- Publié le 9 janv. 2023
- Mis à jour le 29 août 2023
- 5 min
Comment automatiser la maintenance industrielle ?
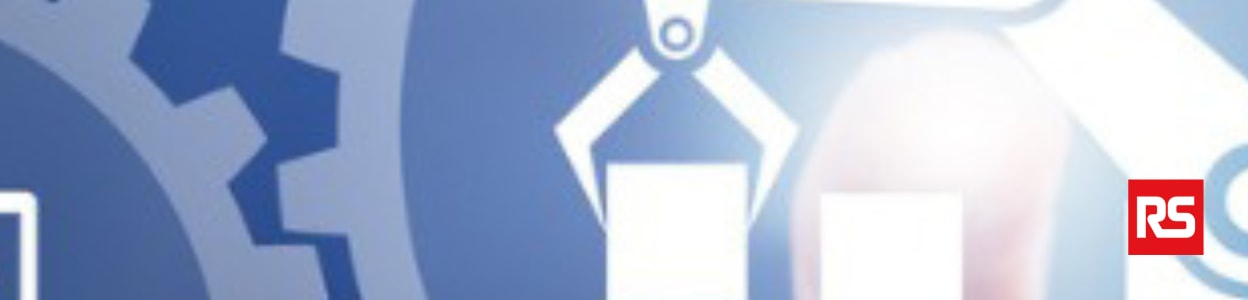
Article publié le 21/07/2021
Maintenance et performance industrielle sont deux notions qui vont de pair. L'une ne peut pas être efficace si l'autre est absente. Maintenance du matériel, des systèmes mécaniques, gestion des équipes de techniciens, arrêt de la production, risques de désorganisation des lignes de production… La maintenance industrielle est aussi quelque chose qui coûte cher et qui impacte durablement les outils de production.
La solution tient alors en un mot : l'automatisation. Une façon de réduire les tâches manuelles chronophages, coûteuses et pas toujours nécessaires, pour confier une partie du travail à l'ordinateur. Ou plutôt à une plateforme digitale pour intervenir uniquement lorsque c'est nécessaire, et avant même que les outils, équipements ou lignes de production ne tombent en panne.
Qu'est-ce que l'automatisation de la maintenance industrielle ?
Une bonne maintenance industrielle est nécessaire pour maximiser le temps de travail de vos équipes et pour maintenir les coûts bas en termes de production. L'automatisation est l'une des grandes tendances du moment. Aux côtés de l'IoT (Internet des Objets), du machine learning, de l'intelligence artificielle et de la gestion des données, l'automatisation a un large impact dans tous les secteurs industriels.
On parle alors de maintenance prédictive pour déterminer l'état d'un équipement afin d'identifier les besoins de maintenance pour en maximiser ses performances. En général, cette prédiction vise à prévenir les pannes, les défaillances ou les arrêts futurs d'un équipement en surveillant en permanence les données relatives aux performances et à l'efficacité. La prédiction se base sur les données collectées et traitées pour anticiper une défaillance éventuelle et pouvoir intervenir juste avant. Une démarche qui fonctionne en trois temps.
Trois grandes étapes pour automatiser la maintenance industrielle
Il ne peut y avoir d'automatisation sans données. Ce sont elles qui permettent de prendre les bonnes décisions au bon moment afin de réaliser des opérations de maintenance en mode « juste à temps ».
Première étape : collecter des données
Si certains équipements modernes disposent déjà de capteurs intégrés, pour d'autres, il sera nécessaire de les intégrer. Ces capteurs permettent de recueillir des données d'utilisation, que ce soit la température, l'humidité, la pression, les vibrations ou le nombre de cycles de fonctionnement. Vous pouvez ainsi mieux comprendre les liens qui existent entre le comportement d'une machine et ses arrêts de production. Avec ces données historiques, ainsi que les données sur les temps d'arrêt ou les taux de défaillance, le processus d'automatisation peut se mettre en place.
On entre ici dans l'ère de l'IoT avec des capteurs qui doivent être connectés ensemble. Parfois, ils doivent être alimentés électriquement et connectés à un réseau à fort débit (Wifi, 4G ou 5G) si les données collectées sont conséquentes et en temps réel. Parfois, un réseau bas débit comme Lora ou Sigfox est plus utile afin de mesurer des données de façon ponctuelle, comme la consommation d'eau, de gaz ou d'électricité d'un équipement par exemple.
Deuxième étape : analyser et faire parler les données collectées
Mesurer des données est une chose, mais il faut aussi savoir les collecter, les sécuriser et les faire parler. Ici, on se base sur l'intelligence artificielle nourrie par le machine learning qui cherche des corrélations et des schémas statistiques dans les données à sa disposition. Plus celles-ci sont nombreuses et pertinentes, plus les résultats seront rapides et cohérents. En général, les industriels utilisent une plateforme de GMAO (Gestion de Maintenance Assistée par Ordinateur) pour réaliser ce travail.
Une fois ces données analysées, il est possible de déterminer une première série d'actions. Si, par exemple, une machine tombe fréquemment en panne lorsque son niveau de lubrifiant ou sa température atteint un certain seuil, la GMAO pourra envoyer une notification au technicien de maintenance juste avant la panne attendue. Pour que le modèle de la maintenance prédictive soit statistiquement fiable, pertinent et utile, il doit se baser sur une grande quantité de données. Au commencement, plutôt que d'attendre plusieurs semaines ou mois, il est d'ailleurs possible d'acheter des jeux de données pour certaines machines. Une manière de gagner du temps dans la mise en place de l'automatisation.
Troisième étape : repenser la gestion de la maintenance
L'automatisation de la maintenance industrielle représente un changement de paradigme pour les industriels. Pour accompagner le changement technologique, il faut aussi accompagner les changements organisationnels et humains qui en découlent. Le succès de l'intégration de la maintenance automatisée dépend toujours de la stratégie mise en œuvre par la direction et de la manière dont elle est déployée au sein des équipes. Équipement informatique, formation, mise à jour des processus, actualisation des méthodes de maintenance… Repenser la gestion de la maintenance est essentiel pour que l'humain accompagne la technologie dans la réussite d'un projet industriel.
Automatiser la maintenance industrielle est aujourd'hui un levier de compétitivité. C'est grâce à elle que des sites de production peuvent se transformer pour devenir plus efficaces, moins coûteux et plus agiles. Une démarche indispensable dans un monde globalisé et incertain où un arrêt de la production peut générer des impacts en cascade.
Services et produits associés
Passerelles IoT
La gamme RS de passerelles IoT offre d'excellentes solutions pour étendre un écosystème IoT ou mettre à niveau un environnement industriel.
Capteur intelligent
La gamme RS Components de capteurs multifonctions permet de prendre le contrôle comme jamais auparavant.
IoT Industriel
Quel que soit votre projet, trouvez les produits et solutions pour bâtir l'industrie de demain.