- Publié le 27 nov. 2023
- Mis à jour le 12 nov. 2024
- 22 min
L’étalonnage des instruments de mesure garantit la fiabilité et la cohérence des mesures
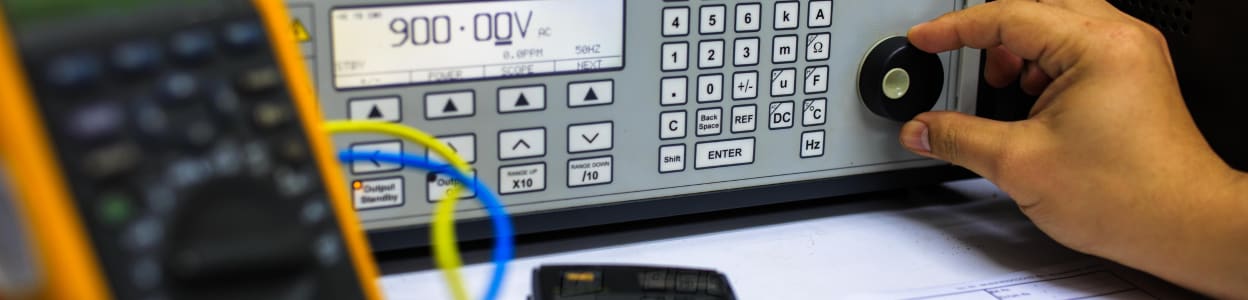
Les processus industriels et les machines exploitent des capteurs et divers instruments indispensables au contrôle de leur fonctionnement. Il peut s’agir de capteurs de courant, de température, de pression, de force, d’humidité, de débit, de vitesse, de vibrations… ou de compteurs énergétiques (électricité, gaz, vapeur, chaleur…). Les mesures délivrées par les instruments de mesure sont utilisées pour surveiller, contrôler ou optimiser le fonctionnement d’une machine ou d’un processus industriel. Elles sont indispensables à toutes entreprises afin de prendre les décisions pertinentes permettant de garantir la fiabilité d’un processus et la qualité de leurs produits ou services. Les mesures doivent donc être associées à une information permettant de juger de leur qualité et leur fiabilité. L’étalonnage permet justement de s’assurer que les instruments ou les capteurs fonctionnent correctement et fournissent une valeur de mesure avec le niveau de précision requis pour l’application concernée.
Qu'est-ce que l'étalonnage et pourquoi est-il important ?
L'étalonnage des instruments de mesure est un processus crucial qui consiste à comparer les indications d'un appareil de mesure avec celles d'un étalon de référence. Cette opération permet de déterminer la relation entre les valeurs mesurées par l'instrument et les valeurs connues de l'étalon, établissant ainsi la traçabilité métrologique. L'importance de l'étalonnage réside dans plusieurs aspects :
- Fiabilité des mesures : Il garantit que les résultats de mesure sont fiables et cohérents.
- Conformité aux normes : Il permet de respecter les exigences des normes comme ISO 9001 et ISO 17025.
- Optimisation des processus : Des mesures précises contribuent à l'amélioration de la qualité et de l'efficacité des processus industriels.
- Réduction des coûts : En prévenant les erreurs de mesure, l'étalonnage aide à réduire les coûts liés aux rebuts et aux reprises.
Fréquence d'étalonnage : à quelle périodicité étalonner vos instruments ?
La fréquence d'étalonnage des instruments de mesure dépend de plusieurs facteurs :
- Type d'instrument : Certains appareils nécessitent un étalonnage plus fréquent que d'autres.
- Conditions d'utilisation : L'environnement et l'intensité d'utilisation influencent la dérive des mesures.
- Exigences de précision : Plus la précision requise est élevée, plus l'étalonnage doit être fréquent.
- Recommandations du fabricant : Elles fournissent une base pour établir la périodicité initiale.
En général, un étalonnage annuel est recommandé pour la plupart des instruments. Cependant, cette fréquence peut varier de quelques mois à plusieurs années selon les critères mentionnés. Il est crucial d'établir un plan d'étalonnage adapté à chaque équipement de mesure pour maintenir la fiabilité des résultats.
Pourquoi étalonner les capteurs et instruments de mesure ?
Aucun capteur ou instrument de mesure n’est parfait. Les mesures délivrées ne sont jamais exactes. Elles sont toujours assorties d’une incertitude plus ou moins importante. Si le contrôle de certains processus industriels ou de certaines machines ne réclame pas des mesures d’une grande précision, d’autres sont plus exigeants. Certaines machines peuvent par exemple opérer correctement avec des capteurs offrant une incertitude de ± 10 %, tandis que d’autres exigeront une incertitude de +/-1 %. Dans le premier cas, cela signifie que si la valeur mesurée par le capteur est égale à X, la valeur réelle se situe plutôt sur une plage allant de (X moins 10 % de X) et (X plus 10% de X). C’est donc au constructeur de la machine et/ou son utilisateur de déterminer que ces erreurs de mesure ne dépassent pas des valeurs limites admissibles pour assurer un fonctionnement correct de la machine. Ces valeurs limites admissibles, appelées erreurs maximale tolérées (EMT), sont fixées par l’utilisateur comme étant la plus grande erreur qu’il est prêt à accepter.
L’étalonnage et/ou la vérification d’un instrument ou d’un capteur permettent d’estimer l’erreur de l’instrument et en cas de défaut de justesse, de la compenser en appliquant une correction. La vérification permet de confirmer que l’erreur de mesure reste inférieure à l’erreur maximale tolérée. Un étalonnage conduit à l’émission d’un certificat d’étalonnage, la vérification à un constat de vérification. Il ne donne pas lieu à une décision de conformité, seule la vérification permet un jugement ou une décision.
L’étalonnage consiste à relever les écarts entre les valeurs affichées par l’appareil à étalonner avec les valeurs réelles données par un étalon. Il s’agit d’une comparaison documentée entre un instrument de mesure à étalonner et un instrument de référence traçable. L’instrument de référence présente une précision plus élevée (ou une moindre incertitude de mesure) que l’instrument à étalonner. L’instrument de référence doit lui-même être étalonné de manière traçable. Ce qui signifie qu’il doit lui-même avoir été étalonné en utilisant un étalon de plus haut niveau. Ainsi, la traçabilité implique une chaîne continue d’étalonnages, de telle façon que l’étalonnage de plus haut niveau ait été réalisé dans un laboratoire national d’étalonnage ou un organisme équivalent.
Un capteur de température, une sonde à résistance de platine, une thermistance ou un thermocouple sont généralement étalonnés en les plaçant dans un environnement de température stable (four ou bain d’étalonnage) et en comparant les valeurs mesurées à celles d’un « thermomètre de référence ».
L'étalonnage des transducteurs de pression s’effectue en général à l’aide d’un générateur de pression, d'un transducteur de pression de référence et d'un logiciel d'étalonnage. Le générateur de pression fournit la pression nécessaire à l'étalonnage. Le transducteur de pression de référence, dont les caractéristiques de mesure sont connues avec précision, est utilisé comme point de comparaison pour étalonner le transducteur de pression testé. Le logiciel d'étalonnage traite les données délivrées lors du processus d'étalonnage et fournit un rapport d’étalonnage.
Selon la grandeur mesurée (tension, courant, masse, pression, température...), l’étalon de référence n’est pas toujours un instrument. Pour la mesure du poids, cela peut être une masse de référence. Pour étalonner le capteur à base de jauge de contraintes, on utilise un jeu de masses étalons dont les valeurs et les incertitudes sont parfaitement connues. Il existe plusieurs classes d'étalons de masse qui diffèrent par la largeur de leur intervalle de confiance. L’étalonnage d’un pied à coulisse est par exemple réalisé à l’aide de cales étalon raccordées. Pour estimer la répétabilité, on effectue une série de mesurages sur une cale étalon dans les mêmes conditions.
Quelles sont les possibles conséquences de l’utilisation d’une instrumentation non étalonnée ?
Respectant certains grands principes édictés par les exigences de la norme ISO 9001 de management de la qualité, de nombreuses entreprises se contentent d'une vérification régulière de leurs instruments alors qu'il est tout aussi important de se focaliser également sur le processus de mesure ainsi que d'autres paramètres affectant la mesure et pas uniquement sur les seules aptitudes de l'appareil.
Un étalonnage ne vise pas simplement à satisfaire l’exigence d’un auditeur. Il doit contribuer à garantir la fiabilité d’une mesure. Il doit être effectué au juste nécessaire et à sa juste utilité. Il faut donc se poser la question de l'usage exact de l'instrument ou du capteur dans les processus de fonctionnement d’une machine ou de production et mettre en place des outils de surveillance afin de ne pas attendre la phase d'étalonnage (en général) annuelle pour s'assurer que tout se déroule correctement.
Les valeurs mesurées servent à prendre des décisions appropriées. Il faut donc évaluer l'impact de la mesure sur la décision qui doit être prise. Comme les mesures ne sont pas justes, les décisions prises ne peuvent donc pas être certaines. Elles entraînent donc un risque avec des conséquences à différents niveaux et à divers degrés de gravité. Il existe un risque client (déclarer conforme une entité qui ne l'est pas ou encore ne pas régler un procédé qui devrait pourtant l'être) et un risque fournisseur (déclarer non conforme une entité qui est conforme en réalité ou encore régler à tord un procédé). Chaque application exige donc une évaluation des risques, et la détermination de l'impact des mesures selon les exigences attendues et les aléas inhérents. Cette évaluation peut être réalisée par des calculs statistiques appropriés, reposant sur des données provenant d'expériences passées et de processus déjà réalisés.
La fréquence à laquelle il faut étalonner un capteur dépend donc du type d’application concerné. Prenons l’exemple d’un capteur de température. Une machine peut intégrer un bain d’huile dont la température ne doit pas dépasser 100°C afin de garantir le bon fonctionnement du processus. Mais il est possible que le processus se déroule correctement jusqu’à une température maximale de 110°C. Dans ce cas, il suffira de s’assurer que le capteur fournit une mesure avec une incertitude inférieure à 10 %. L’industriel peut estimer qu’il doit vérifier ce capteur deux fois par an. Mais s’il s’avère qu’au fil des contrôles, le capteur dérive peu, il peut étendre l’intervalle de vérification. Dans un autre cas, si un capteur de température est employé pour la fabrication d’un produit dont la température doit strictement se situer entre 99°C et 101°C, le capteur doit effectuer des mesures avec une incertitude inférieure à 1 %. Il faudra donc régulièrement s’assurer que le capteur respecte cet impératif. Lorsque la précision de la mesure a un impact critique sur la qualité du produit final ou du bon déroulement du processus de production, le capteur devra être vérifié plus fréquemment.
Est-ce que l’étalonnage garantit la précision des mesures ?
En métrologie, on ne parle pas de mesure précise. Un instrument fournit toujours une valeur avec une incertitude de mesure qui a été évaluée via un processus d’étalonnage (ou l’anglicisme « calibration ») conformément à des procédures bien établies. Mais il est courant d’évoquer la précision d’un capteur où une mesure précise lorsque la valeur est fournie avec un très faible niveau d’incertitude. La précision est néanmoins une notion très relative. Certains processus vont exiger le contrôle d’un débit avec un incertitude de 10 %. Le capteur pourra donc être considéré comme suffisamment précis s’il fournit une valeur avec une incertitude inférieure à 10 % de la valeur mesurée. Dans d’autres situations, le capteur devra fournir une mesure avec une incertitude inférieure à 1 % pour que sa précision soit conforme aux exigences de l’application. L’étalonnage du capteur ou d’un instrument va donc permettre d’évaluer l’incertitude sur une plage de mesure donnée et de s’assurer qu’elle se situe au niveau exigé pour assurer le bon fonctionnement du processus ou d’une machine.
Il faut néanmoins veiller à bien faire la distinction entre la précision (le niveau d’incertitude) et la résolution d’un capteur. La précision d’un capteur peut être considérée comme l’aptitude d’un capteur à fournir une valeur mesurée avec la plus faible incertitude de mesure possible par rapport à la valeur réelle. Cette valeur est en générale définie par un pourcentage de la capacité maximale du capteur ou de l’instrument. Par exemple, pour un capteur dynamométrique dont la précision est de 0,1% de la pleine échelle de mesure et dont la plage de mesure s’étend à 100N, sa précision sera de 0,1% de 100N, soit 0,1 N.
La résolution correspond à la plus petite variation de mesure qu’un appareil peut différencier. Par exemple, un thermomètre classique avec une échelle graduée fournit en général une indication de la température au degré près. Il présente donc une résolution de 1°C. Un capteur de température offrant une résolution de 0,1°C par exemple délivre quant à lui des valeurs au dixième de degrés près. Il est nécessaire de prendre en compte ces deux paramètres (précision et résolution) pour sélectionner le capteur ou l’instrument le plus adapté à l’application à contrôler.
L’importance de la traçabilité métrologique
La traçabilité métrologique est un concept fondamental. Elle garantit la possibilité de comparer des résultats de mesure à l'échelle internationale. Elle est notamment exigée par des normes telles qu' ISO 9001, ISO 17025, etc. La traçabilité métrologique est la propriété d'un résultat de mesure selon laquelle ce résultat peut être relié à une référence par l'intermédiaire d'une chaîne ininterrompue et documentée d'étalonnages dont chacun contribue à l'incertitude de mesure. Un instrument doit être étalonné par rapport à une référence avec traçabilité au Système international d'unités (SI) pour garantir la qualité des données de mesure. Les instituts nationaux de métrologie créent des unités SI avec des incertitudes détaillées et analysées. Les unités sont ensuite transférées vers des étalons secondaires pour être utilisées durant les procédures d’étalonnage. La chaîne de traçabilité des instruments est établie en effectuant un étalonnage par rapport aux étalons secondaires. Cette méthode permet d'obtenir une chaîne d'étalonnage ininterrompue et documentée reliée à l'unité SI. Les valeurs de mesure de l'instrument fabriqué sont considérées comme traçables SI avec une incertitude connue. Plus il y a d'étapes d'étalonnage entre l'unité SI et l'instrument fabriqué, plus l'incertitude de mesure est élevée. Idéalement, la chaîne de traçabilité des étalonnages doit être aussi courte que possible pour les applications exigeantes.
Choisir le capteur adapté à chaque type de mesure
Il existe au moins autant de capteurs et d’instruments de mesure qu’il existe de paramètres mesurables qu’ils soient physiques, mécaniques, électriques, chimiques… Ainsi, il existe des capteurs de température, de force, de pression, d’accélération, de débit, de pH, de conductivité, de tension, de courant, de champ magnétique, de rotation, de vitesse… Impossible d’en faire une liste exhaustive. Et pour chaque paramètre à mesurer, il existe différents types de capteurs qui conviennent mieux à telles ou telles applications industrielles en fonction de la plage de mesure à couvrir, l’incertitude attendue, l’environnement et le mode d’utilisation… Les mesures de température peuvent être par exemple effectuées avec des sondes à résistance de platine, aussi appelées RTD (Resistance Temperature Detector), des thermistances CTN (Coefficient de Température Négatif), des thermocouples, des capteurs infrarouges… Un débit peut être mesuré par un débitmètre électromagnétique, une turbine à hélice, un débitmètre à ultrasons, un débitmètre à effet Coriolis… Les capteurs utilisés pour la mesure de niveau de remplissage d’une cuve ou d’un récipient peuvent quant à eux exploités divers principes de mesure : potentiométrique, hydrostatique, ultrasons, radar…
C’est le constructeur qui sélectionne le type de capteurs qu’il va intégrer dans sa machine en fonction des paramètres qu’il souhaite surveiller et du contexte d’utilisation de ces capteurs. Parfois, l’utilisateur peut intégrer des capteurs supplémentaires à une machine s’il estime que la mesure d’un ou plusieurs paramètres spécifiques lui permettent de mieux maîtriser son processus de production ou d’optimiser les interventions de maintenance à effectuer sur la machine.
Par exemple, le rabotage de planches et de lames de parquet exécuté à grande vitesse sur des machines automatisées peut conduire à des surchauffes qui, dans le pire des cas, peuvent enflammer les copeaux de bois et provoquer un incendie. Des caméras infrarouge peuvent donc être installées ultérieurement sur les machines. Outre la prévention d'incendie, la mesure sans contact de température par infrarouge contribue à l'amélioration de la qualité de fabrication en analysant en continue la température à la surface du bois. Elle permet de détecter immédiatement toute élévation de température excessive des pièces rabotées. Dans le cas présent, les capteurs sont embarqués et fixés à la machine. Mais on peut tout aussi bien imaginer des situations où la mesure serait effectuée ponctuellement et manuellement à l’aide d’un pyromètre portable. Il en est de même pour la mesure de puissance électrique. Certaines machines peuvent intégrer nativement des capteurs de tension et de courant qui permettent de mesurer la puissance consommée par la machine. Mais dans d’autres cas, si le process ne l’exige pas des mesures de puissances peuvent être réalisées par un opérateur avec un wattmètre portable seulement lorsque cela s’avère nécessaire.
Quelles sont les conséquences d'une mesure erronée ?
Une mesure erronée peut impacter de façon plus ou moins importante les processus et les activités de l’entreprise utilisatrice de l’instrument. Elle peut entraîner le dysfonctionnement ou l’arrêt d’une machine, des défauts sur les produits fabriqués et donc une augmentation des rebuts. Elle peut également conduire à une surconsommation de matière première et d'énergie, des pertes de temps et des surcoûts. A ces conséquences négatives peuvent s’ajouter des pertes financières dues aux mesures correctives qui doivent être prises suite à la réalisation de mesures erronées.
Par exemple, pour la fabrication d’un produit qui requiert le mélange de plusieurs ingrédients dans une proportion bien déterminée, il est impératif que les instruments de dosage fournissent une mesure dans la plage d’incertitude requise afin d’avoir l’assurance que le produit final respecte pleinement les spécifications attendues tant en terme de qualité que de quantité.
Les concepteurs d’une pièce mécanique spécifient ses dimensions assorties d’une tolérance car il est presque impossible de fabriquer une pièce en respectant parfaitement ses dimensions théoriques. Cette tolérance dimensionnelle correspond au degré d’imprécision acceptable. Les instruments de mesure dimensionnelle mis en œuvre pour le contrôle des pièces en production doivent donc fournir des mesures avec le niveau de précision requis. Si les mesures sont fournies avec une incertitude de mesure supérieure à la tolérance acceptée, une pièce pourra être considérée comme bonne lors d’un contrôle en production alors qu’elle ne l’est pas. Ce qui pourra empêcher ou compliquer son assemblage sur le produit final qui pourra lui-même connaître des dysfonctionnements.
Lorsqu’un système de comptage d’énergie est installé sur une machine ou une ligne de production pour en mesurer la consommation, une mesure erronée n’aura pas d’impact sur la qualité de fabrication du produit mais faussera le calcul des coûts énergétiques liés à la production de ce produit.
Les conséquences d’une mesure erronée dépendent complètement de l’application pour laquelle la mesure est effectuée.
Étalonnage et normalisation
- La norme ISO 9001 a été élaborée pour répondre à divers aspects de gestion de la qualité. Elle définit les critères applicables à un système de management de la qualité reposant sur un certain nombre de principes orientés notamment vers une forte orientation client, la motivation et l’engagement de la direction, l’approche processus et l’amélioration continue. Les mesures jouent souvent un rôle essentiel dans les processus d’une entreprise et impactent donc la qualité du produit final. Les instruments de mesure doivent donc être pris en compte dans les exigences des processus et dans l'approche de réflexion basée sur l'analyse des risques prévue par la norme ISO 9001. La norme ISO 9001 présente les exigences relatives aux instruments de mesure dans un chapitre intitulé « Ressources pour la surveillance et la mesure ». Elle décrit la sélection et la maintenance requises pour ces instruments. La traçabilité métrologique, grâce à des étalonnages réguliers, fait partie des exigences de la norme.
- La norme ISO/CEI 17025 établit les exigences générales de compétence pour effectuer des essais et/ou des étalonnages, y compris l'échantillonnage. Elle couvre les essais et les étalonnages effectués au moyen de méthodes normalisées, de méthodes non normalisées et de méthodes élaborées par les laboratoires. Cette norme permet aux laboratoires de démontrer leur compétence et leur capacité à produire des résultats valides, renforçant ainsi la confiance qui leur est accordée au niveau national et partout dans le monde. Elle contribue également à faciliter la coopération entre les laboratoires et d’autres organismes en assurant une meilleure acceptation des résultats dans différents pays. Les certificats et rapports d’essai peuvent être reconnus d’un pays à l’autre sans qu’il ne soit nécessaire de procéder à de nouveaux essais, facilitant ainsi le commerce international.
L’accréditation Cofrac (Comité français d'accréditation) d’un laboratoire de métrologie garantit que les équipements étalonnés délivrent des mesures qui sont fiables et traçables au Système international d'unités. Grâce aux accords multilatéraux, le certificat d’étalonnage émis est reconnu dans de très nombreux pays à travers le monde. Ce qui facilite les échanges commerciaux. Les laboratoires d’étalonnage peuvent être accrédités par le Cofrac pour l’étalonnage d’instruments dans un ou plusieurs domaines spécifiques : temps-fréquence, température, hygrométrie, dimensionnel, force et couple, masse et volume masse, électricité-magnétisme, pression, etc. Un certificat d’étalonnage avec constat de vérification accrédité Cofrac permet de garantir le raccordement des moyens de mesures utilisés lors de l’étalonnage au système international d’unité (SI) et que les résultats de mesures délivrés sont fiables dans l’intervalle d’incertitude de mesure déterminée.
Il existe par ailleurs des normes relatives à l’étalonnage de certains types de capteurs. En voici quelques exemples :
- La norme ISO 376 spécifie une méthode d'étalonnage des instruments de mesure de force utilisés pour la vérification statique des machines d'essais uniaxiaux (par exemple machines d'essai de traction/compression) et décrit une procédure de classification de ces instruments. Elle s'applique aux instruments de mesure de force dans lesquels la force est déterminée par la mesure de la déformation élastique d'un élément chargé ou d'une grandeur proportionnelle à celle-ci.
- La norme ISO 5347 comprend une série de documents traitant des méthodes pour l'étalonnage de capteurs de vibrations et de chocs. La norme ISO 5347-18 fournit des spécifications détaillées sur l'appareillage et le mode opératoire à utiliser pour l'essai de sensibilité de température transitoire. Elle s'applique aux capteurs piézo-électriques dans lesquels est mesuré le signal de sortie du capteur dû à un changement brusque de la température.
- La norme ISO 6789 fixe les exigences et spécifie les méthodes d'essai et le marquage des outils dynamométriques à commande manuelle utilisés pour le serrage contrôlé des assemblages boulonnés. Elle est applicable en particulier aux clés dynamométriques à lecture directe et aux clés dynamométriques à déclenchement.
Le certificat d'étalonnage : un document essentiel
Le certificat d'étalonnage est un document officiel qui atteste de la traçabilité et de la précision d'un instrument de mesure. Il contient des informations cruciales :
- Identification de l'instrument : Marque, modèle, numéro de série.
- Conditions d'étalonnage : Température, humidité, etc.
- Résultats de mesure : Valeurs mesurées et leurs incertitudes associées.
- Traçabilité : Référence aux étalons nationaux ou internationaux utilisés.
- Accréditation : Mention de l'accréditation du laboratoire (ex : COFRAC en France).
Un certificat d'étalonnage accrédité COFRAC, par exemple, offre une reconnaissance internationale, facilitant les échanges commerciaux et assurant la conformité aux normes de qualité les plus strictes.
Étalonnage et Vérification : quelle est la différence ?
Bien que souvent confondus, l'étalonnage et la vérification sont deux processus distincts :
Étalonnage | Vérification |
---|---|
Détermine la relation entre les valeurs mesurées et les valeurs de référence | Confirme si l'instrument respecte les spécifications |
Fournit des données quantitatives sur les erreurs de mesure | Donne un résultat binaire (conforme/non conforme) |
Permet d'ajuster l'instrument si nécessaire | N'inclut pas d'ajustement |
Résulte en un certificat d'étalonnage détaillé | Produit un constat de vérification |
La vérification utilise souvent les données d'étalonnage pour déterminer si l'instrument est conforme aux erreurs maximales tolérées (EMT) définies pour son utilisation spécifique. En conclusion, l'étalonnage des instruments de mesure est un pilier fondamental de la métrologie industrielle. Il assure la fiabilité des mesures, la conformité aux normes et contribue à l'amélioration continue des processus de production. En établissant une stratégie d'étalonnage adaptée et en comprenant l'importance des certificats d'étalonnage, les entreprises peuvent optimiser leurs opérations et maintenir un haut niveau de qualité dans leurs produits et services.