- Publié le 9 janv. 2023
- Mis à jour le 14 oct. 2024
- 6 min
Comment utiliser l'IA et la maintenance prédictive dans la maintenance industrielle ?
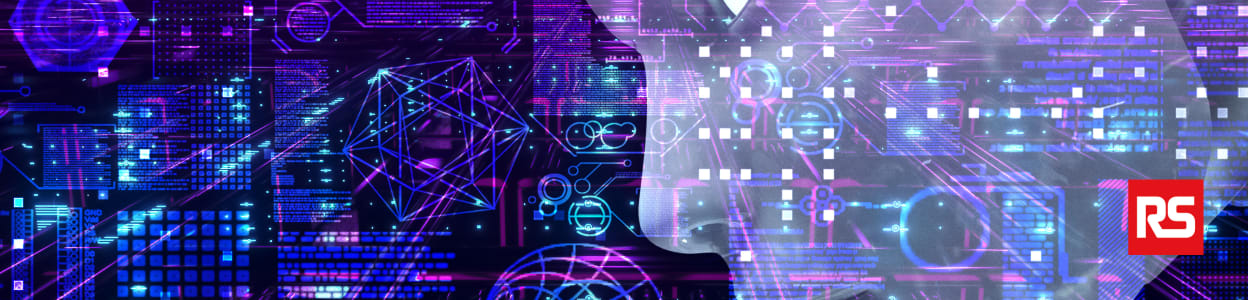
L'intelligence artificielle fait partie de ces innovations structurelles qui ont un impact dans de nombreux domaines. Si ses racines remontent aux années 50, les récentes évolutions technologiques, incluant notamment le machine learning et le deep learning, ouvrent de nouvelles possibilités pour utiliser l'intelligence artificielle dans la maintenance industrielle. Explications.
Au commencement fut la donnée
Dans notre monde, l'intelligence artificielle (IA) n'a pas encore les capacités de Jarvis dans « Iron Man » ou de HAL dans « 2001, l'Odyssée de l'espace ». Techniquement, il s'agit donc d'un programme conçu par des développeurs informatiques qui évolue selon les données auquel il est exposé. L'IA fonctionne grâce aux données qu'on accepte de lui donner. S'il n'y a pas de données, il n'y a pas d'intelligence artificielle, et c'est probablement le point le plus important à prendre en compte.
Dans les outils de production industriels, la donnée peut venir de deux grandes sources :
- des outils, machines, équipements ou lignes de production qui sont connectés par nature et capables de communiquer avec des plateformes numériques,
- des capteurs qui sont ajoutés à des outils, machines, équipements ou lignes de production et qui permettent de mesurer différentes variables comme la température, les vibrations, l'humidité, la pression, les cycles d'utilisation, etc.
Toutes ces données sont ensuite collectées et agrégées au sein d'un système centralisé. Pour chercher des informations, analyser des données, recueillir des contenus et trouver des corrélations entre différentes variables, l'IA est imbattable. Elle travaille 365 jours par an et vingt-quatre heures sur vingt-quatre. Elle est derrière Amazon, Netflix, mais aussi Office 365, Oracle, Adobe et beaucoup de solutions professionnelles. Il est donc naturel qu'elle trouve sa place dans le monde industriel pour éliminer ou réduire l'incertitude liée à la prise de décision.
L'impact de l'IA sur la maintenance
Les pannes des équipements industriels représentent un coût très important pour les entreprises et les outils de production. Dans le secteur manufacturier, la Société Internationale d’Automatisation estime que les industriels perdent chaque année 647 milliards de dollars dans le monde en raison des temps d’arrêt. Pour lutter contre cet état de fait, les professionnels de la maintenance du matériel ont développé des stratégies et des processus avec 4 types de maintenance :
- la maintenance corrective qui vise à intervenir en cas de panne pour limiter les impacts et trouver des solutions rapides,
- la maintenance curative qui vise à réparer en profondeur ou à remplacer un équipement ou un système,
- la maintenance préventive qui consiste à faire une inspection régulière de l'équipement,
- la maintenance prédictive qui se base sur l'intelligence artificielle pour anticiper les risques de pannes et intervenir avant même que celles-ci ne se produisent.
C'est avec la maintenance prédictive que l'intelligence artificielle joue un rôle important. Les entreprises adoptent ainsi une approche plus proactive dans leur stratégie de maintenance. Le responsable de la maintenance et ses équipes de techniciens peuvent intervenir en anticipant les besoins afin de limiter le dérangement et avant qu'une défaillance ne se produise. Pour cela, ils se basent sur les données des capteurs IoT au sein d'un logiciel de GMAO (Gestion de Maintenance Assistée par Ordinateur) afin de surveiller les anomalies et utiliser des modèles prédictifs pour demander une intervention humaine.
Grâce à l'intelligence artificielle, toutes les données recueillies sont analysées en temps réel afin de trouver des relations entre les données historiques et les relevés actuels, mais aussi d'alerter les techniciens en cas de risque de panne. Cette stratégie évite notamment de mettre à l'arrêt une ligne de production quand ce n'est pas utile et réduit les maintenances correctives et curatives qui coûtent cher et qui désorganisent l'activité.
Pour réaliser la transition vers une maintenance 4.0, il est important d'y aller progressivement selon votre niveau de départ, vos ressources internes et votre appétence pour le numérique. En effet, chaque évolution technologique implique des changements plus ou moins profonds qui touchent à la fois votre organisation, vos équipes et votre infrastructure technique. La première à faire est donc d'auditer et de cartographier vos processus internes et vos flux de données. Qu'est-ce qui fonctionne ? Qu'est-ce qui pourrait être amélioré ? Comment les rôles sont-ils répartis ? Qui pilote la maintenance et avec quelle stratégie ? Répondre à ces questions permet de construire de bonnes fondations qui sont indispensables pour ensuite grandir, construire et digitaliser rapidement votre usine.
Optimiser la maintenance industrielle grâce à l'Intelligence artificielle et aux données en temps réel
L'implémentation de la maintenance prédictive basée sur l'IA repose principalement sur l'analyse continue des données collectées en temps réel à partir des capteurs IoT intégrés dans les machines. Ces capteurs permettent de surveiller les paramètres clés tels que les vibrations, la température ou encore la pression, pour identifier les anomalies avant qu'une défaillance ne survienne. L'un des principaux avantages de cette approche est la possibilité de prédire les pannes avec une grande précision, réduisant ainsi les temps d'arrêt non planifiés. Par exemple, General Electric a démontré que l'utilisation de l'intelligence artificielle dans la gestion de la maintenance pouvait réduire les coûts de maintenance de 10 à 20 % tout en augmentant la disponibilité des équipements de 5 à 10 %. En adoptant ces technologies, les industriels peuvent non seulement réaliser des économies, mais également optimiser les opérations de maintenance et augmenter la durée de vie des machines.
Utiliser l'intelligence artificielle pour piloter et optimiser votre maintenance industrielle est une stratégie gagnante qui s'intègre dans les modèles d'usine 4.0. La transformation digitale devient ainsi un pilier de réussite afin de réduire les risques, les coûts inutiles, les arrêts de production et les perturbations qui en découlent.
Services et produits associés
IoT Industriel
Quel que soit votre projet, trouvez les produits et solutions pour bâtir l'industrie de demain.
Capteur intelligent
Les capteurs intelligents sont conçus avec des comportements particuliers pour s'adapter aux applications spécialisées.