- Publié le 5 déc. 2024
- Mis à jour le 5 déc. 2024
- 7 min
Maintenance des systèmes de filtration dans la production pharmaceutique
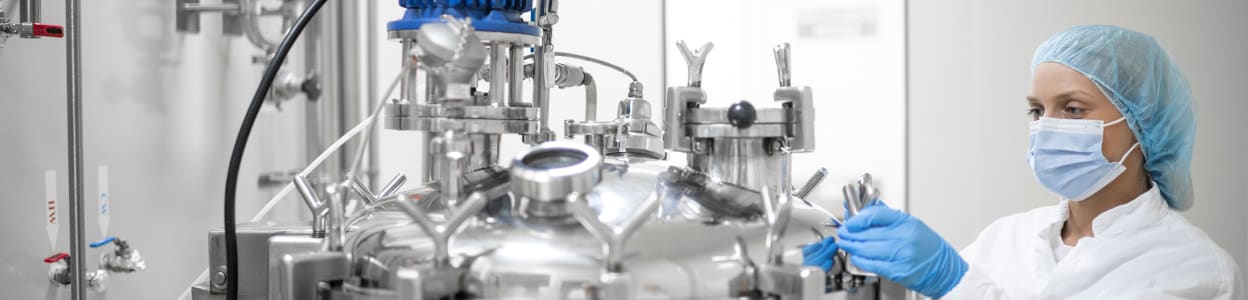
Les exigences en matière de filtration concernent divers aspects, allant de la fabrication des principes actifs pharmaceutiques (API) à la gestion des utilités comme l'eau, les gaz et la vapeur. Dans un contexte de fabrication de produits pharmaceutiques, l’entretien et la maintenance de tels systèmes sont fondamentaux
Dire que dans l'industrie pharmaceutique la propreté et la qualité des produits finis sont des enjeux cruciaux, notamment en matière de sécurité des patients, est un pléonasme. Ces exigences sont à la fois encadrées par des réglementations strictes, des organismes d’accréditation pour la mise sur le marché d’un médicament mais aussi les opérations de contrôle qualité effectuées sur les emballages, les flacons ou les produits finis avant leur commercialisation. Surtout, les conséquences d’un problème de santé quelconque sur un consommateur ou un patient peuvent se révéler désastreuses pour l’entreprise responsable d’une négligence quant au respect des règles d’hygiène tout au long du process.
Parmi les éléments de ce process faisant l’objet de toutes les attentions figurent bien entendu les machines et les équipements de production, les équipements de protection mais aussi les différents éléments composant l’usine. C’est le cas des systèmes de filtrations, qui jouent un rôle central.
Les systèmes de filtration : un élément essentiel dans le maintien de la qualité du process
Les processus de filtration et de séparation sont essentiels dans la mesure où ils assurent la pureté et la sécurité des médicaments destinés aux patients et aux consommateurs. Concrètement, les systèmes de filtration sont utilisés afin d’éliminer les particules, les contaminants microbiens et les endotoxines. Ils garantissent également que les produits pharmaceutiques respectent les normes de qualité imposées par les réglementations.
Il existe plusieurs types de systèmes de filtration, que ce soit des filtres à profondeur chargés de capturer les particules dans des couches filtrantes ou les filtres membranaires utilisés pour la filtration précise des liquides, y compris l’ultrafiltration et la microfiltration. De leur côté, les filtres HEPA et ULPA servent à assainir l'air dans les environnements critiques comme les salles blanches. Enfin, le charbon actif est quant à lui chargé d’éliminer les contaminants organiques. Celui-ci est de plus en plus présent dans le process du fait de sa capacité à éliminer les impuretés colorées pouvant apparaître au moment de la synthèse.
De manière générale, tous ces systèmes répondent à de multiples défis comme la filtration des endotoxines dans les réseaux d'eau grâce à des filtres à membranes à fibres creuses, la filtration des substances issues de cultures microbiennes – comme les antibiotiques –, des solvants pour la production d'API ou des gaz stériles. Les filtres ont également pour mission d’assurer la protection des produits contre les contaminations externes de systèmes comme les autoclaves, d’éliminer les impuretés et autres particules ou encore de filtres la vapeur afin de désinfecter les installations et garantir la bonne préparation de l'eau stérile utilisée pour les formulations.
Une réglementation stricte, y compris dans le domaine de la filtration
Avant même d’évoquer la filtration, rappelons que l’industrie pharmaceutique est encadrée par l’Agence nationale de sécurité du médicament et des produits de santé (ANSM) et des normes strictes s'appliquant à toutes les étapes, de la recherche à la production finale en passant par le conditionnement. Objectif ? Garantir la qualité et la sécurité des médicaments à travers le respect de la directive européenne 2003/94/CE et du Règlement (UE) n° 2017/745 sur les dispositifs médicaux.
Autre règlement européen concerné : le n° 2017/746 sur les dispositifs médicaux de diagnostic in vitro ; celui-ci précise les exigences relatives aux bonnes pratiques de fabrication (BPF) et à la qualité. Concernant les BPF – ou GMP (Good Manufacturing Practices) – celles-ci instaurent des lignes directrices assurant une fabrication à la fois cohérente et contrôlée et, in fine, la qualité des matières premières, des équipements et des installations, le respect des procédures opérationnelles standardisées (SOP) à chaque étape de production ainsi que des exigences d'hygiène strictes.
En matière de filtration cette fois, le secteur pharmaceutique exige que la totalité des filtres et des systèmes de filtration soient traçables, avec une fabrication en salle blanche et des procédures rigoureuses. Notons en effet que plusieurs normes et réglementations définissent les critères à suivre quant aux niveaux de propreté des salles blanches et des environnements contrôlés, y compris les exigences pour les systèmes de filtration d'air. De la même manière, l’ISO 14644 – définissant les BPF – inclut des exigences portant sur l'intégrité des systèmes de filtration et le respect des conditions d'hygiène empêchant toute contamination ; c’est le cas également des GEP qui établissent des bonnes pratiques d'ingénierie appliquées dans la conception et l'entretien des systèmes de filtration dans les installations pharmaceutiques.
Rappelons également que l’ISO 14644 concerne la filtration de l’air en salles blanches et porte donc à la fois sur les centrales de traitement d’air et de la multitude de systèmes de filtration allant de l’air entrant (préfiltres pour les poussières) avant l’échange de chaleur, l’humidificateur puis le ventilateur, jusqu’au filtres HEPA et ULPA (soit des filtres allant de H14 à H17) et le filtre à air final pour l’air neuf (ou air pur) destiné à la salle blanche.
L’entretien et la maintenance au centre de toutes les attentions
Mais qu’en est-il justement de l’entretien et de la maintenance d’un produit aussi technique que stratégique pour le process ? Déjà, avant même l’installation de systèmes de filtration, afin de faciliter les opérations de maintenance, veiller à toujours le rendre accessible, à la fois pour l’inspection et son remplacement. Dans les salles blanches par exemple, le filtre à air doit être positionné à l'extérieur.
Dans un environnement industriel dans lequel le non-respect des règles d’hygiène et de sécurité peut être lourd de conséquences, l’entretien des filtres relève de la maintenance préventive. Celle-ci consiste avant tout à effectuer des inspections régulières et des remplacements selon un calendrier établi par le fabricant. Ainsi, l’équipe de maintenance doit procéder à une vérification des performances en suivant les pressions différentielles afin d’identifier toute obstruction. Elle se charge de l’entretien et du nettoyage des systèmes de manière à éviter toute contamination croisée et, le cas échéant, au remplacement des filtres.
Mais la maintenance préventive inclut également les tests d’intégrité du système, de rétention et de débit, rendus possibles par des méthodes et des instruments de contrôle non destructif (CND), permettant d’identifier des signes d’obturation ou de rupture du filtre. C’est le cas par exemple des filtres stérilisants (hydrophiles ou hydrophobes). Même si cette opération de test s’effectue avant la filtration d’un équipement avant la mise en production, elle doit aussi être menée à l’issu du process afin d’en identifier les éventuels signes de défectuosité.
Parmi ces méthodes figurent le test du point de bulle – la méthode la plus utilisée –, le test consistant à mesurer le débit de gaz ou encore le test d’intrusion d'eau. Celles-ci peuvent être effectuées à l’aide de différents équipements et instruments de CND (endoscopie, ultra-son, analyse microbienne, de particules ou de contamination, colorimétrie, thermographie infrarouge, tests électriques de conductivité ou encore résonance magnétique…).
Enfin, l’usage de capteurs permettant de surveiller la pression, la température ou encore le débit des fluides ou de l’air traversant le filtre se généralise. Plus que du préventif, ces méthodes relèvent de la maintenance conditionnelle voire prévisionnelle dans la mesure où une surveillance en temps réel rend possible la détection d’anomalies et une prise de décision bien mieux anticipées.