- Publié le 12 mai 2023
- Mis à jour le 18 oct. 2024
- 12 min
Qu'entendons-nous par une bonne lubrification industrielle ?
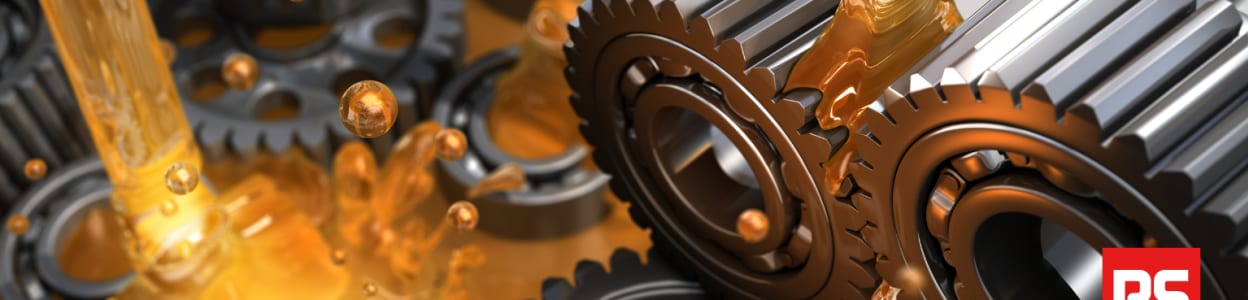
Il n’y a pas de disponibilité, de fiabilité et de durabilité satisfaisantes de la grande majorité des machines tournantes industrielles sans une bonne lubrification. La bonne lubrification s’entend par la distribution du bon lubrifiant, en bonne quantité, au bon moment, au bon endroit et avec la bonne méthode. Elle permet, en général à moindre frais, de réduire les coûts d’achats et de maintenance et d’augmenter la production et la productivité. Ce qui suit permet de mieux comprendre l’impact d’une bonne lubrification et dévoile des pistes pratiques pour sa mise en œuvre.
Si les processus de fabrication sont d’ordinaire bien définis et suivis avec le plus grand soin et des moyens de plus en plus automatisés, la lubrification des équipements industriels manque très souvent d’attention, voire est tout simplement négligée. Si vous en doutez, posez-vous ces simples questions :
- Quels processus sont mis en place pour la bonne lubrification de ces équipements ?
- Comment leur bonne exécution est-elle contrôlée et traçable ?
- Quels indicateurs de performance existe-il, en plus de la consommation de lubrifiants, au niveau de la lubrification ?
- A quelle fréquence les personnes en charge de la lubrification sont-elles formées sur ce sujet ?
Une des raisons principales de ce manque d’attention est que des achats de lubrifiants représente en général seulement 1 à 3% du budget de maintenance. Un manque d’intérêt pour cette petite part n’aurait que peu d’incidence si une lubrification non-maitrisée n’influençait pas significativement, en plus de la sécurité et de la disponibilité des machines, les autres parties de ce budget : les coûts de pièces détachés et équipements, les coûts de mains d’œuvre et les coûts d’interventions en urgence. Et il est couramment reconnu que la lubrification peut affecter jusqu’à 40% d’un budget de maintenance. Autre constatation : 36% des avaries prématurées de roulements sont directement dues à la lubrification. Si à cette part nous ajoutons celle causées par la contamination, qui est le plus souvent étroitement liée à la lubrification, nous pouvons donc affirmer qu’environ la moitié des casses anormales de roulements ont pour origine une lubrification non-maitrisée.
D’autres raisons pourraient être énoncées. Ces deux éléments suffisent, semble-t-il, à montrer qu’une attention plus prononcée que d’ordinaire pour la lubrification est le plus souvent bénéfique.
Alors comment faire pour prendre soin de la lubrification de ses machines ? S’il est aisément compréhensible qu’il soit nécessaire de s’assurer que l’on a le bon lubrifiant, en bonne quantité, au bon moment, au bon endroit et avec la bonne méthode, et que la conjonction de ces cinq facteurs est primordiale (on ne parle pas du choix de l’un d’entre eux, ni même de plusieurs d’entre eux ; les cinq sont indispensables à une bonne maîtrise), encore faut-il savoir comment y parvenir. La suite de ce texte vous donne quelques pistes en ce sens.
Le bon lubrifiant
Le bon lubrifiant est un lubrifiant de qualité, cela tombe sous le sens. Pour évaluer la qualité d’un lubrifiant, plutôt que s’attacher aux descriptions plus ou moins objectives des documents promotionnels, il est plus efficace d’examiner les résultats des tests, souvent normalisés, qui sont publiés ou disponible auprès de leurs fournisseurs, de les comprendre et de comparer ce qui peut l’être (la liste des tests n’est pas normalisée, elle est laissée à l’appréciation des fournisseurs). Mais c’est aussi un lubrifiant adapté à l’équipement qu’il lubrifie : tout comme de l’huile moteur ne convient pas à une cuisine saine et savoureuse, tout lubrifiant ne convient pas à toute machine. Tout lubrifiant industriel mérite d’être sélectionné en fonction des conditions et des contraintes de fonctionnement. Une méthode couramment utilisée pour cela est de suivre les recommandations des fabricants des machines. Cette méthode est souvent conseillée pendant les périodes de garantie des machines, mais possèdent les inconvénients suivants :
- Les constructeurs de machines ne connaissent pas nécessairement les conditions dans lesquelles vont fonctionner leurs machines. Et ces conditions peuvent changer dans le temps
- Pour ces raisons et par souci de sécurité, les constructeurs, peuvent sélectionner des lubrifiants trop élaborés par rapports aux conditions réelles d’utilisation et en faire payer le prix aux utilisateurs des machines.
- Si on suit les recommandations de tous les fournisseurs de machines et équipements, on se retrouve avec une quantité importante de fournisseurs et encore plus importante de lubrifiants. Ceci augmente les coûts d’achats, de stockage et de gestion et rend très complexe, voire extrêmement complexe (pour ne pas dire impossible), la gestion de la lubrification au quotidien. Il en résulte une flambée des coûts et de nombreuses erreurs d’exécution.
Une méthode plus pragmatique est une sélection d’un panel de lubrifiants correspondant aux conditions réelles de fonctionnement (et non supposées), assorties d’une rationalisation de ce panel pour limiter le nombre de variantes. Ce travail peut être réalisé avec l’aide de logiciels de sélection et / ou d’une bonne connaissance des lubrifiants. Des spécialistes de la lubrification peuvent grandement aider à cette sélection. Le résultat de ce travail est une gamme de lubrifiants gérable, économiquement acceptable et source d’économies et une lubrification des machines techniquement adaptée.
Le bon moment
Les lubrifiants sont comme nous tous : ils vieillissent. Plus exactement, leur état se modifie (c’est-à-dire se détériore) sous l’effet conjugué des attaques chimiques, mécanique et des mélanges avec des éléments étrangers. Il peut en résulter des changements de consistance, des pertes d’huiles, des fuites un manque d’additifs et donc des transformations fondamentales des qualités du lubrifiant, qui finit par être incapable de remplir correctement son rôle. C’est pour cela que le lubrifiant est périodiquement remis à niveau ou remplacé par du lubrifiant neuf (appoints d’huile ou de graisse, vidanges, etc.). La question est : quelle est la fréquence idéale pour ces appoints ou ces vidanges ? La fréquence idéale est celle qui garantit un bon niveau de lubrification (autrement dît un bon état du lubrifiant) et une gestion simple et peu coûteuse (évitant des travaux et des dépenses superflus).
Il existe deux types d’approche : l’approche calendaire et l’approche conditionnelle. L’approche calendaire est la plus communément utilisée. Elle consiste à estimer l’intervalle maximum acceptable techniquement. Celui-ci sert ensuite à planifier les opérations de lubrification dans le plan de maintenance. L’estimation se fait en général par le calcul. Pour les roulements par exemples, la détermination se fait à partir de théories éprouvées et le plus souvent normalisées, traduites sous formes de formules et d’abaques ou, plus simplement, traitées par des logiciels. Cette détermination peut être ensuite affinée par la constatation de la modification de l’état des lubrifiants ou de ces effets.
Ce dernier point nous conduit à la méthode conditionnelle, qui s’appuie sur l’observation de l’état du lubrifiant (mesures chimiques et physique, aspect, etc.) pour statuer le besoin ou l’urgence d’un renouvellement du lubrifiant. Par exemple, avant que quelques milliers de litres d’huiles soient vidangées et remplacées, il peut s’avérer pertinent d’estimer si l’huile n’est pas toujours en état de remplir son rôle comme attendu, particulièrement quand la capacité de production, la maitrise des coûts et la sauvegarde de l’environnement sont des priorités. Aussi, un suivi sur site (observations, prises et mesures d’échantillons, mesures en ligne), des analyses en laboratoire (de préférence suivies dans le temps) permettent d’optimiser les opérations de re-lubrifications. Elles peuvent par ailleursavoir pour vertu la détection et la qualification précoces de dysfonctionnement de certains équipements (l’usure par exemple).
La bonne quantité
Pour un bain d’huile, le cas est assez simple : l’observation visuelle permet d’ordinaire de déterminer quand faire un appoint d’huile (hublots de regard, regards tubulaires, etc.). Encore faut-il planifier correctement les inspections pour que ce soit fiable. Des systèmes d’alerte automatique se répandent aussi. Des systèmes simples et peu coûteux de maintien permettent de conserver un niveau constant, offrant tranquillité et sécurité. Pour les systèmes de dosage d’huile, les fabricants des machines ou des composants à lubrifier (chaines, roulements, etc.) pourront en général statuer. Un système de dosage assure l’approvisionnement à la quantité requise. Pour la graisse, il est important de reconnaitre qu’un excès de graisse peut être tout aussi néfaste qu’un manque de graisse (qui se comprend plus intuitivement). Il conviendra donc de calculer, toujours à partir d’abaques et de formules ou de logiciel, quelle est la quantité requise et de planifier périodiquement sa distribution à l’endroit prévu à cet effet. Si des systèmes de lubrification automatique (graisseurs automatiques, centrales de graissages) pourront notamment être utilisées pour fournir la graisse et éviter le surgraissage très couramment constaté en cas de lubrification manuelle (qui génère une inflation des dépenses et des souci techniques), leur débit doit être calculé et ajusté.
En outre, dans les applications susceptibles de surchauffer (souvent à vitesse plutôt élevée), il conviendra de s’assurer que la graisse usée a la possibilité de s’évacuer aisément (par les étanchéités ou par un trou d’évacuation)
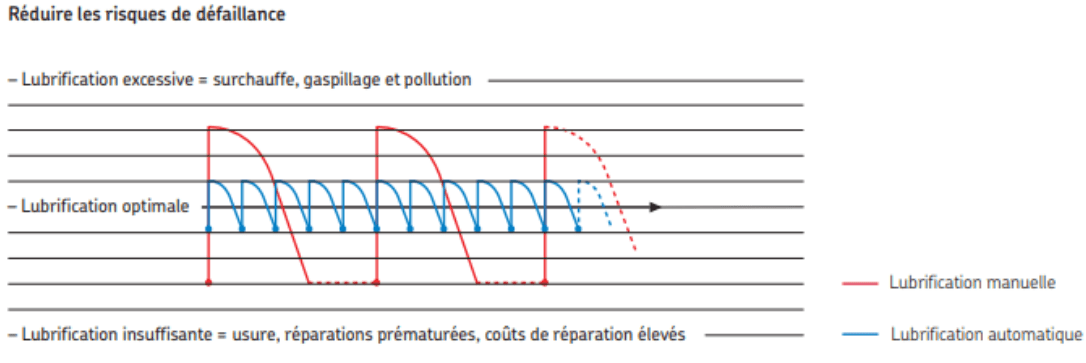
Le bon endroit
Dans l’esprit de certain, signifier qu’il est important de lubrifier au bon endroit peut se résumer à énoncer une lapalissade. Encore faut-il que le point de lubrification soit :
- Visible
- Equipé / connecté
- Correctement identifié
- Accessible sans danger
Dans certains cas, nous constatons même que le lubrifiant a relativement peu de chance d’atteindre son point de destination, notamment à cause d’erreurs de conception et de défaillance des tubes ou tuyaux d’amenée de lubrifiant. Pour s’assurer que l’approvisionnement en lubrifiant est effectif, il convient de contrôler régulièrement tous ces points. Pour simplifier la méthode et obtenir une meilleure maitrise du processus de lubrification, des codes couleurs et/ou des détrompeurs sont de plus en plus souvent utilisés et les informations nécessaires sont clairement et explicitement spécifiées sur les machines.
La bonne méthode
La bonne méthode mérite d’être
- Aussi simple que possible
- Propre
- Sure
- Planifiée et ordonnancée
- Maitrisée
Simplicité
Beaucoup de soucis de lubrification sont dus à des erreurs humaines. Plus les tâches sont simples (nombre limité de lubrifiants différents, accès et réalisation simple par du personnel formé, etc.), moins il y a d’erreurs humaines et moins l’exécution, le reporting et le contrôle demandent de temps. Une lubrification automatique, même simple, peut grandement simplifier l’exécution des tâches de lubrification et libérer du temps.
Propreté
Il a été spécifié plus tôt que la contamination à l’intérieur des machines était trop souvent liée à la lubrification. C’est pourquoi il est nécessaire de s’assurer :
- Que le lubrifiant est livré avec le niveau de propreté requis pour les machines ou, à défaut, de la filtrer
- Qu’il est stocké dans des conditions n’engendrent pas sa contamination
- Que le transfert et la manutention des lubrifiant sont aussi sans risque à ce niveau
- Que le lubrifiant est distribué de manière propre à l’intérieur de la machine
La lubrification automatique est aussi souvent un moyen de maitriser une partie des risques de contamination.
Sécurité
La sécurité du personnel est en jeu chaque fois qu’il se rend dans un endroit difficile d’accès, dangereux, en hauteur ou chaud. Donc chaque fois qu’une tâche de lubrification manuelle comportera un risque, il conviendra de l’adapter. Les fuites d’huile non-traitée peuvent rendre le sol glissant. Un excès de graisse tombant sur une source chaude peut-être source de feu. La contact direct et prolongé des lubrifiants avec le corps humain est fortement déconseillé, d’où l’importance de prévoir les EPI en conséquence.
Planification et ordonnancement
Afin qu’elles soient réalisées en temps et en heure, les tâches de lubrifications doivent être définies, décrites, programmées et réalisées par du personnel formé et ayant accès aux informations nécessaires. Un bon retour d’information permet un contrôle de l’exécution des tâches et une réaction rapide en cas de problème.
Maitrise
En plus des indispensables planification, ordonnancement et reporting des tâches, le suivi d’indicateurs de performance, préalablement définis à partir de la stratégie de lubrification, permet de piloter cette activité, d’en mesurer les bienfaits et de l’améliorer continuellement.
En résumé, la lubrification, même si elle se montre sous certains aspects indulgente et souple, requiert rigueur et analyse. Elle mérite, comme beaucoup d’autres activités de reposer sur un processus et une organisation bien établie pour répondre aux enjeux d’un site industriel, suivie et maitrisée. La mise en œuvre des conseils édictés ci-avant est un pas important vers l’excellence en lubrification, indissociable d’une bonne fiabilité des machines, de leur durabilité et d’une meilleure maîtrise des coûts.
Produits associés
Système de lubrification automatique monopoint SKF LAGD 125/WA2,en 125 ml
Testez ce système de lubrification automatique de SKF à la graisse ou à l’huile pour garantir que votre équipement bénéficie de la quantité adaptée de lubrifiant.
Système de lubrification automatique monopoint SKF LAGD 125/HMT68
Le lubrificateur automatique de SKF distribue l'huile adaptée à votre équipement à une vitesse préréglée pour économiser du temps et des efforts.
Système de lubrification automatique monopoint SKF LAGD 125/GB2, en 125 ml
Les lubrificateurs de point unique offrent plus de flexibilité dans de nombreuses applications, car ils fournissent automatiquement au bon moment, au bon endroit, la bonne quantité de lubrifiant.
Pour aller plus loin
Liens connexes
- Accessoires pour la lubrification
- Système de lubrification automatique monopoint Plastique SKF LGGB 2, 125 ml
- Système de lubrification automatique monopoint Plastique SKF LGWA 2, 250 ml
- Système de lubrification automatique monopoint SKF LGWA 2, 125 ml
- Système de lubrification automatique monopoint SKF System 24, 125mL
- Système de lubrification automatique monopoint SKF System 24, 250mL
- Comment optimiser la gestion des stocks des produits et assurer...
- Système de lubrification automatique monopoint Plastique SKF LGWA 2, 60 ml