- Publié le 10 janv. 2023
- Mis à jour le 29 août 2023
- 7 min
Comment se protéger de l'outil de production ?
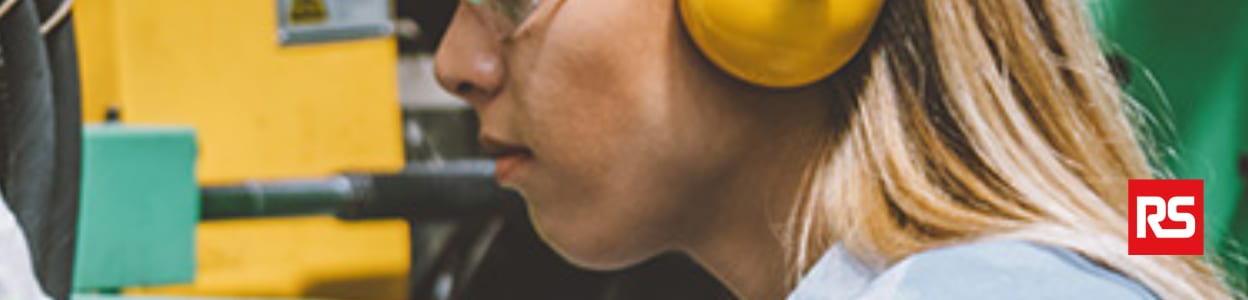
Article publié le 12/05/2022
Travailler au côté des machines et des installations automatisées n’est jamais sans danger. Une minute d’inattention, un non-respect des règles de sécurité, une maintenance mal réalisée ou encore une mauvaise évaluation des risques à la conception… et l’accident peut vite arriver ! Les situations dangereuses auxquelles sont parfois exposés les travailleurs peuvent être évitées. Comment ? Avec quels moyens de protection ? Zoom sur les bonnes pratiques à opérer pour assurer la sécurité des hommes et des machines.
Bilan des accidents du travail liés à la sécurité des machines
Depuis l’instauration de la première « Directive machines », amendée à plusieurs reprises, les règles de sécurité et de maintenance n’ont cessé d’être améliorées ! Les fabricants sont ainsi tenus d’évaluer le facteur de risques dès la phase de conception pour le limiter, voire le supprimer lorsque cela est possible. Malgré ces efforts de prévention et de protection, quelle est la tendance observée ?
Un taux d’accidents élevé malgré une sécurité des machines accrue
Comme les chiffres de l’Assurance maladie – Risques professionnels (Cnam-TS) le prouvent : le nombre d’accidents du travail associé à l’usage de machines dangereuses est important (1) :
- En 2016, 55 044 accidents du travail ont été causés par l’utilisation d’une machine. Cela représente de 10 à 14 % de l’ensemble des accidents de travail, tous secteurs confondus ;
- Dans 1/5e des cas, les blessures engendrent des troubles musculosquelettiques, souvent liés à une mauvaise posture ou à des efforts répétitifs intenses. La seconde cause de blessures est le contact du travailleur avec un élément coupant de la machine (lame, arêtes vives, etc.) ;
- Environ ¼ des accidents de travail sont provoqués par des machines industrielles (métallurgie, plasturgie, industrie du bois ou du papier, etc.) ;
- 15 % des accidents de travail sont générés par l’utilisation de machines portables motorisées, 10 % par des machines de manutention et de levage, 7 % par des machines pour le travail des métaux, et 4 % par des machines pour le travail du bois ou par des scies ;
- Plus de 3 millions de jours d’arrêts de travail sont comptabilisés chaque année à la suite d’un sinistre avec une machine.
Explications sur les principaux risques encourus
Bon nombre d’industries sont encore équipées de machines de production anciennes. Ce constat est doublement problématique ! D’une part, ces équipements ont échappé aux nouvelles règles de conception, imposées par la Directive machine. D’autre part, plus une machine vieillit, plus le risque de pannes et d’accidents augmente.
Dès la phase de conception, le fabricant doit réaliser une prévention des risques visant à supprimer ou à limiter les situations dangereuses. Les facteurs de risques peuvent être regroupés en 8 catégories (2).
- Le risque mécanique : écrasement, cisaillement, coupure, choc, chute, etc.
- Le risque électrique : électrisation avec un équipement sous tension ou une masse conductrice.
- Le risque thermique : machine produisant de la chaleur ou présentant un risque d’explosion.
- Le risque par les vibrations : cas d’une machine portative ou de la conduite d’un engin de chantier.
- Le risque par rayonnements : lié à des émissions d’ondes (à basse fréquence, infrarouges, lasers, etc.).
- Le risque lié aux bruits : une exposition quotidienne et prolongée à un bruit de plus de 80 décibels met en danger l’ouïe du travailleur (3).
- Le risque engendré par des matériaux ou des produits dangereux (matières dangereuses, infectieuses ou inflammables).
- Le risque par le non-respect des principes ergonomiques : mauvaise posture, défaut d’éclairage, accès difficile à l’espace de travail, etc.
Quels sont les organes les plus dangereux d’une machine ?
Comme évoqué précédemment, l’accident avec une machine peut avoir différentes causes. Néanmoins, il s’avère que les risques mécaniques avec des éléments mobiles non protégés (raboteuse, scie portative, etc.) ou avec des éléments en mouvement (courroie, levier, vis sans fin, etc.) sont source d’accidents graves. En effet, avec ce type d’équipements, les blessures sont parfois irréversibles (doigts écrasés, membres sectionnées, décès, etc.).
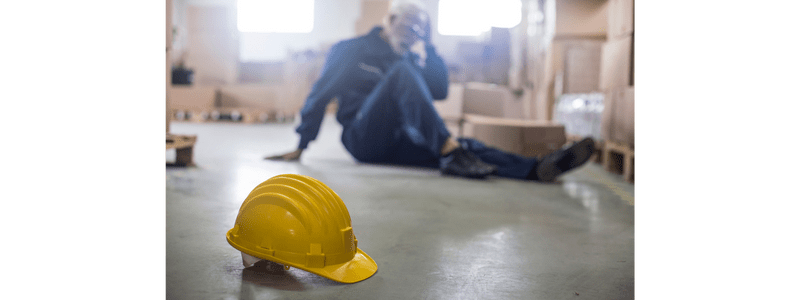
Les moyens techniques pour accroître la sécurité des machines
Lors de la conception, chaque fabricant prévoit désormais un système de commande capable d’optimiser la sécurité de ses machines. Ce système assure à la fois les fonctions de base et les interactions avec les dispositifs de protection. En cas de danger, le système de commande provoque l’arrêt immédiat de l’équipement ou de la fonction dangereuse de l’appareil.
Le tableau ci-après vous présente des exemples de systèmes de sécurité.
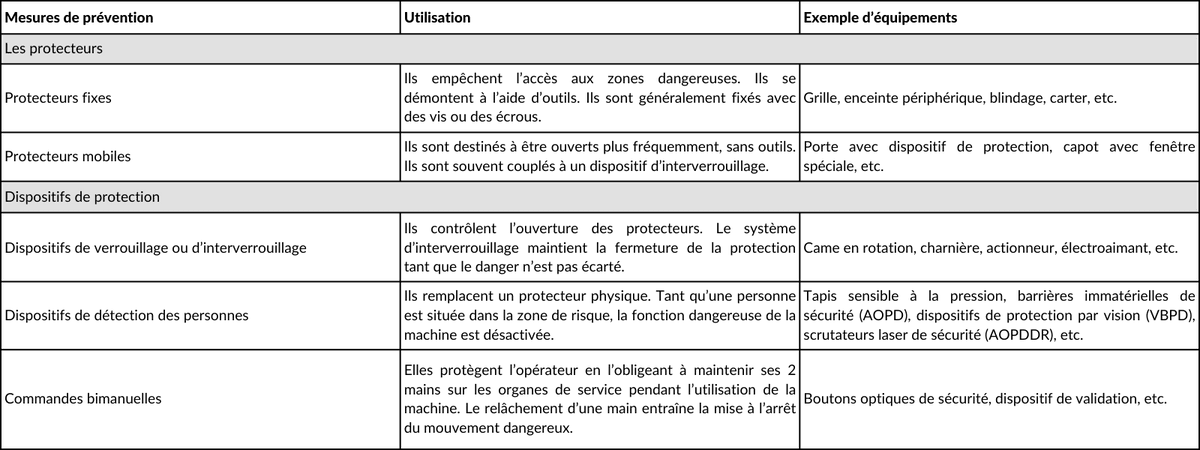
D’autre part, l’employeur doit :
- Veiller à la bonne utilisation des équipements et aux bonnes conditions de travail de ses employés ;
- Former son personnel sur les règles de sécurité à respecter ;
- Assurer la maintenance des machines ;
- Mettre en place de mesures de sécurité complémentaires si nécessaire (dispositifs d’alerte, arrêt d’urgence, équipements de protection collective ou individuelle, etc.).
Sécurité des machines : réglementations et normes
La protection de la santé des travailleurs, notamment des opérateurs et agents de maintenance, est au cœur des préoccupations de l’Union européenne. La sécurité des machines est donc encadrée par un grand nombre de directives et de normes dont les règles sont harmonisées pour l’ensemble des États membres de l’UE.
Les réglementations
En France, les dispositions des directives européennes ont été** transposées dans le Code du travail**. Ainsi, les règles techniques de conception de la Directive machines (2006/42/CE) sont traduites dans par le Décret n° 2008-1156 du 7 novembre 2008. Par ailleurs, il est à noter que le « marquage CE » des machines est obligatoire. Il certifie la conformité des équipements aux règles techniques de sécurité applicables.
Les autres transpositions des directives européennes (3) :
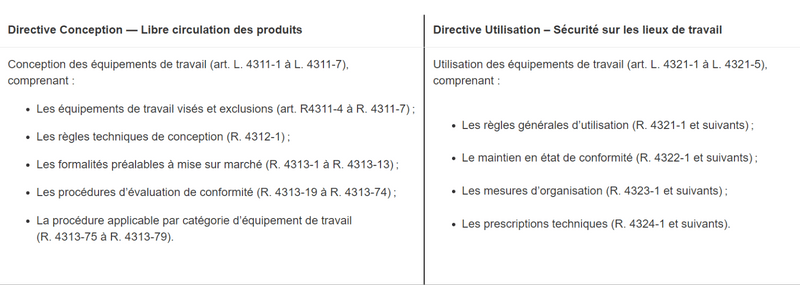
Les normes
En plus des réglementations en vigueur, de nombreuses normes garantissent la sécurité des travailleurs et des machines (4) :
- Norme ISO 12100 : Sécurité des machines — Principes généraux de conception —Appréciation du risque et réduction du risque ;
- Norme ISO 13849 (parties 1 et 2) : Sécurité des machines — Parties des systèmes de commande relatives à la sécurité — Principes généraux de conception et validation ;
- Norme ISO 13851 : Sécurité des machines — Dispositifs de commande bimanuelle —Principes de conception et de choix ;
- Norme ISO 13856 (parties 1, 2 et 3) : Sécurité des machines — Dispositifs de protection sensibles à la pression (tapis, barres, pare-chocs, etc.) ;
- Norme ISO 14119 : Sécurité des machines — Dispositifs de verrouillage associés à des protecteurs - Principes de conception et de choix ;
- Norme ISO 14120 : Sécurité des machines — Protecteurs — Prescriptions générales pour la conception et la construction des protecteurs fixes et mobiles ;
- Norme ISO/TR 22 053 : Sécurité des machines — Système de protection complémentaire, etc.
(1) Source : Hygiène et sécurité du travail n° 259 — juin 2020/Cnam-TS. (2) Source : CNESST (Commission des normes, de l’équité, de la santé et de la sécurité du travail du Québec). (3) Source : INRS (Institut national de recherche et de sécurité). (4) Source : ISO (Organisation internationale de normalisation).
Produits associés
Barrières immatérielles de sécurité
Ces dispositifs optoélectroniques sont utilisés pour détecter les personnes présentes à proximité de machines mobiles.
Interrupteurs de position de sécurité
Mesures de protection conçues pour améliorer la sécurité dans les situations où des portes sont utilisées à proximité d'équipement
Relais de sécurité
Dispositif de surveillance des erreurs ou défaillances potentielles dans les machines ou les usines
Module de sécurité
Dispositifs à usage spécial conçus pour fournir un contrôle critique et une sécurité pendant les situations de processus dangereuses.