- Publié le 31 mai 2023
- Mis à jour le 18 oct. 2024
- 10 min
Comment prévenir des ruptures mécaniques ?
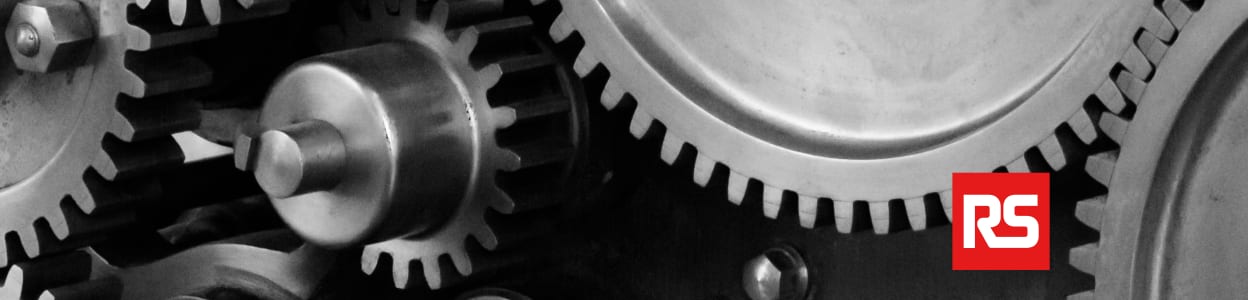
Dans un atelier, les arrêts ont pour origine des causes multiples, à commencer par la rupture des éléments mécaniques présents dans les machines ou les équipements de production. Des opérations de maintenance préventive s’imposent alors à condition de savoir où porter son attention. Face aux risques de rupture mécanique, voici quelques éléments à prendre en compte, tant dans l’identification des organes à surveiller que dans les moyens à mettre en œuvre pour limiter l’usure et éviter la casse.
Sur une ligne de production, le moindre arrêt peut coûter cher. Or il n’est pas toujours évident de percevoir les signes avant-coureurs d’une défaillance et des prémices d’une panne mécanique. Pourtant, bien souvent, la rupture d’un élément peut gripper une mécanique toute entière et stopper net la totalité de la production (en particulier dans les industries de process), entraînant des temps d'arrêt coûteux (l’immobilisation d’un équipement pouvant prendre des semaines voire des mois), une perte financière et de productivité voire des risques pour la sécurité des travailleurs, sans compter l’image de l’entreprise vis-à-vis de ses clients.
Ces défaillances mécaniques interviennent sur une grande variété de machines et d'équipements (pompes, les moteurs, les boîtes de vitesses, les convoyeurs, les turbines...) lorsqu'un composant ou une pièce d'équipement ne fonctionne plus comme prévu en raison d'un dommage, d'une contrainte ou d'une usure. Les causes de ces défaillances trouvent leurs origines dans la fatigue des matériaux, la corrosion, la surcharge ou encore une conception inadéquate de l’organe mécanique installé sur telle ou telle machine, mais aussi à un défaut de maintenance.
Quels risques de rupture et sur quels composants ?
Sur les différentes pièces d'un système de transmission de puissance, les ruptures mécaniques peuvent prendre plusieurs formes, selon la nature et l'intensité de la contrainte subie par le composant. Si l’on prend l’exemple d’un roulement, il est possible d’observer plusieurs signes de rupture mécanique tels que l’apparition de fissures ou de cassures sur la bague intérieure ou extérieure, mais aussi des déformations, des marques d'usure inégale ou de fatigue sur la surface de contact, ou encore la perte d’un bille ou d’un rouleau ; à ce titre, notons qu’une fois encore, il est important de faire appel à ses sens, notamment l’ouïe puisque ce phénomène peut entraîner un bruit ou un déséquilibre dans le fonctionnement du roulement.
Concernant les paliers, les poulies, les chaînes, les pignons, les cardans et autres pièces de fixation, les ruptures sur de telles pièces sont susceptibles d’entraîner des pertes de production, des accidents et de bien coûteux dommages matériels. Outre les phénomènes d’usure « normale », les ruptures de paliers – par exemple – peuvent survenir en raison d’une surcharge, d’un défaut de lubrification ou d’une surchauffe, causant des fissures ou des déformations. Celles-ci provoquant à leur tour des vibrations, des bruits ou même des pannes. Il en est de même pour les poulies ; mal installée ou en surcharge, une poulie peut elle aussi se fissurer ou se rompre sous l'effet de la tension de la courroie qui la maintient en rotation.
Pour ce qui relève des chaînes de transmission, celles-ci peuvent quant à elles rompre – et ce de manière soudaine – à cause d’une tension incorrecte, d’une usure excessive, de défauts de fabrication ou d’une surcharge.
Les pignons, les cardans ou encore les pièces de fixation peuvent à leur tour subir des ruptures. Les dents des pignons notamment s'usent voire se cassent sous l'effet d'une surcharge, d'une vibration ou d'une mauvaise lubrification… d’où une maintenance préventive régulière, prenant en compte le remplacement des pignons usés. Indispensables pour transmettre de la puissance entre deux points non alignés, les cardans sont quant à eux sujets à la rupture au niveau des soudures mais aussi des joints universels ou en raison de dommages causés par une surcharge et des vibrations excessives. Quant aux ruptures de pièces de fixation telles que les écrous, les vis, les boulons et les rivets, celles-ci peuvent avoir de graves conséquences sur l’outil de production et causer des accidents. N’oubliez pas de contrôler leur niveau de serrage régulièrement.
Comme on l’a évoqué précédemment, les ruptures ont pour cause divers phénomènes allant des vibrations excessives (vitesse inappropriée de la machine, sollicitant trop fortement les organes mécaniques) à la pression trop forte en passant par les phénomènes de frottement, provoquant une usure excessive, la performance inadéquate de la machine, des roulements mal réglés sans oublier le fait que certaines pièces de machines à hautes performances peuvent être soumises à des températures trop élevées (causant des échauffements et ainsi l'expansion de certains matériaux). Beaucoup de ruptures mécaniques tirent aussi leur origine dans une mauvaise lubrification, causant des frottements intenses, mais également dans le montage incorrect d'un roulement (risque de surcharge) ou encore un mauvais alignement pouvant entraîner des vibrations et des charges supplémentaires.
Reconnaître les signes de problèmes potentiels et les résoudre avant qu'ils ne s'aggravent
Prendre des mesures proactives pour prévenir ces problèmes, tel est l’objectif de nombreuses entreprises industrielles, notamment dans les domaines de la métallurgie et de la sidérurgie (en raison du coût et des délais astronomiques des arrêts de production) ou encore dans l’agroalimentaire ou l’industrie pharmaceutique ; en somme, partout où un arrêt de ligne de fabrication est tout simplement inenvisageable. Mais cela est – et doit être – le cas dans tous les ateliers de production.
Parmi les mesures de maintenance préventive à adopter figurent les opérations de contrôle périodique et systématique, la bonne utilisation des organes mécaniques et la machine (en fonction des spécifications d’installation ou de montage mentionnées par le constructeur), le recours à des matériaux adaptés à l’équipement permettant de réduire les risques de rupture ou encore s’assurer que la conception de l’équipement en question répond bien aux recommandations du fabricant en matière de stabilité et de durabilité. Il est important de surveiller plusieurs paramètres comme les niveaux de chaleur ou de modifier les caractéristiques des matériaux utilisés, les niveaux de lubrification, de serrage, de vibration et de tension de charge, sans oublier le remplacement systématique des roulements, les pignons et autres garnitures mécaniques.
Pour ce faire, il est conseillé d’une part d’intégrer davantage de composites avancés ou d’alliages métalliques conçus pour résister aux vibrations, mais aussi d'installer des dispositifs d'absorption des vibrations (amortisseurs, joints en caoutchouc…). D’autre part, il est possible d’utiliser un plot antivibratoire ; cette pièce mécanique est utilisée afin de limiter le déplacement d'un autre organe en lui faisant obstacle. Fabriqué à partir de matériaux élastomères et utilisé pour soutenir et stabiliser le fonctionnement de gros équipements (moteurs, pompes, compresseurs, générateurs...), ce dispositif sert dans le même temps de tampon amortisseur, absorbant à la fois vibrations et les chocs. Pourquoi pas non plus combiner ces différentes solutions avec un logiciel de simulation, offrant la possibilité de prévoir les niveaux de vibrations afin de concevoir des systèmes plus adaptés à l’environnement de l’atelier.
Aussi, pour assurer l'alignement et les tensions des courroies, il est important de suivre les instructions spécifiques fournies par le fabricant du mécanisme. Celles-ci portent par exemple sur le desserrage des boulons de fixation, le réglage de la position de la poulie et le resserrage des boulons. Il est également important de maintenir une tension correcte des courroies pour optimiser la performance du mécanisme ; dans ce cas, il est possible d’utiliser un tensiomètre de courroie et suivre les recommandations de tension du fabricant.
Bien sûr, la lubrification demeure à elle seule un élément incontournable pour prévenir des risques de rupture mécanique. En réduisant le frottement et l'usure entre les pièces mobiles, elle contribue en effet à prolonger la durée de vie des composants. Tout réside cependant dans l’identification des causes de rupture et l’adéquation entre les risques et les besoins de production, ceci allant orienter le choix du lubrifiant le mieux adapté. À ce titre, l’accompagnement du fournisseur d’huile est recommandé, à la fois pour bien choisir le modèle le plus adapté mais aussi dans l’utilisation même du lubrifiant… que ce soit sur le dosage et les intervalles de graissage ou la manière d’éviter le dépôt de saleté et de particules susceptible d’agresser les composants. Il est aussi possible d'ajouter des additifs chargés d’améliorer les propriétés du lubrifiant et ainsi augmenter sa viscosité et réduire les frottement et autres phénomènes de corrosion. Notons que l'analyse de l'huile et le prélèvement d’échantillons sur une machine permettent d'identifier les signes de mauvais fonctionnement tels que la présence de particules métalliques, d'eau ou d'autres contaminants.
S’orienter vers des solutions de maintenance conditionnelle
Il existe plusieurs moyens technologiques pour détecter et prévoir les ruptures mécaniques, à commencer par les capteurs de vibrations : ceux-ci permettent de mesurer les vibrations et les variations de fréquence d'une machine. Aussi, les systèmes de surveillance en ligne utilisent des capteurs capables de collecter des données en temps réel sur le fonctionnement d'une machine. L'analyse des données permet de prévoir les défaillances imminentes et de prendre des mesures préventives pour éviter la rupture mécanique. Les thermocouples jouent également un rôle important : en mesurant la température d'une machine, ils peuvent aider à détecter les anomalies thermiques qui pourraient indiquer une rupture mécanique. Mais au-delà, ne négligeons pas l’importance de l’inspection visuelle : un moyen traditionnel mais qui se révèle souvent fiable pour détecter les signes de dégradation.
Les solutions IoT et autres objets connectés s'avèrent eux aussi un bon moyen pour prévenir des défaillances mécaniques. À partir de capteurs positionnés sur les machines, il est possible de surveiller leur état et détecter tout signe de dysfonctionnement ou de panne imminente. Les données collectées par ces capteurs sont ensuite analysées par des algorithmes d'apprentissage automatique afin de détecter des schémas et des anomalies dans les données. Objectif ? Prévoir les pannes à l’avant qu'elles ne se produisent. Mais les solutions IoT peuvent également assurer une surveillance en temps réel des machines, ce qui permet aux opérateurs de détecter rapidement les problèmes qui surviennent et d'y répondre au mieux… Puis prendre in fine les décisions qui s’imposent afin de réduire le nombre de pannes et les risques de casse.
Produits associés
Roulement à billes rigide RS PRO
Les roulements à billes blindés métriques de RS PRO sont utilisé dans une large gamme d'applications mécaniques, telles que les moteurs, les pompes et les convoyeurs.
Courroie synchrone RS PRO Caoutchouc
Obtenez les meilleures performances pour votre application avec les courroies de temporisation dentées en caoutchouc MXL de RS PRO.
Chaîne à rouleaux Simple en Acier Witra 08B-1
Chaîne unidirectionnelle standard anglais