- Publié le 10 janv. 2023
- Mis à jour le 29 août 2023
- 11 min
L’intérêt des moteurs asynchrones en industrie
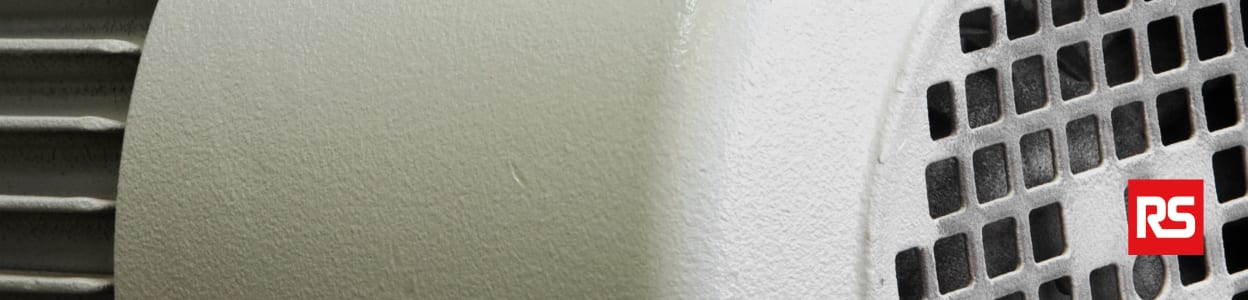
Article publié le 24/03/2021
Les moteurs asynchrones sont largement employés dans l’industrie. En effet, ils sont présents là où l’action mécanique alimentée par une source électrique est nécessaire, c’est-à-dire dans tous les espaces d’une entreprise et particulièrement dans les zones de production. Cet article a pour but de revenir sur les particularités de ces actionneurs électriques et les principales techniques de démarrage ou de contrôle pour leur permettre un fonctionnement optimal.
Quelles sont les particularités des moteurs asynchrones ?
Les moteurs asynchrones ont pour avantage d’être simples à mettre en œuvre, faciles d’entretien et abordables. Ils offrent l’avantage de s’alimenter directement par le réseau de distribution contrairement à d’autres types de moteurs (synchrones, à courant continu, pas à pas etc.).
Les moteurs asynchrones utilisent l'induction électromagnétique du bobinage de leur stator (partie fixe du moteur) pour produire un champ magnétique tournant. La force électromagnétique créée vient agir sur leur rotor (partie en mouvement du moteur) afin de générer un mouvement de rotation au bout de leur axe. La notion asynchrone s’explique par le fait qu’ils sont incapables d’atteindre la vitesse du champ tournant produite par leur stator (appelée également vitesse de synchronisme). Cette différence de vitesse exprimée en % est appelée glissement et obtenue par la relation ci-dessous.
s = (no – nn)/ no
- S = Glissement
- no= Vitesse du champ tournant
- nn= Vitesse de l'arbre moteur
La vitesse du champ tournant quant à elle s’exprime selon la relation suivante :
no = (f x 60)/p
- no = Vitesse du champ tournant
- f = Fréquence du réseau
- p = Nombre de paires de pôles
Ces relations démontrent ainsi les particularités des moteurs asynchrones qui fonctionnent selon une vitesse constante définie par la fréquence du réseau (50Hz en France) et le nombre de paires de pôles disponibles sur leur stator.
Quels sont les différents types de moteurs asynchrones ?
Il existe deux types de moteurs asynchrones, les moteurs à rotor type cage ou à rotor bobiné.
Les moteurs à cage sont les modèles les plus répandus. Leur rotor est constitué de conducteurs (ou barreaux) disposés en parallèle et court-circuités à leurs extrémités par deux anneaux. Cette structure ainsi constituée fait penser à une cage. Leur fabrication aisée, leur coût abordable et le fait qu’ils répondent à la majorité des applications ont orientés le choix des industriels sur cette technologie.
Les moteurs à rotor bobiné quant à eux sont équipés d’un rotor doté de bobines montées en étoile. Sa fabrication plus complexe le rend plus couteux mais apporte l’avantage d’offrir un couple plus élevé au démarrage et la possibilité d’ajuster la vitesse à l’aide de résistances. L’arrivée des démarreurs progressifs et des variateurs de fréquence ont rendu leur utilisation obsolète.
Dans quelles applications utilise-t-on des moteurs asynchrones ?
Ces moteurs à courant alternatif sont les plus couramment utilisés dans l’industrie. Les versions monophasées sont dédiées aux déplacements des petites charges. On les retrouve plus particulièrement dans les appareils électroménagers. Les modèles triphasés sont davantage utilisés pour les applications industrielles intensives telles que les compresseurs, pompes, systèmes de convoyeurs et le matériel de levage.
Quels sont les principaux circuits de démarrage et de contrôle ?
1 - Démarrage direct
Les moteurs asynchrones ont la particularité de pouvoir se brancher directement sur le réseau de distribution. Cependant le démarrage direct génère un courant d’appel pouvant atteindre 7 fois la valeur du courant nominal du moteur, ce qui peut amener des perturbations, chutes de tension ou encore des déclenchements de protections. Ceci implique que le réseau soit suffisamment dimensionné. Dans le cas contraire, il sera nécessaire d’opter pour un autre type de démarrage tel que l’étoile-triangle ou le démarreur progressif que nous évoquerons par la suite.
Pour des raisons de sécurité, il est nécessaire de faire appel à un minimum de protection pour effectuer le branchement sur le réseau. Ainsi un circuit démarrage direct élémentaire est réalisé avec des appareillages suivants :
- Sectionneur – porte fusible : permettant de couper l’alimentation du circuit de démarrage moteur (commande manuelle dans l’armoire de commande). Fonction 2 en 1 : Isolement par sectionnement et protection contre les courts-circuits à l’aide des fusibles de type aM.
- Contacteur : appareillage de commande permettant de contrôler le passage du courant à l’aide d’une bobine d’excitation (commande déportée sur le pupitre de commande de la machine).
- Relais thermique : dispositif de protection capable de couper le circuit en cas de surchauffe lié à une surcharge et de ce fait à l’élévation du courant.
*Représentation des composants pour le démarrage direct **:*
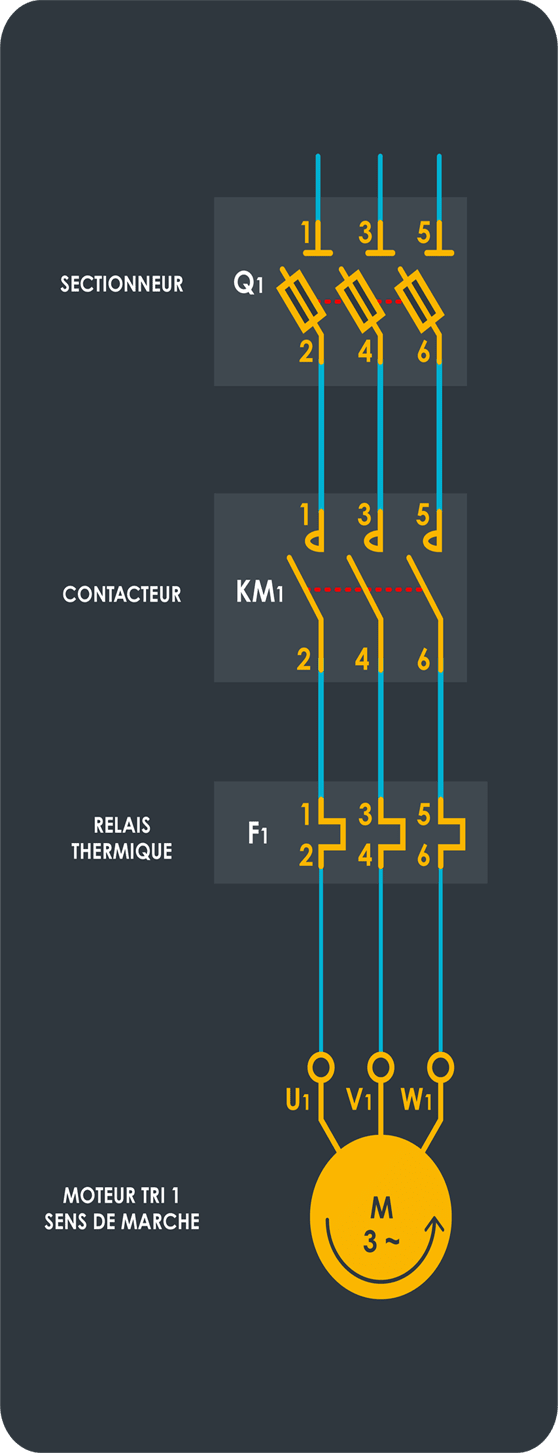
Démarreur DOL
Pour faciliter la mise en œuvre, les fabricants d’appareillage proposent des systèmes précâblés et prêts à être installer sous le nom de démarreur direct en ligne (DOL).
Faciliter la mise en œuvre
- Avantages : démarrage très simple, couple important
- Inconvénients : courant de démarrage élevé
- Type d'application : moteur de faible puissance
2 - Démarrage étoile/triangle
Le démarrage étoile/triangle permet notamment de réduire le courant de pointe au démarrage des moteurs. En effet le couplage étoile permet d’appliquer aux enroulements une tension divisée par racine de 3. Par conséquence, le courant d’appel et le couple sont plus faibles. Ceci a pour avantage de permettre un démarrage moins brusque des moteurs tout en limitant les contraintes sur la mécanique associée.
Le processus de démarrage s’effectue selon deux étapes. Le moteur est sollicité dans un premier temps et ce durant quelques seconds par un couplage étoile de ses bobines. La transition vers un couplage des bobines en triangle s’effectue ensuite afin d’atteindre pouvoir atteindre la vitesse nominale du moteur et ainsi de bénéficier de toutes ses capacités.
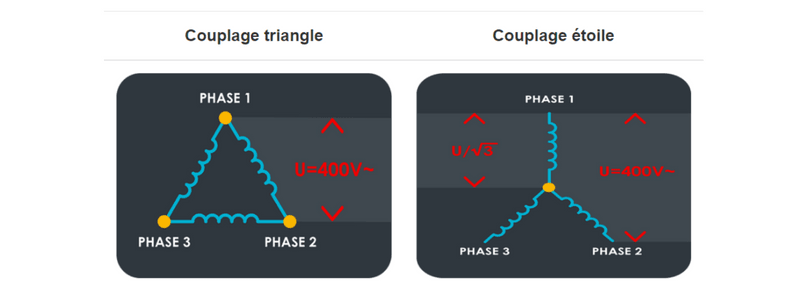
Il faut noter que le circuit étoile/triangle est uniquement possible si la boîte à bornes du moteur présente l’ensemble des connexions des bobines. Ce procédé est également réservé à des applications où le moteur est peu sollicité au démarrage.
Constitution d’un démarrage étoile – triangle :
- 1 Sectionneur – porte fusible : permet de couper l’alimentation du circuit de démarrage moteur (commande manuelle dans l’armoire de commande). Fonction 2 en 1 isolement par sectionnement et protection court-circuit à l’aide des fusibles de type aM.
- 3 Contacteurs : appareillages de commande permettant de contrôler le passage du courant à l’aide d’une bobine d’excitation (commande déportée sur le pupitre de commande de la machine).
- 1 pour le couplage étoile pendant le démarrage (KM1)
- 1 pour le couplage triangle pour la phase de fonctionnement (vitesse stabilisée) (KM3)
- 1 pour la commande moteur via le circuit de commande (pupitre)(KM2)
- 1 relais thermique : dispositif de protection capable de couper le circuit en cas de surchauffe lié à une surcharge et de ce fait à l’élévation du courant.
Schéma pour la représentation du démarrage étoile/triangle :
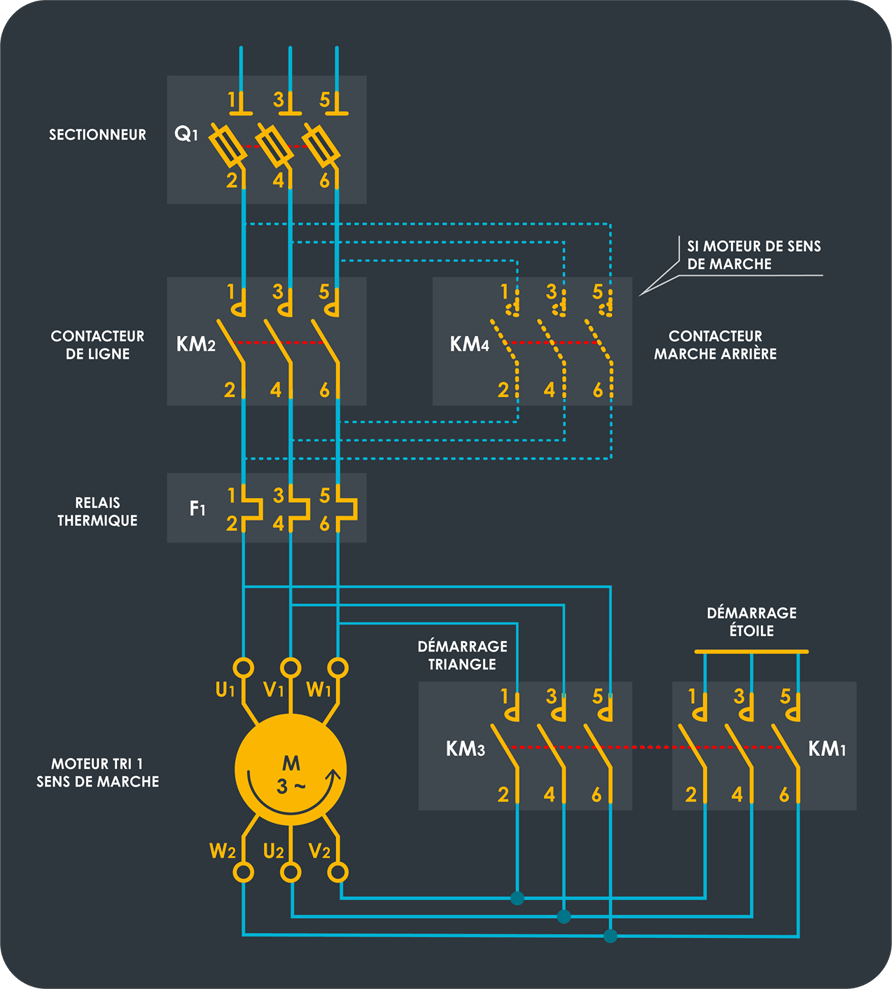
Démarrage étoile – triangle
Le démarrage étoile/triangle permet notamment de réduire le courant de pointe au démarrage des moteurs.
Informations principales
- Avantages : courant de démarrage plus faible, mise en œuvre relativement simple
- Inconvénients : couple de démarrage plus faible et à-coups lors de la transition étoile - triangle
- Type d'application : moteur de grande puissance
3 - Démarrage progressif
Le démarreur progressif est le premier dispositif de commande moteur intégrant des composants électroniques pour contrôler la vitesse et le couple des moteurs lors de leur phase de démarrage. Ces appareils électroniques utilisent les caractéristiques de déclenchement des thyristors et triacs pour contrôler la puissance de l’alimentation appliquée au moteur.
Ils utilisent le procédé de déclenchement à angle de phase. Cette technique effectue un amorçage par impulsion sur la commande (gâchette) du composant électronique pour créer un retard de conduction par rapport au passage par zéro de la tension alternative appliquée. Ainsi, la découpe (ou le hachage) de la tension obtenue permet une réduction de la valeur efficace de la puissance appliquée proportionnelle au temps conduction des composants électroniques.
Le principe reste uniquement dédié aux phases de démarrage car les conditions appliquées ne permettent pas aux moteurs de délivrer les performances nominales pour lesquelles il est conçu.
Représentation en schéma démarrage progressif :
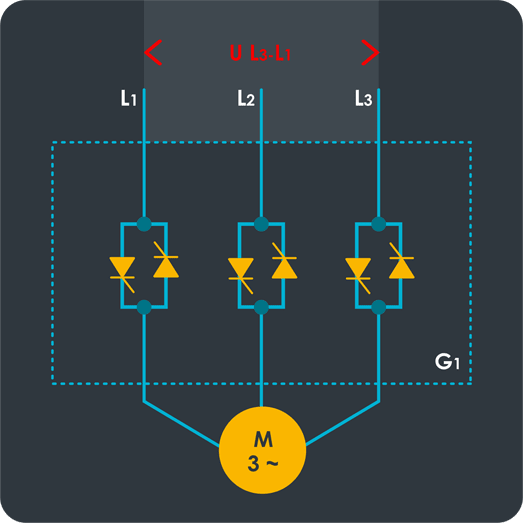
Démarreur progressif
Premier dispositif de commande moteur intégrant des composants électroniques.
Les avantages :
- Démarrage sans à-coup
- Montée progressive en vitesse
- Limitation de l’appel de courant au démarrage
- Attention : prix élevé du démarreur progressif
Variateurs de vitesse
Les systèmes évoqués précédemment sont destinés à accompagner les moteurs dans leur phase de démarrage pour atteindre leur vitesse fonctionnement. En effet, par leur conception les moteurs asynchrones fonctionnent à une vitesse constante déterminée notamment par le nombre de pôles dans leur bobinage, la fréquence de la tension d’alimentation et le glissement.
Avant l’apparition des variateurs de vitesse électroniques, les machines nécessitant une variation de vitesse dans le processus de fonctionnement utilisaient des moyens mécaniques basés sur des systèmes de poulies ou d’engrenage. Ces dispositifs mécaniques avaient un certain nombre d’inconvénients comme notamment une nuisance sonore accrue, un entretien soutenu et l’incapacité de maintenir le couple en cas de variation de la charge.
Les variateurs de fréquence ont balayé toutes ces problématiques et ont permis d’ajouter de nouvelles fonctionnalités comme la commande à distance, l’asservissement de la vitesse, la programmation des différentes phases de fonctionnement ou encore la communication avec d’autres machines comme les automates ou les salles de commande.
Le principe de fonctionnement du variateur consiste à redresser la tension alternative de l’alimentation pour obtenir une tension continue à l’aide d’un redresseur et d’un filtre de lissage associé. Cette transformation de la source d’alimentation offre la possibilité de la traiter de manière numérique afin de délivrer au moteur une source d’alimentation contrôlée selon les paramètres fréquence et tension via une modulation de large d’impulsion (MLI or PWM en anglais).
La vitesse de moteur est ainsi contrôlée en fréquence tout en agissant sur l’amplitude de sa tension afin de maintenir un couple constant. En effet, pour rappel, ces deux paramètres sont intimement liés par la relation suivante :
C = (U/f) x I
- C = couple moteur
- I = courant moteur
- f = Fréquence du réseau
- U = tension réseau
Le traitement numérique réalisé par un microcontrôleur a ainsi ouvert la voie aux nombreuses fonctionnalités évoquées précédemment, mais on peut noter également, qu’il permet de délivrer uniquement la quantité d’énergie nécessaire au moteur. Il contribue ainsi à améliorer significativement l’efficacité énergétique des machines, ce qui incite les entreprises à choisir ce mode contrôle pour réduire leur consommation électrique. Cette démarche est d’ailleurs fortement encouragée par les instances européennes avec la mise en application de la norme CEI 60034-30-1.
Variateurs de vitesse
Le principe de fonctionnement du variateur consiste à redresser la tension alternative de l’alimentation pour obtenir une tension continue à l’aide d’un redresseur et d’un filtre de lissage associé.
Les avantages
- Réglage de la vitesse du moteur et couple constant
- Possibilité de variation facile et précise
- Rampe de démarrage, de décélération
- Démarrage plus souple
- Attention : Création de courant d’harmonique (perturbations électriques)
Les moteurs asynchrones de type cage sont les plus utilisés dans l’industrie. Ils sont reconnus pour être simples à mettre en œuvre, faciles d’entretien et abordables. Leur capacité à se brancher en direct sur le réseau d’alimentation a contribué à leur succès dans l’industrie. Les dispositifs mécaniques ajoutés pour permettre la variation de vitesse apportent une nuisance sonore accrue, un entretien soutenu et l’incapacité de maintenir le couple en cas de variation de la charge. Ces inconvénients sont dorénavant écartés grâce à l’arrivée de variateurs de fréquence et leurs nombreux avantages permettront à ce type de moteur d’entrer sereinement dans le monde de l’industrie du futur.
Produits associés
Variateurs vitesse
Un variateur de fréquence régule la vitesse/la fréquence d'un moteur électrique à courant alternatif en variant la tension et la fréquence
Démarrage direct
Les démarreurs directs en ligne (DOL) ou démarreurs en ligne sont les démarreurs à usage général les plus courants.
Démarreur étoile/triangle
Un démarreur de moteur est un dispositif pour les applications de commande de moteur, qui est utilisé pour démarrer et arrêter un moteur
Démarrage progressif
Un démarreur est un commutateur électromécanique similaire à un relais.
Pour aller plus loin
Liens connexes
- Démarreurs moteurs
- Démarreur étoile-triangle 55 kW 110 → 120 V c.a. 11 A
- Moteur asynchrone triphasé : Comment préserver les performances et...
- Démarreur étoile-triangle 15 kW 400 V c.a. 13 → 18 A
- Démarreur étoile-triangle 11 kW 400 V c.a. 9 → 14 A
- Démarreur étoile-triangle 30 kW 400 V c.a. 32 → 38 A
- Démarreur progressif progressif 75 kW @ 400 V c.a. 187 → 575 V c.a. 150 A
- Comment choisir son moteur électrique ?