- Publié le 27 nov. 2023
- Mis à jour le 14 mars 2025
- 14 min
Comment les agents de maintenance peuvent-ils résoudre les problématiques liées à l’instrumentation industrielle ?
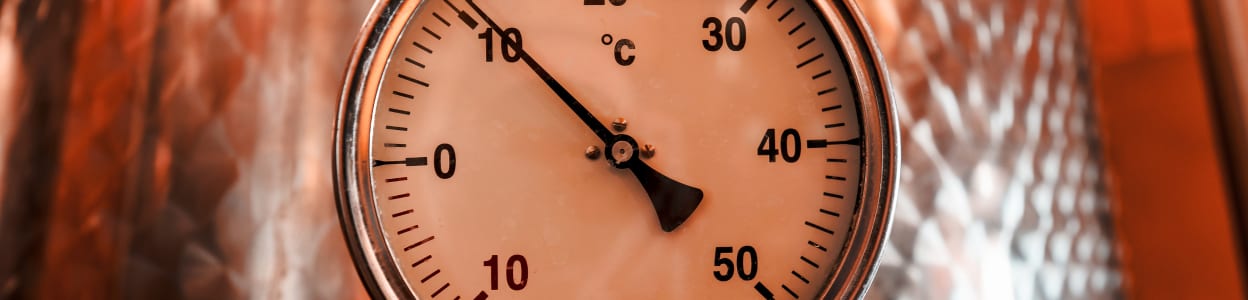
Lancé il y a déjà plus d’une dizaine d’années, le concept d’industrie 4.0 (anciennement nommée "Industrie du futur en France") s’est peu à peu imposé dans l’esprit des industriels à travers des projets de plus en plus concrets. En parallèle, la crise énergétique qui sévit depuis quelque temps les a poussé à recourir à davantage d’instrumentation. Une multitude de capteurs et d’instruments de mesure prennent place dans l’atelier mais charge au service maintenance de bien surveiller et de maintenir tous ces appareils, en fonction de règles d’étalonnage bien précises et de choix du bon protocole de communication.
L'instrumentation industrielle concerne l'utilisation d'instruments et de dispositifs de mesure servant à collecter, contrôler et surveiller des données dans des environnements industriels. Très répandus dans les industries chimiques, pharmaceutiques et agroalimentaires, ainsi que sur les sites utilisant de nombreuses sources d’énergies, l’instrumentation industrielle et les dispositifs de mesure qui l’accompagnent jouent un rôle crucial dans l'optimisation des processus de production, de maintenance et de gestion de l'énergie.
L’instrumentation fait appel à des technologies avancées et à des capteurs de pointe capables de collecter des données précises et en temps réel, d'analyser les performances des équipements et d’aider les agents de maintenance à prendre des décisions rapides en cas de problèmes intervenant sur le réseau ou le process. Au-delà des pannes et des dysfonctionnements de ligne, ces outils permettent d’améliorer l'efficacité globale de l’outil de production mais aussi, chose précieuse depuis le début de la crise énergétique, de réduire les coûts et minimiser l'empreinte environnementale.
Quels instruments sont concernés ?
Derrière le terme « instrumentation industrielle », on désigne le plus souvent non pas une famille de produits mais une diversité d’outils allant des capteurs aux transmetteurs, en passant par les sondes, les enregistreurs, les régulateurs, les vannes de contrôle et tout autre dispositif utilisé pour mesurer différents paramètres tels que la pression, la température, le débit, la concentration, le niveau, la vitesse, etc. Celle-ci regroupe ainsi un ensemble d'outils et de dispositifs utilisés pour mesurer, contrôler et réguler les variables physiques des procédés de production.
Gamme de produits :
Objectif de ces instruments ? Collecter les données physiques ou chimiques nécessaires afin de les transformer en signaux électriques ou électroniques pouvant être utilisés pour surveiller et contrôler les processus industriels, anticiper des pannes, prendre des décisions opérationnelles, optimiser les performances ou encore maintenir la sécurité et la fiabilité des installations industrielles… sans oublier le fait d’aider à réduire la facture énergétique en surveillant les écarts de température, de pression, de consommation électrique et l’apparition d’éventuelles fuites. Car en mesurant et en surveillant les grandeurs physiques telles que la consommation d'énergie, la température, le débit, la pression, les services maintenance peuvent identifier les sources de gaspillage, mettre en œuvre des mesures d'efficacité énergétique et réduire l’empreinte environnementale.
L'instrumentation industrielle mesure une variété de valeurs physiques en fonction des besoins spécifiques de l'application industrielle, des repères qui s’avèrent indispensables pour assurer le bon fonctionnement du process. Parmi elles figurent la pression (dans les systèmes de tuyauterie par exemple, les réservoirs, les chaudières, et autres récipients sous pression…), la température pour surveiller les niveaux de chaleur sur les machines mais aussi les systèmes de refroidissement avec la mesure de température des fluides notamment, ainsi que les moteurs et les compresseurs ; il en est de même pour l’analyse vibratoire et les ultrasons, deux technologies très complémentaires selon les besoins de précision visés.
Autre valeur concernée, le débit qui permet de mesurer la quantité de liquide, de gaz ou de matériau qui passe à travers des tuyaux ou des canalisations. La mesure de niveau est quant à elle utilisée afin de surveiller le niveau de remplissage des réservoirs, cuves ou de silos. Enfin, il est possible de mesurer la concentration (essentiellement dans la chimie et le traitement de l'eau) ou encore la conductivité (électricité), le pH ou encore la vitesse.
Des secteurs d’activité à la pointe de l’instrumentation industrielle
En utilisant ces instruments, les industries ont aussi la possibilité́ de surveiller et d’ajuster en temps réel les paramètres de production, de détecter les problèmes potentiels, de réduire les temps d'arrêt et d’optimiser les performances des équipements. Adaptés aux besoins de la maintenance préventive et prévisionnelle des équipements, ces outils font appel à des techniques de mesure telles que l'analyse vibratoire, l'analyse des fluides, la thermographie et la surveillance des gaz afin de fournir de précieuses informations sur l'état de santé de l’outil de production et ainsi réduire les coûts de maintenance, optimiser les performances et éviter les arrêts non planifiés.
À titre d’exemple, dans l’industrie chimique sont fréquemment utilisés des capteurs de débit et des régulateurs de pression permettant de minimiser les pertes d'énergie liées aux fuites dans les systèmes de distribution de fluide. La surveillance continue de la pression et de la température dans les procédés chimiques assurent la sécurité et l'efficacité de la production ; un critère essentiel (et obligatoire dans ce secteur d’activité), tout comme le fait de mesurer la concentration des solutions chimiques pour garantir la qualité du produit final ou encore la mesure de niveau des cuves de stockage.
régulateur de pression :
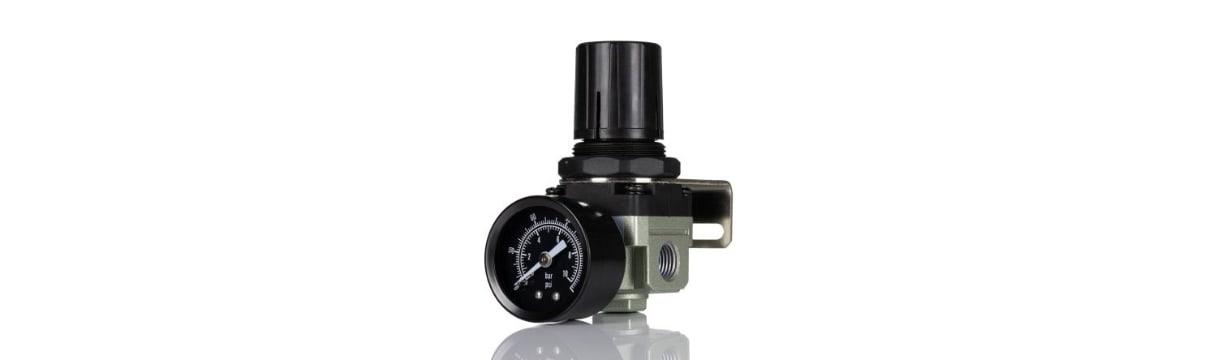
capteur de débit :
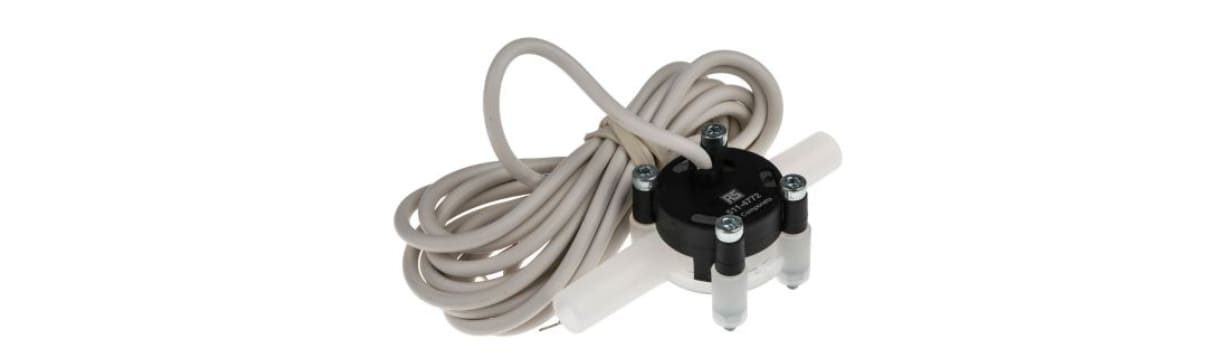
Dans l’industrie pharmaceutique, le contrôle de la température et de l'humidité dans les environnements de production et de stockage des médicaments est primordial, tout comme la surveillance en continu des paramètres de stérilisation (température, pression) dans les autoclaves ou encore la mesure de la concentration des principes actifs pour assurer la qualité et l'efficacité des médicaments, sans oublier la mesure précise du débit et de la pression lors de la fabrication de médicaments liquides ou gazeux.
Enfin, dans l’agroalimentaire, la mesure du débit et de la pression intervient au moment de la transformation des aliments, comme le lait ou la fabrication de jus. Le contrôle de la température dans les processus de cuisson et de pasteurisation y est essentiel ; c’est le cas aussi de la mesure de l'humidité dans les environnements de stockage des produits alimentaires. Enfin, mesurer des paramètres tels que le pH permet d’assurer le contrôle qualité des aliments avant leur conditionnement.
Résoudre les problématiques de maintenance et d’entretien des instruments de mesure
Bien que parfois bien équipés en matière d'instrumentation industrielle, les agents de maintenance n’en sont pas moins confrontés à plusieurs problèmes. Parmi eux, la défaillance des capteurs eux-mêmes : en environnement industriel, ceux-ci peuvent se dégrader avec le temps mais aussi à cause de conditions d’utilisation sévères (et peu adaptées en fonction du modèle choisi) ; or un capteur dégradé entraîne des mesures incorrectes et donc perdre en fiabilité des données.
Pour faire face à cette dégradation des capteurs et autres instruments de mesure, et ainsi assurer la précision attendue, il est essentiel de mener des opérations régulières de calibration et d’ajustement. Il en est de même pour l’étalonnage (à confier à des sociétés certifiées Cofrac). Il s’agit d’une tâche qui peut être confiée au service maintenance dans le cadre d’opérations de maintenance préventive. Dans le cas d’une démarche préventive ou curative (si une défaillance de l'instrumentation survient), les agents de maintenance doivent être en mesure de diagnostiquer rapidement la cause de la panne et de la réparer. Cela peut nécessiter des compétences techniques avancées et une compréhension approfondie des systèmes d'instrumentation.
Pour répondre efficacement à ces problèmes de dégradation, d’usure dans le temps ou au contraire prématurée, et assurer un bon étalonnage des instruments de mesure, les techniciens de maintenance n’ont d’autres choix que de se former suffisamment afin de bien comprendre leur fonctionnement… et, au préalable, bien choisir le matériel en fonction des attentes en matière de recueil de données et de l’environnement industriel. Ils doivent pour cela mener une veille technologique régulière, d’autant que l'instrumentation industrielle évolue rapidement.
Rappelons qu’en matière de calibrage et d’étalonnage, il est important d’une part d’établir un plan permettant d’identifier les instruments à calibrer, les fréquences de calibrage (recommandées par les fabricants ou les normes en vigueur) ainsi que les procédures spécifiques à suivre. Une documentation précise de toutes les opérations de calibrage et d'étalonnage doit absolument être tenue à jour comprenant les résultats, les dates de chaque opération et les noms des techniciens l’ayant effectuée.
Concernant le cas des capteurs, la calibration (avant et pendant usage afin d’éviter les dérives) implique de respecter quelques étapes clefs telles que la préparation (vérification de la propreté et du bon état du capteur), l’environnement dans lequel il va être utilisé, l’étalonnage régulier du capteur et son réglage en fonction de la courbe d’étalonnage, puis la vérification finale des instruments de mesure. Attention toutefois car une fois installé dans l’atelier de production, celui-ci peut subir des variations de température, d'humidité, de pression…, changements pouvant affecter les mesures du capteur.
Opter pour le bon protocole de communication
Parmi les autres problèmes rencontrés dans l’utilisation et la maintenance de l’instrumentation industrielle figurent les interférences électromagnétiques présentes sur certains sites, perturbations pouvant entraîner des mesures erronées. Mais avant même d’intégrer ses premiers capteurs dans son atelier de production, il est essentiel de bien vérifier l’interopérabilité et la compatibilité des instruments de mesure.
En effet, certains instruments de mesure peuvent avoir des interfaces différentes, compliquant ainsi leur intégration avec d'autres équipements ou systèmes de contrôle… et entraînant de fait des difficultés de communication et de transfert de données. En matière de protocole de communication, ceux-ci sont divers et variés ; lorsqu’ils ne ne sont pas compatibles, cela pose des problèmes pour établir une connexion et d'échanger des données entre le capteur de mesure et le système de contrôle.
Les protocoles en question sont multiples : Ethernet/IP (ou Ethernet industriel) est couramment utilisé pour sa communication stable et en temps réel entre les équipements (via un réseau câblé). De son côté, Profinet se distingue par sa vitesse d’exécution. Très répandu, le protocole Profibus permet quant à lui de connecter les appareils de terrain et un système de contrôle central ; il présente notamment l’avantage d’être plus simple du fait notamment du gain en matière de câblage, et se décline en différents profils (ProfiSafe, ProfiDrive, Profibus DP ou PA).
Autre protocole de plus en plus présent dans l’industrie, l’IO-link sert quant à lui d’interface de dialogue entre le capteur (ou l’actionneur) et l’automate. Reposant sur la norme CEI 61131, l’IO-link a spécialement été créé pour l’automatisation et se révèle particulièrement pertinent lorsque l’on souhaite recueillir un maximum d’informations permettant de mieux surveiller l’outil de production. Avec plusieurs valeurs mesurées au sein d’un seul instrument de mesure, il se révèle également simple à mettre en place, à utiliser et à maintenir en cas d’usure des capteurs.
Basé sur les protocoles de communication série RS-232/RS-485 et s'appuyant sur une architecture maître-esclave, Modbus est depuis longtemps utilisé pour la communication entre équipements industriels du fait de sa simplicité d’intégration ; il est cependant de moins en moins adapté aux besoins de puissance que l’on rencontre aujourd'hui. Aussi, l’AS-I (AS-Interface) se révèle simple à mettre en place et facilite le contrôle des capteurs. Autre exemple, le Highway Addressable Remote Transducer (HART) est requis pour la maintenance conditionnelle et prévisionnelle en raison de sa polyvalence et la possibilité qu’il offre de remonter des informations de diagnostic et de l’état de santé de l’outil de production. Enfin, le protocole Foundation Fieldbus se distingue lui aussi par sa simplicité d’utilisation grâce à moins de chemin de câbles et donc à la possibilité de connecter plusieurs appareils sur un seul câble.
Mais comment choisir le bon protocole ? En fonction de leurs natures (énumérées précédemment) certains sont en effet plus complexes à mettre en œuvre, d’autres plus coûteux, d’autres encore sur ou sous-dimensionnés par rapport sur aux volumes de données de mesure à traiter ou encore à la vitesse de communication souhaitée (dans le cas des très hauts débits) sans oublier la nécessité (ou non) de remonter toutes sortes d’informations supplémentaires pour la maintenance prévisionnelle. Il est avant tout important de bien prendre en compte la question de la compatibilité avec les systèmes existants. Il est d’ailleurs parfois nécessaire d'utiliser des convertisseurs d'interface, des adaptateurs de protocole ou des logiciels compatibles avec différents types d'instruments de mesure. De plus, une planification adéquate et une coordination entre les fournisseurs d'équipements peuvent aider à anticiper et à résoudre les problèmes liés à la compatibilité et à l'interopérabilité des instruments de mesure. Enfin, la distance de communication est un élément à considérer car si les instruments de mesure sont très éloignés du système de contrôle, il peut être pertinent de s’orienter vers un protocole adapté tel qu’Ethernet.
Dans tous les cas de figure , il est nécessaire de bien identifier ses besoins afin de s’orienter vers le capteur et le système de contrôle, puis le protocole le plus adapté, évaluer les coûts et la complexité d’installation puis les contraintes de maintenance – et former son personnel si besoin.