d'améliorer la gestion des interventions, un tel outil permet d’ajuster le planning en fonction des besoins réels et de réduire les pannes imprévues. En intégrant des indicateurs clés comme le MTTR (Mean Time To Repair) et le MTBF (Mean Time Between Failure), les responsables peuvent suivre la performance des équipements et optimiser la gestion des ressources.
En conclusion, mettre en place un plan de maintenance préventive est essentiel pour garantir la fiabilité des équipements et la pérennité de la production. En adoptant une approche méthodique, basée sur la maintenance conditionnelle et prédictive, les entreprises peuvent à la fois réduire leurs coûts et prolonger la durée de vie de leurs machines.
Vous souhaitez en savoir plus sur ce sujet ? Vous trouverez des informations complémentaires sur la gestion de maintenance et la disponibilité des équipements.maintenance préventive.
Service & Produits associés
Sécheur à adsorption
Les lubrificateurs d'air pneumatiques sont utilisés pour injecter un flux d'huile en aérosol dans une ligne d'air.
Filtres régulateurs
Les filtres régulateurs lubrificateurs, sont conçus pour fournir un débit d'air propre dans les applications pneumatiques.