- Publié le 9 janv. 2023
- Mis à jour le 29 août 2023
- 5 min
Comment repérer et localiser les pannes dans une ligne de production
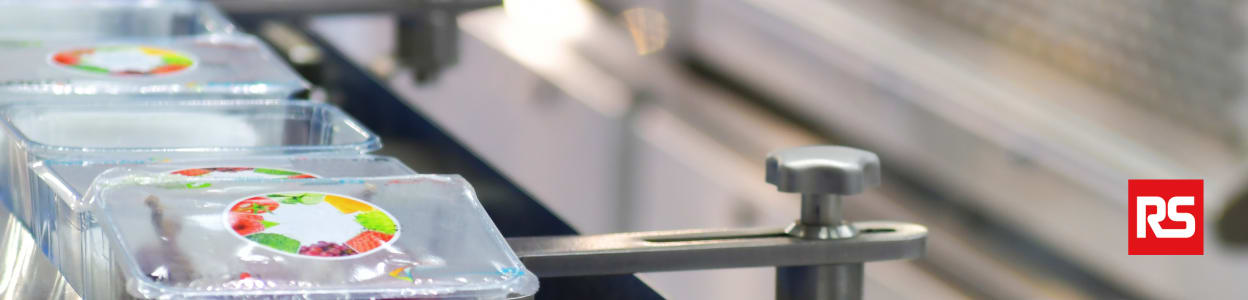
Article publié le 20/08/2021
Personne n'aime les pannes. Mais il y a une différence entre une ampoule à remplacer à votre domicile et une ligne de production qui suffoque en raison d'une défaillance technique au sein d'un équipement industriel. La question des pannes est en fait extrêmement importante pour les professionnels de la maintenance, car elles peuvent coûter beaucoup d'argent, mobiliser de nombreuses personnes et considérablement désorganiser votre site industriel. Pour limiter les risques, il est donc essentiel de savoir comment repérer, localiser les pannes et surtout faire en sorte qu'elles ne se reproduisent pas.
Revenir aux fondamentaux pour prendre du recul
Aucune usine n'est parfaite et il y a toujours des points à améliorer et des problèmes à résoudre. Cependant, il arrive que les entreprises soient confrontées à des problèmes multiples et qu'il leur soit difficile d'en trouver les sources afin d'y apporter une solution. C'est notamment le cas des pannes qui peuvent être causées par une multitude de facteurs : une intervention humaine, un problème électrique, une défaillance technique, un problème identifié (mais dont la maintenance a été maintes fois repoussée), une négligence d'un salarié ou d'un technicien, etc.
Afin d'optimiser votre travail d'intervention, il existe deux outils classiques qui vous permettront de mieux repérer et localiser les pannes afin d'établir un premier diagnostic.
La cartographie de vos processus
Les processus dans l'industrie peuvent être complexes et difficiles à visualiser, ce qui peut causer des difficultés dans la résolution de problèmes ou causer la réalisation d'un travail inutile. C'est pourquoi la cartographie des processus est un outil très utile. Cet outil consiste en une description visuelle de toutes les activités d'un processus dans l'ordre où elles sont effectuées. Après avoir complété ce travail, il sera plus facile d'identifier à quelle étape une amélioration peut être apportée et quels sont les impacts en cas de panne, afin d'éviter un effet domino sur votre ligne de production.
Le diagramme de causes et effets
Également connu sous le nom de diagramme d'Ishikawa, c'est un outil utile pour vous aider à organiser vos idées relatives aux causes possibles du problème. À partir du problème principal, toutes les causes possibles sont réparties en cinq catégories communément appelées les 5 M.
- Matière : les matières et matériaux utilisés.
- Matériel : l'équipement, les machines, le matériel informatique, les logiciels et les technologies.
- Méthode : le mode opératoire, la logique du processus et la recherche et développement.
- Main-d'œuvre : les interventions humaines.
- Milieu : l'environnement et le contexte.
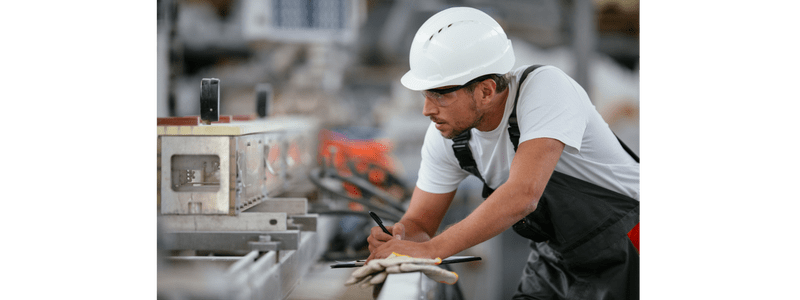
Quelle solution mettre en place pour réduire le risque de panne ?
La solution tient en deux mots : la maintenance industrielle. En effet, c'est elle qui contribue à réduire le risque de panne, mais surtout, dans le cas de la maintenance prédictive, d'éviter qu'elles ne se produisent. Schématiquement, il existe 4 grands types de maintenance pour vos équipements industriels :
- la maintenance corrective qui vise à intervenir en cas de panne pour limiter les impacts et trouver des solutions rapides,
- la maintenance curative qui vise à réparer en profondeur ou à remplacer un équipement ou un système,
- la maintenance préventive qui consiste à faire une inspection régulière de l'équipement,
- la maintenance prédictive qui se base sur l'intelligence artificielle pour anticiper les risques de pannes et intervenir avant même que celles-ci ne se produisent.
En cas de panne, votre équipe de maintenance doit agir vite, car l'arrêt de la production peut avoir des conséquences importantes. Vous avez donc 5 actions possibles à effectuer par ordre de priorité.
- Tenter de faire fonctionner votre équipement industriel en mode dégradé si c'est possible. Cela signifie qu'il ne sera pas aussi opérationnel ou productif que prévu et qu'il fonctionne au minimum de ses capacités.
- Effectuer une réparation d’urgence par un technicien de votre équipe de maintenance corrective.
- Basculer sur une production manuelle et demander à vos salariés de faire ce que faisait la machine. Parfois, c'est possible (empaqueter et organiser des colis par exemple), parfois, c'est trop complexe et technique.
- Faire une opération de maintenance curative pour réparer durablement l'équipement ou la ligne de production en question.
- Trouver des solutions pour éviter les arrêts futurs, en misant notamment sur la maintenance prédictive.
La maintenance prédictive utilise la puissance des données collectées par des capteurs et analysées sur un outil de GMAO (Gestion de Maintenance Assistée par Ordinateur) pour intervenir au bon moment. C'est une stratégie qui repose sur une bonne utilisation des données via un système d'intelligence artificielle capable « d'apprendre » et de s'adapter selon le fonctionnement de l'équipement. Votre ligne de production est ainsi analysée en temps réel par des capteurs et la maintenance est mise en œuvre sur la base des signes indiquant une dégradation du fonctionnement d’un système. Il est ainsi possible de prévoir les interventions avant la défaillance et de limiter les interventions non planifiées.
Mettre en place une stratégie pour repérer et localiser les pannes dans une ligne de production est indispensable afin de travailler plus efficacement. On parle alors de maintenance 4.0 pour réaliser la bonne intervention, au bon moment et avec les bonnes personnes. De quoi avoir une approche plus rationnelle et stratégique en matière de maintenance industrielle et faire des pannes (presque) un sujet du passé.
Services associés
Passerelle IoT
La passerelle compatible avec la technologie MobiusFlow ® de RS Pro transforme vos données en avantage commercial.
Capteur intelligent
Les capteurs intelligents sont conçus avec des comportements particuliers pour s'adapter aux applications spécialisées.
IoT Industriel
Quel que soit votre projet, trouvez les produits et solutions pour bâtir l'industrie de demain.