- Publié le 14 mars 2024
- Mis à jour le 14 mars 2024
- 8 min
Comment maximiser les performances énergétiques de vos machines ?
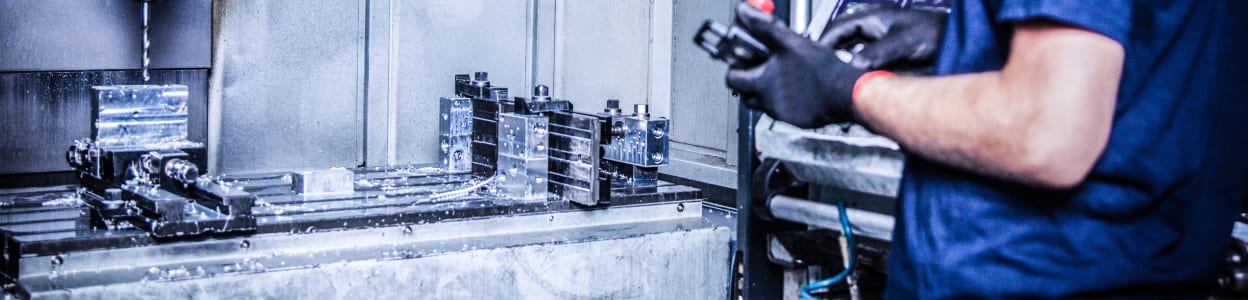
L'optimisation des performances énergétiques des machines et des équipements de production est devenue une priorité pour les entreprises cherchant à réduire leur impact environnemental tout en améliorant leur productivité. Différentes mesures peuvent être prises par les responsables de production et de maintenance afin d’optimiser l'efficacité énergétique de leurs lignes de production.
Fini le temps où agir sur la consommation de son outil de production était un « plus » venant apporter des économies financières et s’ajouter à la performance globale d’une entreprise. Depuis la crise énergétique qu’a subi de plein fouet l’industrie en 2022, avec des prix de l’électricité fleurtant durant l’été le chaud de l’histoire avec 1 000 € du km/h, les entreprises ont dit adieu à l’énergie peu chère et ont dû prendre conscience de « s’armer » pour faire face à la volatilité des coûts.
En premier lieu, si le bâtiment et sa consommation énergétique est en ligne de mire, c’est avant tout sur l’atelier et ses machines que les regards doivent se tourner. En effet, l’exploitation d’une machine demeure le premier poste de dépense d’une usine. D’où l’intérêt d’entamer une démarche d’efficacité énergétique en réalisant un audit – il est conseillé pour cela de s’adresser directement à des spécialistes de la question, à commencer par l’Agence de la transition énergétique (Ademe) de votre région, un fournisseur d’énergie ou bien un cabinet de conseils spécialisé. Un audit aura pour intérêt d’identifier les équipements de production les plus « énergivores ».
La maintenance au cœur de l’optimisation énergétique des machines
Lorsqu'il s'agit de réduire la consommation énergétique des machines de production, les opérations de maintenance jouent un rôle crucial, à commencer par la maintenance préventive, laquelle porte notamment sur le nettoyage et l’entretien réguliers visant à éliminer les saletés, l'accumulation de poussière et autres dépôts pouvant affecter la performance et augmenter la consommation d'énergie. Car l’un des rôles de la maintenance réside dans la chasse aux gaspillages, notamment dans les réseaux fluidiques et gazeux afin de limiter les pertes de charge en ligne ou les pertes de qualité des échanges thermiques. L’objectif est d’éviter toute obstructions, sédimentation, embouage ou empoussièrement.
Le contrôle visuel régulier est également de mise, notamment au niveau des filtres à air et des joints. De la même manière, une lubrification appropriée des composants mobiles est essentielle pour réduire les frottements et minimiser les pertes d'énergie, tout comme la vérification régulière des réglages et des calibrations des machines pour s’assurer de leur fonctionnement optimal. Notons que le sur-graissage ou, à l’inverse, le manque de graisse des roulements, consomment de l’énergie. Une bonne lubrification des réducteurs est aussi une source d’économie d’énergie, mais ce n’est pas tout : bien maîtriser l’alignement et la tension des courroies permet aussi d’optimiser la consommation d’énergie.
Dans le cadre du préventif, le remplacement des pièces usées doit s’effectuer en fonction des recommandations du constructeur mais aussi de l’utilisation de la machine sans oublier l’environnement de l’atelier. Il est également possible d’installer des équipements permettant de gagner en économie d'énergie, à l’exemple des variateurs de vitesse pour une utilisation conforme aux besoins réels et évitant ainsi de surdimensionner les fonctions de la machine… et de trop consommer. La chasse aux fuites figure également comme l’une des tâches de la maintenance pouvant optimiser l’efficacité énergétique de la machine : celles-ci usent en effet prématurément la machine et affectent son rendement… la poussant à consommer davantage.
Du point de vue curatif ou au niveau du retrofit, agir sur les moteurs est tout aussi pertinent. En remplaçant un moteur ancien par un moteur à haut rendement énergétique de type IE5, les économies peuvent vite dépasser 20%. Mais en fonction des process, il s’avère parfois plus intéressant d’intégrer de la variation de vitesse pour des démarrages moins consommateurs et pour travailler à des régimes de vitesses plus basses.
Enfin, n’oublions pas que la sensibilisation et la formation du personnel sont essentielles ; si les salariés sont conscients de l'importance de l'efficacité énergétique et de l'impact de leurs actions sur la consommation d'énergie, l’utilisation des machines a de fortes chances d’être moins énergivore.
Pas de méthode « big-bang », mais agir en priorité sur les machines énergivores
Une fois les machines les plus consommatrices identifiées, une batterie de mesures s’impose. Et de mesure, il en est question puisque c’est précisément elle qui va aider à déterminer avec précision combien mais aussi pourquoi un équipement surconsomme. Ainsi, commencer par « monitorer » la machine à l’aide de capteurs de température mais aussi de vibration, de vitesse, de pression, de chocs et d’ultrasons va offrir une lecture de ses défaillances. En détectant une avarie, il est possible d’intervenir avant une éventuelle panne (c’est le cas ici de la maintenance conditionnelle) tout en évitant que la machine ne consomme plus qu’à l’accoutumée. Les ultrasons s’avèrent aussi très utiles pour détecter et localiser la présence de fuites.
Naturellement, il va sans dire qu’avant même d’intégrer des outils de mesure et de contrôle de la consommation il est essentiel de mener des opérations de maintenance préventive de façon régulière, de remplacer les joints quand il le faut et lubrifier sa machine et graisser les composants à chaque campagne de préventif. Mais la maintenance conditionnelle présente depuis déjà longtemps de sérieux avantages. Celle-ci est aujourd'hui renforcée de la maintenance prévisionnelle (« predictive maintenance » en anglais) qui va quant à elle, grâce à la remontée de données prélevées sur la machine ou sur toute une de production permettre de les analyser et d’en faire de précieuses informations… menant ensuite le responsable maintenance ou de production à prendre les bonnes décisions.
Enfin, mettre en place un logiciel de pilotage de la production en temps réel tel que le Manufacturing Execution System (MES) permet d’une part de remontée les informations du terrain pour améliorer la performance de la machine et, d’autre part, d’aller au-delà du TRS (un indicateur de performance) en surveillant ses éventuelles surconsommations d’énergie depuis sa mise en route et ce jusqu’à sa mise en veille.
Quelques technologies à mettre en place
Parmi les moyens à mettre en œuvre figurent les compteurs d'énergie. Leur rôle ? Mesurer la consommation d'énergie des machines de production de manière précise. Il existe différents types de compteurs, tels que les compteurs d'électricité, de gaz ou d'eau, en fonction des besoins spécifiques. Il existe aussi d’autres capteurs bien connus mesurant la température, la pression et la vitesse. Leur utilisation aide à surveiller et à contrôler les paramètres importants liés à l'efficacité énergétique et à détecter les problèmes potentiels, tels que les surchauffes ou les variations de pression, lesquelles peuvent entraîner une surconsommation d'énergie.
Il existe également des systèmes de monitoring énergétique permettant de collecter et d'analyser en temps réel les données de consommation d'énergie des machines de production. Ces systèmes peuvent inclure des logiciels spécialisés procurant une vision claire de la performance énergétique de chaque machine et donnant le moyen d'identifier les goulots d'étranglement énergétiques et de prendre des mesures correctives rapidement.
Des logiciels de gestion de l'énergie apparaissent sur le marché afin de mieux suivre et analyser les données énergétiques de l’outil de production sur une base régulière. Ces logiciels aident les techniciens à détecter les tendances, à établir des objectifs d'efficacité énergétique et à suivre les progrès réalisés. D’autres logiciels offrent de leur côté des fonctionnalités avancées, telles que la simulation et la modélisation énergétique, pour optimiser les performances énergétiques de la machine. En ce sens, les jumeaux numériques peuvent se révéler très utiles… quant à l’intelligence artificielle (IA), les progrès considérables de cette technologie promettent d’en faire, à court terme, un outil incontournable de l’optimisation énergétique de l’outil de production.