- Publié le 9 déc. 2024
- Mis à jour le 9 déc. 2024
- 6 min
Real Time Monitoring : mesurer et surveiller en temps réel les lignes de production
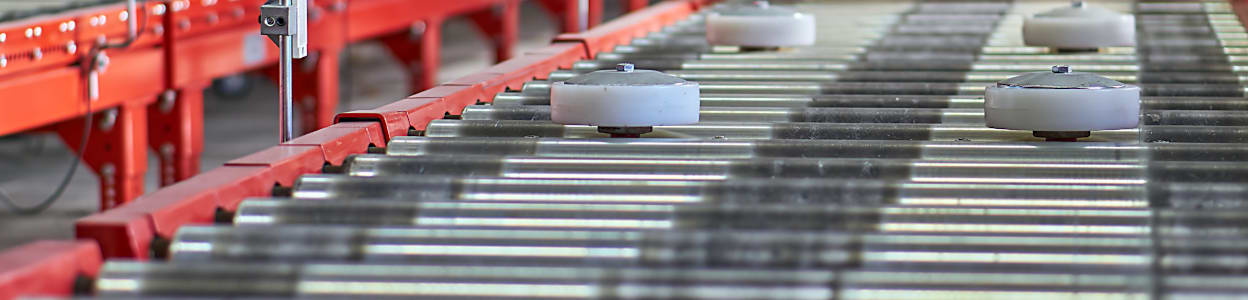
Le Real Time Monitoring (RTM), ou surveillance en temps réel, est devenu une pratique essentielle dans le secteur industriel confronté à la recherche constante de compétitivité. Les entreprises cherchent en effet à optimiser leur processus, à prolonger la durée de vie de leurs équipements et à réduire les temps d’arrêts de production. Grâce aux technologies d’automatisation proposées par RS, les entreprises industrielles sont en mesure de surveiller en continu les équipements critiques et de suivre en temps réel permet de détecter les anomalies avant qu’elles ne causent des pannes.
Pourquoi surveiller en continu les équipements critiques ?
Le Real Time Monitoring offre une visibilité instantanée sur les opérations et équipements critiques pour faciliter une maintenance proactive et optimiser les processus.
Éviter les arrêts imprévus
Les arrêts de production non planifiés peuvent se révéler extrêmement coûteux pour les entreprises. Une panne soudaine entraîne non seulement des coûts de réparation d’urgence, mais impacte également la productivité et les délais de livraison. La surveillance en temps réel permet de détecter les signes précurseurs de défaillances — comme une chute de pression, une augmentation de la température ou des vibrations inhabituelles — bien avant qu’ils ne deviennent critiques. Les entreprises peuvent ainsi planifier des interventions préventives pour limiter les interruptions imprévues et optimiser la maintenance.
Améliorer la durée de vie des machines
Grâce au suivi en temps réel, les entreprises prolongent la durée de vie de leurs équipements. Identifier et corriger les anomalies dès leur apparition est le meilleur moyen d’éviter une dégradation progressive qui affecterait la machine sur le long terme. Par exemple, une légère surchauffe non détectée peut rapidement endommager des composants clés si elle persiste. Une surveillance constante permet de réduire ce type de risques. Autre avantage : les investissements en équipements lourds peuvent être amortis sur une plus longue période.
Optimiser la maintenance et les processus
La maintenance évolue alors vers une approche prédictive, où les interventions sont réalisées en fonction de l’état réel des machines et non selon un calendrier prédéfini. Cela permet de mieux gérer les ressources, de réduire les coûts de maintenance et d’optimiser l’efficacité des équipes techniques.
Par ailleurs, les responsables de maintenance peuvent aussi ajuster les paramètres de production en temps réel grâce à l’accès constant aux données actualisées sur la performance des machines. L’objectif est de réduire les déchets, d’optimiser la consommation d’énergie et d’améliorer la productivité globale.
Protéger les employés et prévenir les risques
La surveillance en temps réel touche directement la sécurité des opérateurs travaillant sur la ligne de production. Les anomalies comme des variations de pression ou des températures élevées sont plus facilement détectées et donc rapidement réparées, avant qu’un accident ne survienne. Une maintenance proactive et bien planifiée réduit également les interventions d’urgence sur des machines en panne, ce qui limite l’exposition des employés à des situations dangereuses.
Faire monter en compétence ses équipes
Les systèmes de Real Time Monitoring contribuent aussi à la formation des équipes techniques. En analysant les données des capteurs, les techniciens acquièrent une meilleure compréhension des processus et des causes de défaillance. Ils peuvent ainsi anticiper les problèmes et ajuster les pratiques pour renforcer leurs compétences et leur expertise. Une approche data-driven améliore la gestion des équipements et la communication entre les équipes.
Le suivi en temps réel pour détecter les anomalies avant qu’elles ne deviennent des pannes
Une détection proactive grâce aux capteurs
Les systèmes de Real Time Monitoring reposent sur un réseau de capteurs installés sur les machines. Ces capteurs collectent des données en continu : température, vitesse, vibration, consommation d’énergie... Dès qu’un paramètre dépasse les seuils définis, le capteur envoie une alerte pour signaler une possible défaillance. La détection proactive permet d’intervenir rapidement et de planifier des actions correctives avant que l’anomalie ne conduise à une panne complète.
Par exemple, dans une ligne de production, une variation de la consommation d’énergie est symptomatique d’un moteur défaillant. Les équipements de gestion d’énergie sont capables de la détecter et de déclencher une intervention rapide qui évite des réparations couteuses en limitant l’impact sur la production.
Analyse et amélioration continue des processus
La surveillance en temps réel génère aussi une quantité considérable de données exploitables pour optimiser les processus de production. En analysant ces données, les responsables peuvent identifier des tendances, repérer les points faibles et ajuster les réglages pour améliorer l’efficacité. L’amélioration continue s’inscrit d’ailleurs dans une démarche d’excellence opérationnelle qui contribue à la compétitivité de l’entreprise.
L’impact des technologies IoT sur la surveillance en temps réel
L'Internet des objets (IoT) au service du Real Time Monitoring
L’intégration des technologies IoT dans le Real Time Monitoring a révolutionné la gestion des lignes de production. Les capteurs connectés permettent une collecte de données en temps réel, même à distance, et centralisent les informations dans des plateformes spécialisées.
Ils offrent ainsi une vue d'ensemble précise et instantanée de l’état des équipements qui facilite une prise de décision rapide. Les données recueillies sont stockées et analysées automatiquement pour anticiper les problèmes et optimiser la maintenance.
Des usines intelligentes grâce à l’automatisation des processus
Les usines intégrant des solutions IoT deviennent plus autonomes et intelligentes. Les systèmes peuvent, par exemple :
- déclencher des alertes automatiques ;
- ajuster les paramètres des machines en temps réel en cas de déviation ;
- commander des pièces de rechange si nécessaire.
Cette automatisation améliore la réactivité, réduit les marges d’erreur et optimise les coûts opérationnels. Une infrastructure d’automatisme et de contrôle de process permet également aux gestionnaires de concentrer leurs efforts sur des tâches plus stratégiques et d’optimiser la chaîne de production dans son ensemble.
Le Real Time Monitoring représente une avancée majeure pour la gestion des lignes de production, en permettant une surveillance continue et proactive des équipements critiques. Grâce à l’Internet des objets et à des capteurs sophistiqués, les entreprises sont en mesure d’anticiper les problèmes, réduire les arrêts imprévus, optimiser la maintenance et prolonger la durée de vie des machines. En parallèle, ces technologies renforcent la sécurité des employés et favorisent une amélioration continue des processus industriels. Investir dans la surveillance en temps réel, c'est donc opter pour une gestion intelligente et performante des ressources qui garantit une compétitivité accrue sur le long terme.