- Publié le 10 janv. 2023
- Mis à jour le 28 janv. 2025
- 14 min
Comment prévenir la fuite d'air comprimé dans le circuit ?
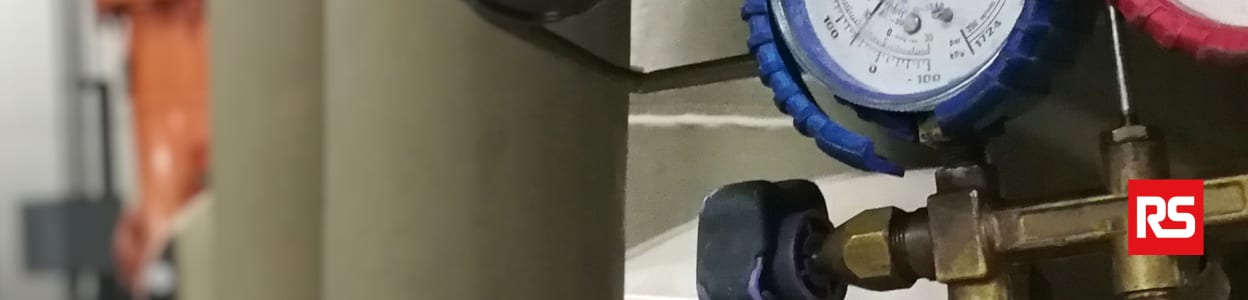
Dans l’industrie agroalimentaire, le bon fonctionnement des appareils utilisant de l’air comprimé est primordial pour garantir la qualité de la production. Il convient notamment d’éviter les fuites d’air afin de limiter les coûts d’exploitation, de maintenance et de réparation. Grâce à des interventions préventives ciblées, la fiabilité des installations est préservée. L’air comprimé est utilisé principalement pour faire fonctionner des outils pneumatiques destinés à la production, le conditionnement ou le nettoyage.
Pourquoi éviter les fuites d'air comprimé ?
L’air comprimé est utilisé dans un grand nombre d’industries manufacturières. Dans les systèmes industriels, l'air comprimé est essentiel pour le fonctionnement des machines et des outils. Afin d’avoir un système fiable et efficace, l’air comprimé et les autres gaz utilisés (comme l’azote par exemple) doivent avoir une pression déterminée. Le gaspillage d'air dû aux fuites peut entraîner des coûts élevés et des dépenses inutiles. Toute fuite d’air peut avoir des conséquences importantes.
Éviter la surconsommation d’énergie
Un système sujet à des fuites augmente la consommation d’énergie, car les compresseurs ou générateurs d’air comprimés doivent se déclencher plus souvent pour compenser la fuite, y compris lorsque alors que tous les équipements sont à l’arrêt.
On estime qu’un trou de 3 mm de diamètre dans un circuit d’air comprimé avec une pression de 6 bars peut générer des fuites coûtant près de 6000 € par an, précise Antoine Lavaux, responsable produits Instrumentation industrielle chez le fabricant SICK. Or, l’enjeu actuel est de réduire la consommation énergétique des installations, à la fois pour atteindre la neutralité carbone à l’horizon 2030-2040, mais surtout pour compenser la hausse brutale des coûts de l’énergie.
Garantir la qualité de la production
Les fuites peuvent conduire à des arrêts de production à cause des chutes de pression, les appareils pneumatiques étant insuffisamment alimentés en air. Par ailleurs, une pression insuffisante nuit à la qualité des produits fabriqués ou altère leur conditionnement.
Une fuite d’air peut également occasionner des contaminations aux impacts non négligeables sur la sécurité alimentaire ou la conformité du produit.
Améliorer l’efficacité de la maintenance
L’absence de détection d’une fuite d’air peut conduire à faire réparer un appareil qui, en réalité, fonctionne bien. Le fonctionnement d’un circuit d’air comprimé génère dans tous les cas des dégradations inévitables, notamment au niveau des raccords.
On peut réduire les risques ou retarder l’usure en utilisant des composants et raccords ou tubes pneumatiques de qualité, préconise le fabricant EMERSON AVENTICS. Il est également nécessaire de réaliser des contrôles périodiques pour détecter l’apparition de fuites au cours de la vie de la machine.
Pour toutes ces raisons, il est primordial d’éviter autant que possible les fuites d’air comprimé dans le système de production de l’air, mais aussi au niveau de sa distribution.
Comment détecter une fuite d’air comprimé ?
Un réseau d’air comprimé se compose schématiquement de trois grands types de circuits :
les circuits primaires entre le générateur et les distributions, à fort débit ;
les circuits secondaires alimentant les unités de productions ;
les circuits d’alimentation des machines elles-mêmes.
Les fuites peuvent intervenir sur ces différents circuits. Les points de fuite les plus fréquents sont les suivants :
purgeurs de condensat ;
brides, couplages et raccordements ;
FRL (filtre/régulateur/lubrifiant) ;
flexibles et garnitures ;
réservoirs de stockage ;
raccords, tubulures et valves.
L'utilisation de l'ensemble de microphones miniatures dans la caméra acoustique ii900 permet de capturer à la fois les ondes sonores et ultrasonores, contribuant ainsi à la précision dans l'identification des fuites grâce à la technologie innovante intégrée à l'appareil.
Les fuites d’air sont difficiles à détecter. L’installation de capteurs sur les circuits permet de monitorer la consommation d’air et d’indiquer s’il y a une fuite. En complément, les inspections permettent de localiser la fuite pour qu’elle soit réparée.
Les capteurs sur le circuit d’air et le monitoring
Les capteurs sont installés directement sur les circuits d’air comprimé, à différents niveaux. Les capteurs FTMg les plus basiques permettent de mesurer instantanément le débit d’air comprimé, sa pression et sa vitesse de circulation.
Le but est d’avoir des données instantanées de consommation, mais aussi des données cumulées que l’on va pouvoir interpréter, précise le fabricant SICK. Par exemple, une surconsommation d’énergie, une chute de pression ou un pic de consommation pendant un temps d’arrêt signale qu’il y a sans doute une fuite d’air.
Pour le fabricant EMERSON AVENTICS, le débitmètre suit en temps réel la consommation d’air comprimé et d’alerter par une alarme si elle est anormale, ce qui permet d’intervenir très rapidement pour corriger la source de la fuite.
Dans les versions les plus élaborées, les capteurs avec webserver sont reliés à des plateformes d’analyse qui visent à optimiser l’efficacité énergétique du circuit d’air comprimé ou de toutes les énergies consommées par l’installation. EMERSON AVENTICS propose un outil nomade et clé en main sous forme de valise « Smart Pneumatic Analyzer » qui affiche les données (pression, débit d’air, température…) sous forme de graphiques et de tableaux répertoriant les coûts, la consommation électrique et même l’empreinte carbone associée.
La détection des fuites d’air en inspection
Il existe une formule pour mesurer l’ampleur des fuites d’air comprimé dans une installation : Fuite (en %) = (Temps de charge en minutes x 100) / (temps de charge en minutes + temps de déchargement en minutes). Cette mesure s’effectue au compresseur d’air en dehors de toute utilisation pour la production. Elle nécessite de connaître le temps moyen de déchargement du système.
La détection des fuites d’air dans une installation n’est pas forcément aisée, car elles peuvent être nombreuses et parfois infimes. Les quatre méthodes de détection traditionnelles sont :
la présence de sifflement indique une fuite importante, puisqu’il faut un niveau sonore de 60 dBA pour être audible sans équipement de détection ;
la pulvérisation d’eau savonneuse sur une zone suspecte fait apparaître des bulles en cas de fuite, mais il s’agit d’une méthode artisanale et imprécise, généralement impossible à mettre en œuvre en agroalimentaire ou en présence de circuits électriques ;
la détection acoustique utilise les ultrasons grâce à un appareil spécifique et des écouteurs ;
la visualisation par imagerie ultrasonore permet de localiser les fuites grâce à une caméra acoustique et ultrasonique. Cet appareil ne nécessite pas l’intervention d’un technicien spécialisé et peut être utilisé même lorsque l’équipement fonctionne.
En plus de ces méthodes, il est crucial de fournir des informations sous forme de ressources pédagogiques et de conseils pour optimiser l'utilisation de l'air comprimé, notamment par le biais de partenariats comme le Compressed Air Challenge.
Chaque fuite détectée doit être identifiée par une étiquette afin d’être surveillée et réparée en temps voulu.
Comment réparer et réduire les fuites d'air comprimé ?
Une fois les fuites détectées et localisées, il convient de les éliminer, puis d’éviter qu’elles se renouvellent. Les services de détection et de réparation des fuites d'air comprimé sont essentiels pour réduire les coûts d'énergie et améliorer l'efficacité opérationnelle.
La réparation des fuites d'air
La réparation s'effectue par des méthodes classiques de colmatage :
- scellement des filets ;
- remplacement des filtres ;
- serrage des raccords ou remplacement lorsqu'ils sont défectueux.
Il est conseillé d'adopter une approche globale en ne réparant pas les fuites seulement au coup par coup. Souvent, les petites fuites en entraînent d'autres et rendent tout le système instable ou peu fiable.
Lorsque les fuites sont complexes à réduire ou éliminer et quand la machine a de nombreux temps d'arrêts, EMERSON AVENTICS propose une solution de mise en veille automatique et autonome de la pression. Cela permet réduire les coûts énergétiques lorsque la machine n'est pas en fonctionnement, le redémarrage étant automatique. Cette solution n'est pas intrusive dans l'automatisme existant de la machine, puisque le programme automate n'est pas modifié. De plus, elle permet de couper complètement la pression en cas d'arrêt prolongé (plus de consommation d'air liée aux fuites), tout en remontant les données mesurées par le débitmètre AF2 à un système SCADA/Cloud via une communication OPC-UA.
Un objectif : anticiper les fuites d'air
Des inspections fréquentes, en dehors des audits réguliers et réglementaires sont également recommandés pour réduire la probabilité de fuites dans les circuits. La détection par imagerie ultrasonore permet en outre de ne pas arrêter la chaîne de production, un élément non négligeable qui évite des pertes de rentabilité.
La mise en place d'une solution globale d'Energy Monitoring de SICK permet de conserver une traçabilité des données et de les faire remonter vers une plateforme numérique. Elle permet une analyse plus poussée des données et surtout une récupération de ces dernières en continu pendant le fonctionnement des machines. Ainsi, il est possible d'agir dès que l'on enregistre une consommation anormale ou un pic de consommation, mais aussi de comparer les performances des machines ou d'optimiser leur maintenance en allant vers une maintenance ajustée et non plus systématique. L'enjeu est d'arriver à optimiser les coûts de fabrication grâce à une connaissance fine des données, mais cela nécessite aussi des compétences en interne d'interprétation.
Selon SICK, jusqu'à présent,
“Les industries avaient tendance à être peu équipées en capteurs, car le coût de l'énergie avait moins de poids. Aujourd'hui, la hausse de ces dépenses énergétiques met en péril la rentabilité des entreprises et a apporté un caractère d'urgence à cette problématique de correction des fuites d'air.”
La réparation des fuites d’air
La réparation s’effectue par des méthodes classiques de colmatage :
- scellement des filets ;
- remplacement des filtres ;
- serrage des raccords ou remplacement lorsqu’ils sont défectueux.
Il est conseillé d’adopter une approche globale en ne réparant pas les fuites seulement au coup par coup. Souvent, les petites fuites en entraînent d’autres et rendent tout le système instable ou peu fiable.
Lorsque les fuites sont complexes à réduire ou éliminer et quand la machine a de nombreux temps d’arrêts, EMERSON AVENTICS propose une solution de mise en veille automatique et autonome de la pression. Cela permet réduire les coûts énergétiques lorsque la machine n’est pas en fonctionnement, le redémarrage étant automatique. Cette solution n’est pas intrusive dans l’automatisme existant de la machine, puisque le programme automate n’est pas modifié. De plus, elle permet de couper complètement la pression en cas d’arrêt prolongé (plus de consommation d’air liée aux fuites), tout en remontant les données mesurées par le débitmètre AF2 à un système SCADA/Cloud via une communication OPC-UA.
Un objectif : anticiper les fuites d'air
Des inspections fréquentes, en dehors des audits réguliers et réglementaires sont également recommandés pour réduire la probabilité de fuites dans les circuits. La détection par imagerie ultrasonore permet en outre de ne pas arrêter la chaîne de production, un élément non négligeable qui évite des pertes de rentabilité.
La mise en place d'une solution globale d'Energy Monitoring de SICK permet de conserver une traçabilité des données et de les faire remonter vers une plateforme numérique. Elle permet une analyse plus poussée des données et surtout une récupération de ces dernières en continu pendant le fonctionnement des machines. Ainsi, il est possible d'agir dès que l'on enregistre une consommation anormale ou un pic de consommation, mais aussi de comparer les performances des machines ou d'optimiser leur maintenance en allant vers une maintenance ajustée et non plus systématique. L'enjeu est d'arriver à optimiser les coûts de fabrication grâce à une connaissance fine des données, mais cela nécessite aussi des compétences en interne d'interprétation.
Selon SICK, jusqu'à présent,
“Les industries avaient tendance à être peu équipées en capteurs, car le coût de l'énergie avait moins de poids. Aujourd'hui, la hausse de ces dépenses énergétiques met en péril la rentabilité des entreprises et a apporté un caractère d'urgence à cette problématique de correction des fuites d'air.”
Un objectif : anticiper les fuites d’air
Des inspections fréquentes, en dehors des audits réguliers et réglementaires sont également recommandés pour réduire la probabilité de fuites dans les circuits. La détection par imagerie ultrasonore permet en outre de ne pas arrêter la chaîne de production, un élément non négligeable qui évite des pertes de rentabilité.
La mise en place d'une solution globale d'Energy Monitoring de SICK permet de conserver une traçabilité des données et de les faire remonter vers une plateforme numérique. Elle permet une analyse plus poussée des données et surtout une récupération de ces dernières en continu pendant le fonctionnement des machines. Ainsi, il est possible d'agir dès que l'on enregistre une consommation anormale ou un pic de consommation, mais aussi de comparer les performances des machines ou d'optimiser leur maintenance en allant vers une maintenance ajustée et non plus systématique. L'enjeu est d'arriver à optimiser les coûts de fabrication grâce à une connaissance fine des données, mais cela nécessite aussi des compétences en interne d'interprétation.
Selon SICK, jusqu'à présent,
“Les industries avaient tendance à être peu équipées en capteurs, car le coût de l'énergie avait moins de poids. Aujourd'hui, la hausse de ces dépenses énergétiques met en péril la rentabilité des entreprises et a apporté un caractère d'urgence à cette problématique de correction des fuites d'air.”
La fiabilité du système de production et de distribution de l’air comprimé repose en partie sur l’absence de fuites d’air tout au long de la chaîne. La mesure de la consommation d’air comprimé combinée à une maintenance régulière et minutieuse permet des économies significatives et une amélioration de la rentabilité.
Produits associés
Capteur de pression Sick PBS Plus
Le PBS plus est un pressostat électronique, un transmetteur de pression et un affichage en un et est disponible avec jusqu'à deux sorties de commutation, une sortie analogique et IO-Link.
Débitmètres EMERSON-AVENTICS
La série Aventics AF2 est un capteur de débit qui surveille la consommation d'air dans les systèmes pneumatiques, permettant une intervention rapide en cas de fuite.
Filtres régulateurs EMERSON-AVENTICS
Le régulateur de filtre pneumatique Aventics 5 mm est doté d'une connexion de port G 1/4". Il nettoie et enlève les humectures d'air dans un système à air sous pression.
Capteur de pression Sick PBT
Le PBT est un transmetteur de pression électronique universel, il est adapté pour les applications de mesure standard dans l'ingénierie de machines et d'usines, les systèmes de contrôle de pression, l'hydraulique, le pneumatique, etc.