- Publié le 31 mai 2023
- Mis à jour le 11 oct. 2024
- 10 min
Comment bien préparer la maintenance des lignes de production pour la fermeture annuelle ?
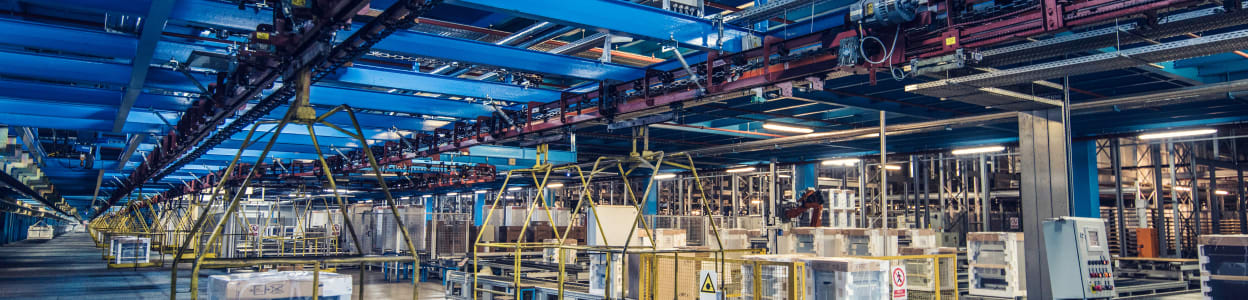
Plus que jamais d’actualité, les grands arrêts de maintenance représentent une étape cruciale pour de nombreuses entreprises industrielles. Face à la perte de compétences en maintenance mais aussi à la hausse des coûts et des délais de livraison des pièces de rechange, les fermetures annuelles de lignes de fabrication assurent à l’usine une meilleure disponibilité de l’outil de production dans un contexte de recherche de productivité accrue. Mais comment bien organiser ses grands arrêts ?
Étape indispensable pour un grand nombre d’entreprises industrielles, la fermeture annuelle des lignes de production – autrement appelée les grands arrêts de maintenance – est cruciale car elle permet d’assurer la disponibilité des équipements lors des phases de production. Planifiés à l'avance, ces arrêts ont une durée très précise, allant de quelques jours à plusieurs semaines. L’objectif est de planifier et d’organiser au mieux ces grands arrêts de maintenance, notamment pour réaliser des opérations de diagnostic, de réfection, de correction, d’ajustement et de réparation, voire de remplacement d’un équipement ou d’une machine.
C’est durant cette période en effet que les équipes travaillent sur la réparation, le remplacement et l’entretien de diverses pièces et de systèmes mécaniques, électriques, hydrauliques ou pneumatiques. Le service de maintenance effectue ainsi plusieurs activités, allant de la réparation au remplacement de pièces défectueuses, en passant par l'inspection de l'équipement, le nettoyage, la lubrification et les tests de performance. Ces activités visent à garantir que les équipements seront prêts à fonctionner en toute sécurité et à leur plein potentiel pendant l’année.
Objectif ? Avant tout, il s’agit de prévenir les temps d'arrêt imprévus susceptibles d’entraîner des pertes considérables pour l'entreprise. Ainsi, en garantissant la disponibilité de l’équipement durant la période d’exploitation et de production, les grands arrêts de maintenance réduisent indubitablement les coûts globaux tout en augmentant l'efficacité et la productivité de l'entreprise.
Mais ce n’est pas tout puisque ces interventions peuvent en outre contribuer à améliorer l'efficacité énergétique de l'entreprise, réduire les risques de sécurité et améliorer l'environnement de travail des salariés.
Comment déterminer les besoins en matière d’arrêt annuel et comment bien les planifier ?
La planification des arrêts de maintenance annuels nécessite une évaluation minutieuse de chaque équipement tout en prenant en compte les agendas, les délais et les budgets associés. Cette planification dépend à la fois de la taille, de la complexité et de la nature de l’atelier et du parc machines. Elle suppose d’une part d’identifier les équipements et les installations qui nécessitent une maintenance annuelle, d’autre part d’établir un calendrier définissant les périodes de l'année où ces arrêts peuvent être effectués. La production et le service maintenance devront donc se mettre d’accord pour déterminer les périodes de fermeture ou de ralentissement de l'activité les plus favorables pour planifier les arrêts de maintenance. Pour cela, il convient de prendre en compte l'historique de maintenance des équipements concernés, y compris les délais et la durée des opérations de maintenance précédentes.
Qui dit période dit délais ; une fois le calendrier établi, il est important d'évaluer le temps nécessaire pour la maintenance de chaque équipement, y compris le temps de préparation, d’intervention, de nettoyage et de remise en fonctionnement. Enfin, il est nécessaire de fixer un budget et de le faire valider par la direction, ce type d’intervention pouvant s’avérer coûteux – mais bien moins qu’une panne et l’arrêt de production qui s’en suit bien sûr.
Bien lister les opérations et les tâches à effectuer
Parmi les opérations d'entretien et de maintenance pouvant être réalisées pendant les grands arrêts de maintenance annuels figurent l’inspection et le nettoyage de tous les équipements mécaniques et électriques, des filtres ou des échangeurs de chaleur, des réservoirs de stockage et des tuyauteries, mais aussi le remplacement ou la réparation de toutes les pièces endommagées ou usées. Mais ce n’est pas tout, loin de là… La vérification et le calibrage des instruments de mesure et des capteurs font également partie des tâches à effectuer, tout comme les opérations de test de performance des moteurs, des générateurs, des transformateurs et des équipements de contrôle, l’inspection et la réparation des équipements de sécurité, à commencer par les systèmes d'extinction d'incendie et les alarmes. Enfin, viennent la vérification et la mise à jour des plans ainsi que des manuels d'exploitation et de maintenance.
Mais cette liste n’est pas exhaustive et dépendra des équipements et des procédés spécifiques de chaque installation. Il est important de soigneusement planifier les grands arrêts de maintenance annuels et de suivre les procédures de sécurité pour assurer la sécurité des travailleurs et la fiabilité de l'installation. Dans tous les cas, il est important de suivre une méthodologie efficace... En commençant – par exemple – par analyser les données de maintenance préventive et corrective des années passées afin de voir les tendances en matière de pannes et de défaillances. Il est également possible de planifier une inspection détaillée de chaque équipement en prenant en compte les recommandations du fabricant et les exigences réglementaires. Mais il ne faut pas non plus occulter les retours d’expérience exprimés par les techniciens, lesquels remontent parfois des problèmes récurrents au moment d’utiliser l'équipement.
Mettre en place son équipe dédiée ou travailler avec les entreprises extérieures
Une fois les besoins et les équipements identifiés les tâches listées, le planning, les délais et les coûts chiffrés vient le moment de créer son équipe. Pour ce faire, il convient de respecter quelques étapes. Tout d’abord, il est important d’identifier les compétences nécessaires. Pour cela, il faut avoir une idée de la composition de l'équipe, des compétences requises et des rôles de chacun. Puis se pose la question du recrutement ; si toutes les compétences sont déjà disponibles en interne, une stratégie doit alors être élaborée afin de s’assurer que l’équipe suit des consignes et des objectifs clairs, et que chacun des membres est bien au fait des procédures de travail et de sécurité à suivre. Il est crucial de former l'équipe – et de prévoir le cas échéant des sessions de formation pour les membres de l'équipe pour renforcer leurs compétences et leur expertise.
Pour mener à bien les grands arrêts annuels, il est important de considérer la complexité de l'équipement ou de la machine, ainsi que les compétences et l'expérience de l'équipe de maintenance qui effectuera les travaux. C’est tout particulièrement le cas des entreprises sous-traitantes, pour lesquelles il est indispensable d’avoir des objectifs clairs. C’est pourquoi il est important d’établir un cahier des charges précis, définissant clairement les tâches à effectuer, les résultats attendus et dans quels délais.
Il convient naturellement de sélectionner des prestataires qualifiés, compétents et expérimentés dans le domaine de la maintenance industrielle, de fixer les dates des interventions à l’avance en fonction des disponibilités de tous, et surtout, communiquer à travers des briefings toutes les informations nécessaires aux intervenants, notamment les règles de sécurité, les procédures à suivre et les accès autorisés, sans oublier les historiques d’intervention des équipements concernés. Il est enfin recommandé de mener un suivi régulier de l’avancement des travaux pour éviter les mauvaises surprises et assurer un suivi de la prestation à travers un bilan afin d’évaluer la qualité du travail réalisé en vue d’améliorer les interventions à venir.
Assurer l’approvisionnement et la disponibilité des pièces de rechange
L'assurance de la disponibilité des pièces de rechange est une condition* sine qua non *d’une maintenance efficace. Pour assurer la disponibilité de celles-ci, il est important d'établir une liste des pièces de rechange nécessaires à chaque équipement et chaque installation. Il est également pertinent de tenir compte de la durée de vie de chaque pièce, de la fréquence des remplacements et des délais de livraison. Autre priorité, le stockage des pièces de rechange.
Disposer d'un stock de pièces de rechange pour les équipements et les machines est primordial ; les pièces doivent être stockées dans des endroits appropriés, de manière à ne pas subir de dommages ou de détérioration. Outre le fait de travailler avec des fournisseurs de pièces de rechange fiables, capables de livrer rapidement les pièces nécessaires (et bien sûr de qualité), il est fortement conseillé de s’appuyer sur un système de gestion de stock efficace pour suivre la disponibilité des pièces de rechange, les niveaux de stock et les délais de livraison. Une bonne gestion des stocks, doté d’une identification précise des pièces, évite des pertes de temps bien inutiles, en particulier lors de ces opérations de maintenance encore trop souvent perçues comme trop coûteuses par la direction de l’entreprise.
De quelles technologies s’équiper pour assurer la maintenance lors des arrêts annuels ?
De multiples technologies se révèlent une aide précieuse pour les équipes de maintenance, à commencer les outils logiciels de gestion de maintenance assistée par ordinateur (GMAO), bien connus de la profession, en particulier pour planifier (mais aussi historiser) toutes les interventions, répartir les tâches et valider et boucler les ordres de maintenance.
Autres technologies en vogue, les objets connectés – ou « IOT » (Internet des objets). Ceux-ci permettent notamment, à travers des capteurs intelligents, de détecter des anomalies en amont d’une éventuelle panne… et ainsi orienter le responsable maintenance dans sa décision de programmer ou non un arrêt annuel sur tel ou tel équipement. En somme, tout ce qui couvre le domaine de la maintenance prévisionnelle (ou « prédictive maintenance » en anglais) peut contribuer à la préparation et à la réalisation des arrêts annuels de maintenance. Notons également qu’un système de Manufacturing Execution System (MES), en permettant de suivre en temps réel la production et l’état de santé des machines, fait remonter de nombreuses données précieuses pour élaborer une stratégie d’arrêts de maintenance.
Moins poussée que la prédictive maintenance, la maintenance conditionnelle elle aussi a son rôle à jouer ; celle-ci intervient en amont de ces arrêts en permettant ainsi de savoir sur quels équipements s’intéresser en mesurant et en analysant de nombreux paramètres physiques décrivant l’état de santé des équipements… et ainsi mieux orienter ses arrêts annuels pour gagner en efficacité et réduire des temps d’arrêts toujours très onéreux pour les entreprises.
Services associés
IoT Industriel
Quel que soit votre projet, trouvez les produits et solutions pour bâtir l'industrie de demain.
RS Smart Inventory Management
Une solution intelligente pour la gestion et l'optimisation de vos stocks.