- Publié le 10 janv. 2023
- Mis à jour le 15 janv. 2025
- 19 min
L'Internet Industriel des Objets (IIoT) : De la maintenance prédictive à l'intelligence artificielle
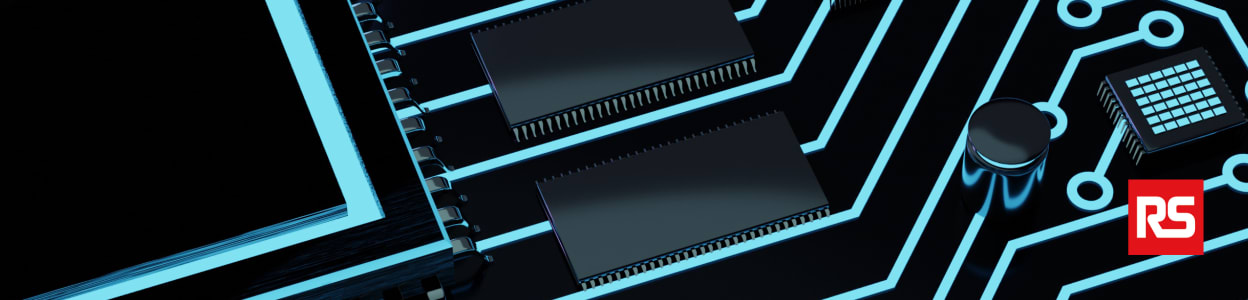
Les équipements industriels génèrent une variété de données. L'analyse de certaines de ces données par des outils logiciels dédiés visent à fournir des informations et des indicateurs permettant d’optimiser la production, de doper les performances des processus industriels, de mettre en place un système de maintenance prédictive ou de déterminer des taux de rendement synthétique (TRS). L’échange des données entre les systèmes de pilotage des machines et les systèmes informatiques de niveau supérieur n’est cependant pas aussi simple qu’il n’y paraît. Les passerelles IIoT (Industrial Internet of Things) sont justement conçues pour simplifier la liaison entre l'univers des technologies opérationnelles (OT) et celui des technologies informatiques (IT).
Dans l’industrie, les machines sont, pour la plupart et depuis longtemps, connectées à des solutions logicielles de supervision de la production, des systèmes MES (Manufacturing Execution System) qui permettent de contrôler les processus de fabrication aux différentes étapes de production et à d'autres applications logicielles de surveillance et de gestion des process de fabrication.
Mais aux côtés des équipements récents, dotés d'interfaces numériques de transmission de données, sont également exploitées dans les ateliers des machines plus anciennes qui mettent en œuvre des liaisons de communication analogiques ou qui en sont complètement dépourvues.
Pour rappel, selon une étude Accenture sur l’industrie en France présentée par l’Alliance Industrie du Futur et les organisations professionnelles Gimelec et Symop, l’âge moyen du parc productif qui était de 19 ans en 2012 est passé à 17 ans ces dernières années. Dans ce contexte, il est particulièrement difficile pour un industriel de mettre en œuvre une application IIoT (Internet Industrial of Things) et de connecter ses équipements de production d'ancienne génération afin d'en surveiller et optimiser le fonctionnement, d'en améliorer le rendement, de planifier des interventions de maintenance…
Cependant, qu’elles soient d’anciennes ou de nouvelles générations, les machines génèrent toutes une variété de données. Le principal défi des applications IIoT est d’extraire ces données, parfois inutilisées, les collecter et les transmettre pour une analyse locale ou sur des plates-formes Cloud via des applications de traitement dédiées. Ces données peuvent provenir des capteurs, actionneurs et autres systèmes de commande qui pilotent et assurent le fonctionnement des machines. Il peut s'agir de simples contrôleurs en passant par les automates plus sophistiqués et des variateurs pilotant des moteurs, jusqu’aux commandes numériques indispensables à de nombreuses machines-outils. En outre, la variété des bus de terrain et réseaux industriels exploités par les machines ne facilite pas la transmission et la centralisation des données. Ces données sont souvent disponibles dans des formats distincts. Ce qui rend délicat leur exploitation.
Définir un objectif intelligent avec l'iot industriel
Pour mettre en œuvre un projet IIoT, il ne vaut mieux pas se focaliser dès le départ sur les moyens de connexion et d’analyse de données mais avant toute chose d’identifier les machines à connecter, les données à collecter, les bus et les protocoles de communication en présence… Et surtout, de déterminer quel est l’objectif du projet IIoT. Il peut s'agir par exemple d'augmenter la disponibilité machine, d'optimiser la performance production, de réduire la consommation d'énergie, de maîtriser la maintenance, d'améliorer la qualité des produits, d'analyser des données... Un audit de connectivité peut se révéler indispensable afin d'établir précisément comment sont connectées les machines, par quels moyens et à l'aide de quelles technologies elles communiquent, à quels systèmes informatiques les données machines sont (ou peuvent être) rapatriées... Ce qui permettra d'établir un cahier des charges qui dictera le choix des solutions techniques les plus pertinentes.
Une fois l’audit de connectivité réalisé et que les objectifs du projet IIoT ont été spécifiés, il est alors temps de s’intéresser aux choix techniques concernant le matériel de collecte et d’exploitation de données ainsi que les outils logiciels de traitement et d’analyse des données qui pourront être déployés localement ou de façon déportée sur des plates-formes Cloud. Il est difficile de trouver sur le marché une solution sur étagère qui répond aux particularités du processus et des machines d'un industriel. Mais ce dernier pourra s’appuyer sur le savoir-faire et les solutions des fournisseurs d'automatismes et d'équipements industriels qui pourront l'accompagner et lui fournir des briques technologiques essentielles en matière de récupération de données de production, de nœuds de connectivité et de protocoles industriels pour concevoir une solution répondant aux exactes attentes de son projet IIoT.
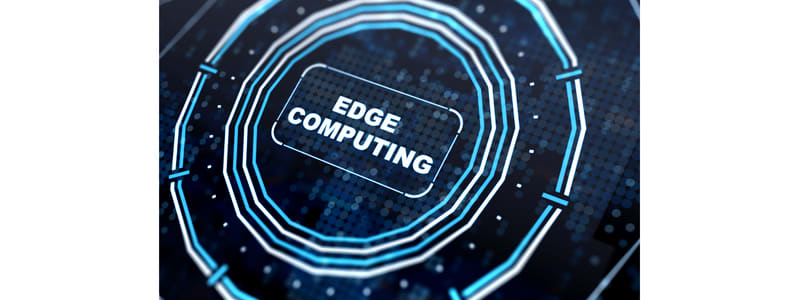
Solutions de connectivité pour l'industrie 4.0
Il existe aujourd'hui sur le marché un large choix de solutions pour connecter n’importe quel équipement industriel ou base de données IT : des passerelles IIoT (collecte la donnée et transmission vers cloud, base IT…) en passant sur les modules d’Edge Computing (collecte et exploitation de la donnée localement via des applicatifs intégrés) jusqu’aux fonctions IIoT intégrées directement dans les automates, commandes numériques et autres Panel PC.
Les données peuvent être exploitées localement en temps réel via des systèmes d’Edge Computing installés sur ou aux pieds des machines et traitées par des applications dédiées avec la possibilité d’envoyer les données agrégées dans une plate-forme Cloud. Diverses applications Cloud permettent notamment l’archivage des données, leur comparaison entre différents sites industriels, leur analyse sur le long terme. Certaines d'entre elles sont dédiées à la surveillance de moteurs ou d'une machine spécifique et à des problématiques industrielles propres à un équipement ou un processus particuliers. Elles collectent et traitent les données afin de fournir des indicateurs permettant de doper les performances des processus industriels, de mettre en place un système de maintenance prédictive ou de déterminer des taux de rendement synthétique (TRS).
L’industriel pourra ainsi disposer de tableaux de bord lui permettant de surveiller les paramètres clés de ses process industriels. Il pourra alors se baser sur ces paramètres pour le guider dans ses choix afin de prendre les décisions les plus appropriées pour améliorer ses procédés. Automatiser la remontée des informations provenant des équipements de production et les transmettre en temps réel permet par exemple d’anticiper l’usure et le remplacement de certaines pièces, d’être immédiatement averti d’une rupture de charge ou d’un dysfonctionnement, de prévoir et de gérer les évolutions de la production.
Les passerelles IIoT
La collecte et le transfert de ces données vers des outils décisionnels n'est cependant pas si simple. Ces opérations peuvent être rendues complexes par la diversité des bus de terrain industriels exploités par les machines. Heureusement, la plupart des automates et systèmes de contrôle sont désormais dotés d'une Ethernet via laquelle les machines peuvent communiquer. Ce qui permet le transfert des données vers les systèmes informatiques de niveau supérieur dédiés à la gestion et à la supervision de la production, au suivi de la qualité, à l’organisation de la maintenance...
Il existe une grande variété de bus de terrain : Foundation Fieldbus, CIP, Profibus, CC-Link, EtherCAT, Modbus, etc. A cette diversité s'ajoute la variété des formats de données à collecter. Ce qui ne simplifie pas leur acquisition et leur transfert. Il est donc souvent nécessaire de connecter l’automate à une interface matérielle chargée de la mise en forme des données dans un format exploitable par les systèmes informatiques industriels. Ce qui réclame une expertise dans le domaine des automatismes ainsi que celui de l'informatique. Pour simplifier ces opérations, les fournisseurs de solutions d’automatisme ont donc développé des passerelles qui permettent de relier les automates pilotant les machines et équipements de production aux systèmes informatiques industriels.
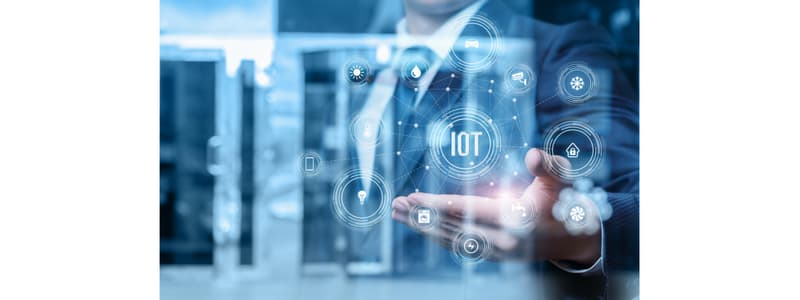
Convergence OT/IT
Ces passerelles IIoT (Industrial Internet of Things) visent à assurer la convergence des technologies opérationnelles (OT) et des technologies informatiques (IT). Elles offrent des outils et des entrées/sorties grâce auxquels les automaticiens vont pouvoir sélectionner les variables à collecter, définir leur fréquence d’acquisition et de transmission, et spécifier vers quels systèmes, sous quel format et à quel rythme les transmettre. Le processus de configuration est, selon leur fournisseur, à la portée des automaticiens sans expertise informatique spécifique et ne nécessite pas de programmation par un langage codé. A l’inverse, ces passerelles IIoT permettent aux informaticiens de se plonger plus aisément dans l'univers des automatismes.
Une telle passerelle IIoT intègre en général le connecteur dédié aux principaux automates du marché, afin de permettre l’accès aux données de la machine sans modifier son programme de fonctionnement ni écrire une seule ligne de code. Sa configuration s’effectue en s’y connectant avec un ordinateur localement ou à distance via le réseau. Il suffit de sélectionner les données que l'industriel souhaite collecter, le traitement à leur appliquer et de définir leur destination qu’il s’agisse d’une application logicielle industrielle, tournant sur un serveur dédié ou une plate-forme Cloud.
Capacités de communication et de traitement
Ces passerelles IIoT sont disponibles en différentes variantes. Leur processeur, leur profondeur mémoire, et leurs capacités de traitement embarqués sont adaptés à l’application et à la quantité de variables à collecter. Pour éviter la transmission d’une trop importante quantité de données et de surcharger le réseau de communication, il leur est possible de réaliser certains traitements localement. Elles sont ainsi capables de réaliser la mise à l’échelle des variables et la mise en forme des données dans un format approprié, d’effectuer des calculs statistiques ou mathématiques, de filtrer des signaux, d’envoyer une alerte lors de dépassement de seuil... Elles pourront par exemple déterminer la consommation énergétique d’une cellule robotisée via les mesures de courant et de tension ainsi que le temps de cycle machine ou surveiller le couple d’un moteur par rapport à la position de son axe afin d’identifier un problème cinématique.
Au final, les passerelles IIoT alimentent en données issues du terrain les outils logiciels d’analyse et de surveillance qui délivreront des indicateurs aux industriels afin d’optimiser en temps réel les performances de leur process et la maintenance de leurs équipements. La collecte et l’évaluation des données opérationnelles localement ou à distance via des applications d’analyse spécifiques tournant sur des plates-formes Cloud ou des serveurs dédiés rend possible la mise en place d’interventions de maintenance prédictive (ce qui permet de s’affranchir de la maintenance de la machine à intervalles prédéfinis), et d’optimiser son utilisation et sa productivité, et par conséquent, de réduire les coûts et les arrêts non planifiés du process. Il est également possible de surveiller les consommations afin de pouvoir optimiser l’efficacité énergétique, de calculer la productivité effective d’une machine ou d’un équipement, de connaître leur taux de rendement synthétique (TRS), etc. Les possibilités sont aussi nombreuses et diverses que la variété des machines et des process de production mis en œuvre par les industriels.
Différentes utilisation des IIoT dans l'industrie
Optimisation des flux et applications
Suez a par exemple équipé les bennes de collecte de déchets déployées dans des déchetteries du territoire toulousain de modules de traitement électronique et de communication. Le module assure la collecte et l’envoi des données par transmission sans fil via la technologie Sigfox qui repose sur une infrastructure de communication radio de type LPWA (Low Power Wide Area). Mais il peut tout aussi bien communiquer dans le cadre d’autres projets par le biais des technologies sans fil LoRa ou LTE-M. Grâce à ces boîtiers électroniques connectés placés sur les bennes, Suez dispose d’une visibilité en temps réel sur le taux de remplissage des conteneurs, leur localisation à quai et hors quai, aussi bien au sein des déchetteries que durant leur transit. Les équipes opérationnelles connaissent ainsi précisément les phases de chargement/déchargement des bennes lorsque celles-ci se trouvent sur un camion ou au sol et sont alertées en cas d’immobilisation prolongée.
Nexans a quant à lui mis en œuvre un service IIoT qui permet aux opérateurs de réseaux de distribution de localiser leurs tourets de câble sur les chantiers et de connaître à distance la longueur résiduelle de câble sur ceux-ci afin que ses clients puissent piloter au plus près leurs stocks et l’avancée de leurs projets. Pour ce faire, le fabricant de câbles a équipé les tourets d’un boîtier instrumenté communicant sans fil qui transmet par voie radio les informations collectées à une plateforme Cloud dédiée à la surveillance et à l’analyse des données.
Surveillance des stocks
Des capteurs de niveau radar sont également conçus pour communiquer sans fil (via les technologies NB-IoT, LTE-M, LoRa ou 2G), se connecter au cloud et fonctionner sur batterie en toute autonomie. Ils permettent de surveiller en continu et à distance le contenu de réservoirs de produits liquides ou pulvérulents, 24h sur 24 et 7 jours sur 7, via un PC, une tablette ou un smartphone. L'exploitant peut ainsi maîtriser ses coûts, planifier ses stocks et prévenir toute pénurie. Il reçoit des alertes lorsque ses stocks atteignent des niveaux bas. Cette solution permet d’éliminer toutes les dépenses liées au déplacement du personnel affecté à la surveillance des cuves tout en fiabilisant et optimisant la gestion des stocks. En outre, lorsque les conteneurs sont déployés sur un site étendu ou sur plusieurs sites, la fonction de localisation GPS embarquée au capteur permet de connaître en temps réel l’emplacement de chaque cuve mobile de type IBC (Intermediate Bulk Container).
Maintenance prédictive
L'usine de FPT Industrial de Bourbon-Lancy en Saône-et-Loire produit des moteurs pour camions, bus, engins agricoles et de BTP, etc. Elle a mis en place une application de collecte et d’analyse en temps réel de certains paramètres de fonctionnement d’une de ses machines-outils. Ces paramètres fournis par la commande numérique remontent via une passerelle IIoT vers une plate-forme Cloud où elles sont analysées par des outils dédiés afin de déterminer l’état d’usure des vis à bille. Le service de maintenance est alerté en temps réel dès qu’une intervention est nécessaire sur la machine.
Sogema Services a développé la solution Sogebox pour aider ses clients à optimiser le suivi et la maintenance de leurs équipements électro-hydrauliques dotés de composants de Parker. Cette solution de maintenance prédictive surveille en temps réel la qualité de l'huile, l'état du filtre, la teneur en eau et la température des circuits hydrauliques. La Sogebox intègre des capacités de communication (4G LTE, Wi-Fi) et différents capteurs nécessaires à la surveillance et au diagnostic des machines (particules, pression, température). Elle transmet les informations à une plateforme Cloud dédiée qui les analyse et qui envoie des alertes par SMS ou e-mail si des dérives sont constatées. Une entreprise du secteur du machinisme agricole utilise cette solution pour surveiller en temps réel sa presse hydraulique. Cette solution l’alerte des élévations anormales de température. Ce qui évite ainsi de coûteux arrêts de production. Une autre entreprise utilisatrice exerçant dans le domaine la sidérurgie l’exploite quant à elle pour éviter des problèmes de pollution liquide sur un échangeur eau/huile. En la prévenant dès le début d’une pollution de sa centrale hydraulique, la Sogebox lui a permis d’éviter de coûteuses pertes d’huile neuve, à laquelle se seraient ajoutées les coûts liés au processus de dépollution des circuits depuis la dépose des composants à dépolluer jusqu’à leur repose.
Lapp a développé une solution de maintenance prédictive capable de prévoir avec précision quand la détérioration limite la fonctionnalité du câble Ethernet et donc d'anticiper sa défaillance. Ce système surveille en permanence les caractéristiques de transmission réelles des lignes de données pendant leur fonctionnement et mesure plusieurs paramètres pertinents. Les données sont évaluées dans le boîtier de surveillance prédictive qui est équipé de deux ports Ethernet et est simplement connecté au câble Ethernet à surveiller. Un algorithme spécifique calcule la durée de vie restante des lignes. Le système s'appuie sur les valeurs de millions d'ensembles de données qui ont été collectées et analysées dans le centre de test du fabricant de solution de câblage.
Les fondements technologiques de l'IIoT
L'Internet Industriel des Objets représente une évolution majeure dans la manière dont les industries collectent et utilisent leurs données. Imaginez chaque machine comme un capteur géant, transmettant en continu des informations précieuses sur son fonctionnement. Cette interconnexion permet de créer une véritable cartographie numérique de la production, où chaque équipement, du plus ancien au plus récent, contribue à l'intelligence collective de l'usine. Les données générées alimentent des systèmes sophistiqués qui transforment ces informations brutes en insights actionnables.
L'architecture des systèmes IIoT industriels
Au cœur de l'IIoT se trouve une infrastructure complexe mais intelligemment organisée. Les passerelles IIoT jouent le rôle d'interprètes universels, traduisant les différents langages industriels (Modbus, Profibus, EtherCAT) en un format standardisé compréhensible par les systèmes informatiques modernes. Cette harmonisation permet de créer un écosystème où les machines de différentes générations peuvent communiquer efficacement, transformant des ateliers disparates en un environnement de production unifié et intelligent.
La révolution de la maintenance prédictive
L'analyse continue des données de production permet désormais d'anticiper les défaillances avant qu'elles ne surviennent. En surveillant les paramètres critiques comme les vibrations, la température ou la consommation électrique, les systèmes IIoT peuvent détecter des schémas anormaux invisibles à l'œil humain. Cette approche proactive de la maintenance transforme radicalement la gestion des équipements industriels, réduisant les temps d'arrêt imprévus et optimisant les coûts d'exploitation.
L'optimisation des processus industriels en temps réel
Les technologies IIoT permettent une supervision fine et continue des processus de production. En collectant des données sur chaque aspect de la production - des temps de cycle aux consommations énergétiques - ces systèmes créent une base factuelle pour l'amélioration continue. Les algorithmes d'analyse peuvent identifier des opportunités d'optimisation souvent imperceptibles pour les opérateurs humains, conduisant à des gains significatifs en efficacité et en qualité.
Le Edge Computing au service de l'IIoT
La prolifération des données industrielles nécessite des solutions de traitement innovantes. Le Edge Computing répond à ce défi en permettant l'analyse des données au plus près de leur source. Imaginez un mini-centre de calcul directement installé sur votre ligne de production : il filtre, analyse et traite les informations en temps réel, ne transmettant vers le cloud que les données pertinentes. Cette approche décentralisée offre plusieurs avantages cruciaux : une réduction significative de la latence, une diminution des coûts de transmission de données, et une capacité de réaction quasi instantanée aux événements critiques.
L'intégration des technologies OT/IT
La convergence entre les technologies opérationnelles (OT) et informatiques (IT) représente un changement de paradigme dans l'industrie moderne. Traditionnellement séparées, ces deux sphères fusionnent grâce aux passerelles IIoT, créant un environnement unifié où les données circulent librement entre les machines et les systèmes de gestion. Cette intégration permet non seulement d'optimiser les processus existants mais aussi d'imaginer de nouveaux modèles opérationnels basés sur une vision holistique de l'entreprise industrielle.
La cybersécurité dans l'environnement IIoT
L'interconnexion croissante des systèmes industriels soulève des enjeux critiques de sécurité. La protection des données industrielles nécessite une approche multicouche, depuis la sécurisation physique des équipements jusqu'au chiffrement des communications. Les passerelles IIoT modernes intègrent des mécanismes de sécurité sophistiqués, permettant de créer des zones de confiance où les données sensibles peuvent circuler en toute sécurité, tout en restant accessibles aux applications autorisées.
L'avenir de l'industrie connectée
L'IIoT ouvre la voie à une transformation profonde de l'industrie. Les usines intelligentes de demain seront capables d'auto-optimisation, adaptant leur fonctionnement en temps réel aux conditions changeantes du marché et de la production. Les technologies émergentes comme l'intelligence artificielle et le machine learning, combinées aux capacités de l'IIoT, permettront de créer des systèmes de production véritablement autonomes, capables d'apprendre de leurs expériences et d'améliorer continuellement leurs performances. Cette évolution vers l'industrie 4.0 promet non seulement des gains d'efficacité significatifs mais aussi une réduction de l'empreinte environnementale de la production industrielle.
Produits associés
Stockage de données
Nous proposons une large gamme de produits de stockage de données et de mémoire.
Passerelles IoT
Nos dispositifs de passerelles IoT offre des solutions pour étendre un écosystème IoT ou mettre à niveau un environnement industriel.
IoT Industriel
Quel que soit votre projet, trouvez les produits et solutions pour bâtir l'industrie de demain.