- Publié le 2 janv. 2025
- Mis à jour le 2 janv. 2025
- 8 min
La GMAO comme brique incontournable de l’industrie 4.0
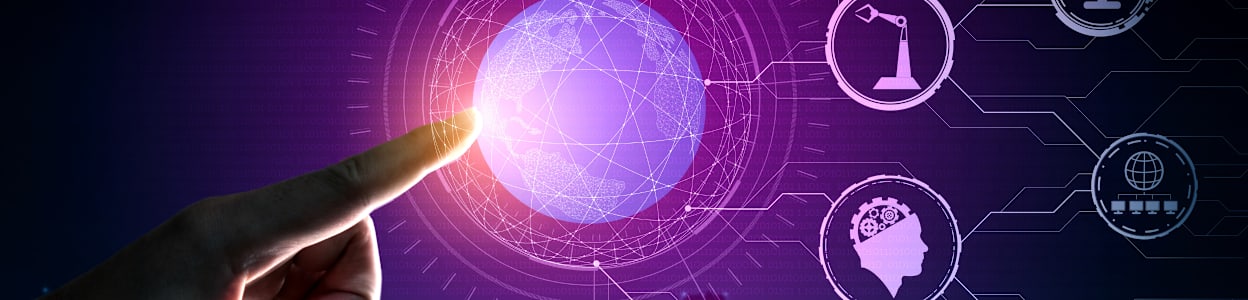
Depuis les années 80, la gestion de la maintenance assistée par ordinateur (GMAO) a permis à de nombreuses entreprises d’optimiser leurs interventions et leurs opérations de maintenance. Les logiciels sur le marché n’ont pas manqué de prendre le virage du 4.0. En intégrant des outils de mobilité, la GMAO permet de remonter des données dans le Cloud, d’interagir avec les autres outils du système informatique de l’entreprise et même utiliser l’IA pour affiner la stratégie de maintenance.
Dans un contexte de numérisation progressive de l’industrie et des usines, chaque étape de la production est concernée. Outre le fait de s’affranchir du papier et de ses inconvénients (espace disponible, conservation dans le temps, perte de document, risques d’erreurs de saisie…), les entreprises industrielles profitent de nombreux avantages : rapidité de la programmation des machines et des temps d’exécution du process (avec l’automatisation et la robotisation de la production), monitoring des équipements et suivi précis des étapes de fabrication, remontée des précieuses données de production ou encore gestion automatisée des stocks et du conditionnement… Mais la maintenance aussi est, elle aussi, concernée par la numérisation des opérations
De l’optimisation des opérations à la planification proactive des interventions
S’intégrant pleinement dans cette étape de digitalisation de l’usine, la GMAO est désormais considérée comme un élément incontournable de l'industrie 4.0, et ce pour plusieurs raisons. Tout d’abord, la GMAO, en intégrant des outils numériques, permet de passer d'une approche réactive à une approche proactive en matière de maintenance. Les responsables maintenance peuvent ainsi établir des plans de préventif reposant à la fois sur les recommandations des fabricants d'équipements et sur des analyses historiques.
Cela permet d'anticiper les besoins en maintenance avant qu'un problème ne survienne, réduisant ainsi les temps d'arrêt non planifiés. En ce sens, la GMAO participe à l’idée d’une maîtrise de plus en plus fine des tâches effectuées dans l’usine et les nombreux indicateurs de performance (KPI) tels que le temps moyen entre pannes (MTBF) ou le temps moyen de réparation (MTTR). Ces indicateurs fournissent des données essentielles pour optimiser les processus. Cela aide également à identifier les équipes ou les équipements nécessitant une attention particulière (équipements dits « critiques »).
Si l’on va plus loin dans ce contrôle de la production et de l’état de santé des équipements, le suivi en temps réel figure comme l’objectif ultime à atteindre. Et si le rôle d’une GMAO n’est pas de remonter des informations temps réel captées sur les machines, celle-ci s’interface sans problème avec l’ERP de l’entreprise, lui-même connecté à des outils de MES (Manufacturing Execution System) ; l’intérêt est de renseigner la GMAO de signes de défaillances repérés par le MES et d’affiner sa stratégie de maintenance. Ces données permettent aussi d’enrichir considérablement les plans de préventifs mais aussi, in fine, de se diriger vers de la maintenance prévisionnelle (« predictive » en anglais), prenant en compte de futures opérations à mener sur un équipement critique et l’intégrer dans le planning d’intervention, ou encore pour anticiper la commande et l’approvisionnement de pièces de rechange.
La GMAO se révèle aussi être un outil capable de s’ouvrir à la production. En effet, grâce aux alertes générées par les capteurs en cas d’échauffement anormal sur une machine ou d’une vibration suspecte, le technicien de production peut avertir directement la maintenance afin qu’elle intervienne directement voire pour lui indiquer, dans la mesure du possible, quelle action mener s’il s’agit d’un simple réglage à effectuer par exemple.
La collecte et l’analyse de données pour une analyse approfondie
Dans le cadre de l'Industrie 4.0, la collecte et l'analyse de données sont essentielles et la GMAO se se présente comme un réel atout pour l’entreprise. Celle-ci recueille de précieuses données sur les performances des équipements et les historiques de maintenance, permettant une analyse plus approfondie afin d’anticiper les pannes et améliorer les processus. Cette centralisation des informations inclut les historiques de réparation, le suivi des pièces de rechange, et les données de performance. En outre, elle facilite l'accès à l'information pour tous les acteurs impliqués, ce qui améliore l'efficacité des décisions prises.
Il est possible l’aller encore plus loin dans le traitement de la donnée en y intégrant de l’analyse prévisionnelle (souvent qualifiée de « prédictive »). Mais attention ! Là encore, ce n’est pas le rôle d’une GMAO de générer de la donnée afin d’en faire de la maintenance prévisionnelle. En revanche, il est aujourd'hui possible d’associer différents outils prédictifs à la GMAO et ainsi, à partir d’une analyse fine, prendre les bonnes décisions en matière d’intervention préventive avant que les éventuelles pannes ou défaillances n’apparaissent. Cela réduit non seulement le temps d'arrêt, mais permet également une planification plus précise et un meilleur contrôle des coûts liés à la maintenance.
L’intégration avec des systèmes d’analyse avancée, comme les outils de Business Intelligence (BI), permet d’exploiter les données générées par la GMAO. Cela favorise l’analyse prévisionnelle en utilisant des modèles statistiques et des algorithmes afin de mieux anticiper les pannes. L’entreprise peut dès lors prendre des décisions basées sur des données concrètes plutôt que sur des expériences passées.
Le rôle clé de l’IoT
La GMAO peut être connectée à des capteurs IoT dont le rôle est de surveiller en temps réel l'état des machines. Cela permet une maintenance prévisionnelle afin de pouvoir intervenir peuvent être effectuées avant que des défaillances ne surviennent, augmentant ainsi l'efficacité globale de la production. En effet, intégrer la GMAO aux technologies IT de l’entreprise s’avère indispensable pour tirer le meilleur parti des données générées et optimiser les opérations de maintenance. La mise en œuvre de la maintenance prévisionnelle, rendue possible grâce à cette intégration, offre des avantages considérables, permettant aux entreprises de réduire les coûts, d’augmenter la disponibilité des équipements et d’améliorer la sécurité tout en soutenant un processus d'amélioration continue.
Les données recueillies par ces capteurs peuvent être envoyées directement à la GMAO, ce qui permet d’automatiser la détection des anomalies et de déclencher des alertes pour une maintenance prévisionnelle. Ces nombreuses données peuvent être obtenues à l’aide de capteurs de vibration, de pression ou de température, des points de contrôle de lubrification, des systèmes de mesure du bruit. L’intérêt réside surtout par le fait que ces outils permettent de mesurer grâce à des automates programmables industriels, le bon état de de la machine ou de l’équipement alors en état de fonctionnement.
Des atouts multiples propres à l’industrie 4.0
Les nombreux progrès effectués par les éditeurs sur les logiciels ont permis de pleinement intégrer la GMAO dans l’usine numérique et en tirer un grand nombre de bénéfices. C’est le cas par exemple de la communication et de la collaboration entre les équipes, en particulier entre la maintenance et la production. En connectant la GMAO aux plateformes numériques, l'information se partage plus facilement ; ce qui aide à coordonner les efforts et à résoudre plus rapidement les problèmes.
Aussi, en optimisant les processus de maintenance et en prévenant mieux les pannes, la GMAO contribue à la réduction des coûts d'exploitation. Elle permet également d'allonger la durée de vie des équipements et ainsi générer un avantage financier significatif pour l’entreprise. Ce pas tout. Sur le volet du développement durable, la GMAO permet de réduire les déchets liés aux processus inefficaces et en optimisant l'utilisation des ressources.
Enfin, notons qu’en identifiant de potentiels problèmes, la maintenance prévisionnelle contribue à réduire le risque d’accidents liés à des équipements défectueux, améliorant ainsi la sécurité au travail. Intégrer l’humain dans l’industrie revient aujourd'hui à parler de « 5.0 »… là encore, la GMAO a son rôle à jouer.