- Publié le 12 déc. 2023
- Mis à jour le 24 janv. 2025
- 18 min
Guide Pratique : réduire le coût de production industrielle - stratégies et solutions pour améliorer votre performance financière
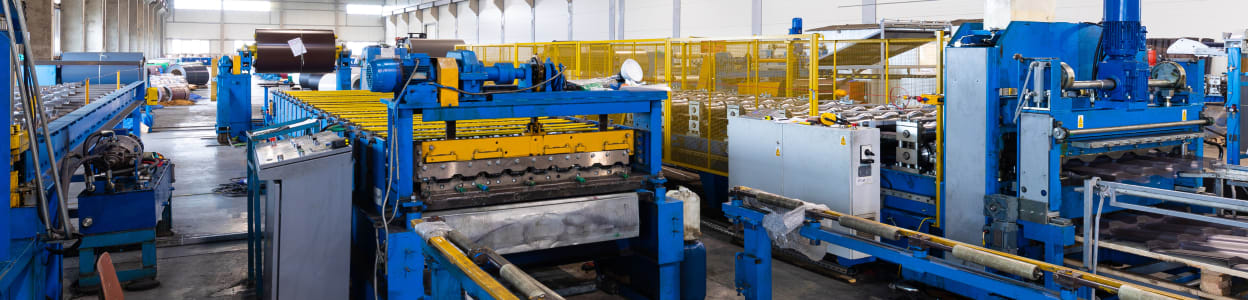
Face à l’urgence climatique et à la volatilité des coûts de l’énergie, mais aussi dans le but de répondre aux objectifs européens de décarbonation, les industriels doivent tout faire pour réduire leur consommation. Cela passe avant tout par celle des machines et des équipements de production. Mais comment ?
Économiser l'énergie dans une usine est nécessaire, et ce pour plusieurs raisons. Nous pourrions évoquer la conscience environnementale et l’urgence climatique mais pour une entreprise, l’objectif est avant tout de réduire les coûts de fonctionnement de l'atelier en minimisant la consommation d'énergie, en particulier depuis l’envolée des coûts de l’énergie en 2022. Mais consommer moins peut également améliorer l'efficacité de l'usine du fait d’une utilisation efficace de l'énergie ; en somme, produire mieux avec moins. Comment ? À la fois en adoptant de nouvelles technologies de surveillance de l’état de santé et de fonctionnement de l’équipement, et en remplaçant certains composants voire une vieille machine par une autre de nouvelle génération... mais pas seulement : établir un diagnostic peut aussi permettre d’utiliser différemment et façon optimisée un moteur ou un compresseur par exemple.
Plusieurs types d’énergie sont concernés, les machines et les outils de production pouvant être alimentés par une grande variété de sources en fonction des besoins spécifiques de chaque entreprise. C’est le cas de l'électricité, l'une des sources d'énergie les plus utilisées dans l'industrie (machines et d'outils, aux équipements de production automatisés, capteurs, écrans...), le gaz naturel (fours, chaudières, turbines...), le pétrole (souvent utilisé comme combustible pour les machines et les équipements nécessitant une grande quantité d'énergie comme les moteurs de navires et les centrales électriques), les biocarburants (produits à partir de matières organiques renouvelables comme les céréales, l'huile de colza, le bois et les déchets agricoles) ou encore l’eau, ressource indispensable pour de nombreux secteurs comme la métallurgie, les cimenteries, la papeterie ou encore le verre et la chimie sans oublier l’agroalimentaire.
Toute l’industrie est concernée par la réduction de la consommation énergétique
Dans l’industrie, la question de la réduction de la consommation d’énergie se pose aujourd’hui partout (c’est le cas d’ailleurs de tous les pans de l’économie). Mais historiquement, plusieurs secteurs d’activité étaient identifiés comme particulièrement énergivores ; ils sont d’ailleurs la cible du Gouvernement qui s’est donné pour mission d’agir localement, site par site. Ces sites appartiennent le plus souvent aux cimenteries, à la sidérurgie, à la chimie et la pétrochimie, au raffinage et au pétrole ou encore à l’industrie du verre et du sucre... des industries qui ont besoin d'une quantité importante d'énergie pour extraire, traiter et transporter les matières premières et pour faire fonctionner les machines et équipements complexes et de grande taille utilisés dans leurs activités.
La sidérurgie représente par exemple une part importante de la consommation d'énergie du secteur industriel, l'énergie étant utilisée pour fondre le minerai de fer et d'autres matériaux afin de fabriquer de l'acier. Il en est de même pour l’industrie du ciment, du verre ou encore du papier. Notons également le cas des futures gigafactories – dont les projets de construction se multiplient et voient le jour dans le pays, en particulier dans les Hauts-de-France ; la production de batteries électriques est fortement consommatrice d’eau. Outre l'industrie lourde, d'autres secteurs industriels tels que l'agriculture, les transports et la construction consomment également des quantités substantielles d'énergie.
Un réglementation de plus en plus exigeante
Au final, en 2021, l'industrie était responsable de 19% de la consommation d'énergie primaire de la France, selon le Commissariat général au développement durable, représentant au passage environ 14% des émissions totales en France, chiffres de l'Ademe à l’appui (dont 60% des émissions de CO2 proviennent de la combustion de combustibles fossiles tels que le charbon, le pétrole et le gaz naturel). Question pollution, cette consommation est responsable en France de plus de 30%.
À ce jour, les industriels ont bien compris l’enjeu de réduire leur consommation d’énergie, en particulier avec l’explosion des coûts intervenue depuis la guerre en Ukraine. Autre raison significative, la tendance réglementaire qui, depuis plusieurs années et plus particulièrement depuis la crise sanitaire, se montre toujours plus exigeante.
En France, la loi sur la Transition énergétique pour la croissance verte adoptée en 2015 oblige les entreprises industrielles à mettre en place des mesures d'économie d'énergie et de réduction des émissions de gaz à effet de serre. Au niveau européen, la directive sur l'efficacité énergétique de 2012 oblige également les États membres à fixer des objectifs contraignants en matière d'efficacité énergétique. Du côté des normes, si celles-ci ne sont qu’incitatives, elles se révèlent être un bon moyen d’atteindre ses objectifs ; c’est le cas notamment par exemple de la norme ISO 50001 qui établit un système de gestion de l'énergie afin d’aider les entreprises à améliorer leur performance énergétique.
Sur quels équipements de production agir ?
En usine, il est nécessaire d’identifier les équipements les plus consommateurs d'énergie. Bien souvent, il s’agit des moteurs électriques lorsqu’ils sont surdimensionnés, mais pas seulement. Les compresseurs d'air chargés d’alimenter les outils et les machines peuvent être très énergivores et nécessitent souvent une surveillance et un entretien réguliers pour minimiser les pertes d'énergie. Il en est de même pour les fours, les séchoirs et autres chaudières, couramment utilisés pour chauffer des matériaux et de l'eau ; ceux-ci utilisent bien souvent des combustibles fossiles. Quant aux équipements de production automatisés tels que les robots, leur consommation peut se révéler excessive lorsqu'ils sont laissés en veille ou lorsqu'ils sont mal réglés et fonctionnant à des niveaux de production inférieurs.
Avant toute chose, il est préférable de mener une campagne d’économie d’énergie dans l’entreprise et de nommer le cas échéant une équipe dédiée. Celle-ci doit prendre en compte l’ensemble des consommations du site, à la fois de l’usine et de l’outil de production, mais également de la partie tertiaire et bâtiment, de la consommation d’électricité (engendrée par exemple par les outils informatiques) et l’éclairage ou encore l’utilisation d’eau sanitaire sans oublier le chauffage et la climatisation (CVC). Elle permet aussi de savoir quelle énergie – comment et combien – est réellement utilisée dans l’entreprise, puis dans l’atelier et enfin sur quelle machine.
Pour ce faire, il semble pertinent d’installer une GTC (gestion technique du bâtiment – GTB – mais dans un ensemble plus vaste, comprenant aussi les dépenses énergétiques de l’atelier de production et de maintenance). En centralisant la gestion des équipements techniques, ce système informatique va dès lors aider à identifier les gaspillages d’énergie, à réguler la température – par exemple – mais également repérer les dysfonctionnements des équipements de l’usine pouvant à leur tour provoquer des surconsommations. Mais attention, ce système peut s’avérer à la fois coûteux et complexe à mettre en place et à exploiter, en particulier dans les sites anciens.
La GTC va surtout permettre d’agir au bon endroit et de prendre des décisions rapides et efficaces, comme le remplacement de pièces sur des moteurs ou des variateurs, l’installation d’un éclairage LED, améliorer l’entretien des machines et replanifier les interventions de maintenance préventive des équipements de production, à l’image des opérations de lubrification, le nettoyage des machines afin d’éviter l’accumulation de saleté, de poussière et tout autre contaminant pouvant affecter leur performance. Il en est de même pour le remplacement des pièces susceptibles de casser prochainement... ce qui nécessite des inspections régulières afin de détecter des problèmes potentiels et les réparer avant qu'elles ne deviennent critiques.
Réduire la consommation de l’outil de production... entre IoT et récupération d’énergie
Concrètement, il est important d’installer un système de surveillance et d’acquisition de données. Cela passe par l’intégration sur les équipements de compteurs d'énergie, de capteurs de température et d'humidité, le tout relié à un système de surveillance en temps réel, focalisé sur chaque équipement. En cela, l'automatisation des processus de production peut également contribuer à réduire la consommation d'énergie en minimisant les pertes liées aux processus manuels et en optimisant les temps d'utilisation des machines. Enfin, former et sensibiliser le personnel de production semblent incontournables.
Parmi les technologies récentes, les IoT (Internet des Objets) se révèlent à leur tour précieux pour réduire la consommation énergétique. C’est le cas notamment des compteurs intelligents, lesquels collectent des données en temps réel sur la consommation d'énergie, les systèmes de gestion énergétique, sortes de plateformes IoT chargées de collecter, de traiter et d'analyser des données sur la consommation énergétique d'un bâtiment et d'optimiser la gestion de l'énergie en temps réel. Les capteurs de pression, d’humidité, d’air et de température, qui vont aider à mieux gérer la consommation d'énergie et réduire les gaspillages, offrir une meilleure visibilité à travers la collecte des données en temps réel et apporter plus de flexibilité en matière de programmation et de contrôle des équipements. Néanmoins, l'installation et la configuration des IoT peuvent être complexes et nécessiter des compétences techniques avancées... et tout autant au niveau de leur mise en œuvre et de leur entretien. Aussi se pose la question des risques en matière de cybersécurité et de confidentialité des données collectées.
Autres solutions pouvant être mises en place : les systèmes de récupération d’énergie, à l’image de la récupération puis la réutilisation de la chaleur générée par les processus de production afin de chauffer d'autres zones de l'usine ou alimenter des systèmes de ventilation ou de climatisation. De même, certains processus de production génèrent de l'énergie mécanique sous forme de vibrations ou de mouvements... une énergie pouvant être à son tour récupérée et utilisée pour alimenter d'autres équipements. Il est possible d’installer des systèmes de récupération d'énergie sur des équipements tels que les compresseurs d'air ou les machines de traitement de l'eau. Il convient enfin de mentionner l'utilisation de panneaux solaires ou de turbines éoliennes...attention toutefois à la complexité de mise en œuvre et d’exploitation, mais aussi aux seuils de rentabilité pas toujours évident à atteindre.
Stratégies avancées pour l'optimisation énergétique industrielle
La réduction de la consommation énergétique dans l'industrie nécessite une approche holistique qui va au-delà des solutions techniques traditionnelles. L'implication des collaborateurs et la mise en place d'une véritable culture de sobriété énergétique sont devenues des leviers essentiels pour atteindre les objectifs de performance.
Engagement collectif et formation pour réduire sa consommation
Les entreprises industrielles qui réussissent le mieux leur transition énergétique sont celles qui impliquent activement leurs équipes. La sensibilisation et la formation des collaborateurs aux bonnes pratiques énergétiques peuvent générer des économies significatives, pouvant aller jusqu'à 15% de réduction sur la facture globale d'énergie
Solutions intelligentes de monitoring
L'utilisation de plateformes IoT dédiées à l'optimisation énergétique permet désormais une gestion ultra-précise des consommations. Ces systèmes, couplés à l'intelligence artificielle, peuvent identifier automatiquement les pics de consommation et ajuster en temps réel les paramètres de production pour une meilleure efficacité énergétique.
Récupération thermique avancée
Les technologies de récupération de chaleur fatale connaissent des avancées majeures. Les systèmes nouvelle génération permettent de valoriser jusqu'à 60% de l'énergie thermique habituellement perdue dans les processus industriels, créant ainsi une source d'énergie secondaire précieuse pour l'entreprise.
Démarche d'amélioration continue dans l'efficacité énergétique
La mise en place d'un guide de vérification énergétique permet d'établir un diagnostic régulier des performances. Cette approche structurée aide à identifier rapidement les dérives de consommation et à mettre en œuvre des actions correctives ciblées. Les entreprises qui adoptent cette méthodologie constatent en moyenne une réduction de 20% de leur consommation énergétique sur trois ans.
Optimisation des processus de production
L'analyse détaillée des cycles de production permet d'identifier les opportunités d'optimisation énergétique. La réorganisation des séquences de fabrication, l'ajustement des temps de fonctionnement des équipements et la synchronisation des phases de production peuvent générer des économies substantielles sans investissement majeur
Stratégie globale de réduction des coûts : optimiser la chaîne de production
Pour mettre en place une stratégie efficace de réduction des coûts, il est essentiel d'avoir une vision globale des flux physiques et d'informations qui circulent dans votre entreprise. L'analyse détaillée de la chaîne de production permet d'identifier les gaspillages et les irrégularités qui impactent directement les coûts de production. Les gestionnaires doivent passer en revue chacune des étapes du processus de fabrication pour détecter les dépenses inutiles et les opportunités d'optimisation. Cette approche systématique permet non seulement de réduire les coûts mais aussi d'améliorer la qualité des produits et services.
Optimisation des approvisionnements et gestion intelligente des stocks
La maîtrise des coûts liés aux matières premières commence par une gestion rigoureuse des approvisionnements. Une mauvaise gestion des stocks peut rapidement générer des frais généraux considérables. Il est important de comparer les différents fournisseurs et de négocier avec eux pour obtenir les meilleures conditions. L'adoption d'une stratégie qui consiste à attendre la commande du client avant de lancer la production permet de réduire considérablement les coûts de stockage. Les entreprises les plus performantes automatisent les tâches liées à la gestion des stocks grâce à des systèmes d'information intégrés.
Rentabiliser les équipements de production existants
Pour rendre la production plus rentable, il est crucial d'optimiser l'utilisation des équipements existants. Les coûts énergétiques comprennent les sources de dépenses les plus importantes pour de nombreuses entreprises industrielles. Une analyse approfondie de l'utilisation des machines, comme les chariots et les laminoirs, permet de réduire les coûts associés à leur fonctionnement. Les fabricants peuvent réaliser des économies significatives en améliorant l'efficacité des processus de production et en minimisant les temps d'arrêt des équipements.
Digitalisation des processus et gestion des données de production
La transformation numérique des processus de production constitue un levier majeur pour réduire les coûts de production. L'intégration des outils digitaux permet d'obtenir une vision globale des flux physiques et d'informations qui circulent dans l'entreprise. Les systèmes MES (Manufacturing Execution System) et ERP (Enterprise Resource Planning) offrent une traçabilité complète des opérations, permettant d'identifier rapidement les sources de gaspillage et les opportunités d'optimisation. Les entreprises peuvent ainsi détecter les anomalies en temps réel, ajuster leur production en fonction de la demande réelle et minimiser les stocks tampons coûteux.
Amélioration continue des processus de fabrication
La mise en place d'une démarche d'amélioration continue s'avère essentielle pour maintenir une réduction durable des coûts de production. Cette approche systématique implique l'analyse régulière des différents processus de fabrication pour identifier les points d'amélioration potentiels. Les gestionnaires doivent encourager les équipes opérationnelles à partager leurs observations et suggestions, car ce sont souvent les opérateurs qui détectent les premiers les inefficacités dans la chaîne de production. Les gains peuvent sembler modestes individuellement, mais leur accumulation génère des économies significatives sur le long terme.
Formation et implication des ressources humaines
L'optimisation des coûts de production passe nécessairement par une gestion efficace des ressources humaines. Une formation continue des équipes aux bonnes pratiques de production et aux nouvelles technologies permet de réduire les erreurs de manipulation, les rebuts et les temps d'arrêt machine. L'implication du personnel dans la démarche de réduction des coûts crée une dynamique positive où chaque collaborateur devient acteur de l'amélioration de la performance. Les entreprises qui investissent dans le développement des compétences de leurs équipes constatent généralement une amélioration significative de la qualité des produits et une réduction des coûts associés aux non-conformités.
Partenariats stratégiques avec les fournisseurs
La construction de relations durables avec les fournisseurs représente un axe majeur dans la stratégie de réduction des coûts. Au-delà de la simple négociation des prix, il est important de développer des partenariats qui permettent d'optimiser l'ensemble de la chaîne d'approvisionnement. Les accords de long terme peuvent inclure des programmes d'amélioration conjointe de la qualité des matières premières, des solutions logistiques innovantes ou encore des plans de développement communs. Cette approche collaborative permet non seulement de réduire les coûts directs d'achat, mais aussi d'améliorer la fiabilité des approvisionnements et de diminuer les coûts cachés liés aux ruptures ou aux non-conformités.
Cette approche globale de la réduction des coûts de production nécessite un engagement fort de la direction et une vision claire des objectifs à atteindre. La combinaison de ces différentes stratégies permet aux entreprises industrielles de construire un avantage compétitif durable tout en maintenant, voire en améliorant, la qualité de leurs produits et services.
Adopter des bonnes pratiques en optimisant les processus de fabrication
Améliorer l’exploitation du parc existant, c’est finalement la première des choses à faire, et cela coûte moins cher, car optimiser le processus industriel permet de fait de réduire la consommation d'énergie et de réaliser des économies immédiates. Pour ce faire, il est conseillé d’analyser le processus afin de comprendre comment celui-ci fonctionne et d’identifier les zones les plus énergivores.
Ainsi, on peut s’apercevoir que certaines machines et équipements perdent de l'énergie sous forme de chaleur ou de vibrations. Faire de la maintenance conditionnelle à partir de capteurs de température, d’humidité, de vibrations ou autres technologies comme l’usage de caméras thermiques à infrarouge ou de solutions par ultrasons, permet de déterminer avec plus ou moins de précision là où se situent les pics de chaleurs et points d’échauffement, les vibrations (révélatrices de défaillances) ainsi que les fuites d’eau et de gaz.
Concernant les moteurs, remplacer ses équipements vieillissants par des moteurs IE5 (et demain IE6) peut s’avérer coûteux ; analyser avec un spécialiste l’exploitation quotidienne de ses installations revient à identifier si celles-ci sont utilisées de façon optimale (cas de surdimensionnement, trop d’opérations marche-arrêt, phase de démarrage-freinage mal adaptées etc.). Il est également possible de faire du retrofit sur des moteurs anciens en remplaçant les systèmes classiques comme le courroies poulies ou les réducteurs par des variateurs de vitesse. En jouant aussi sur l’utilisation du moteur reposant sur une organisation repensée du process, il est possible de limiter les phases de marche-arrêt et gagner rapidement 30 à 80% d’énergie ! Ça donne à réfléchir...