- Publié le 17 déc. 2024
- Mis à jour le 17 déc. 2024
- 6 min
Réduire les temps d'arrêt de production grâce à une maintenance proactive des SKID
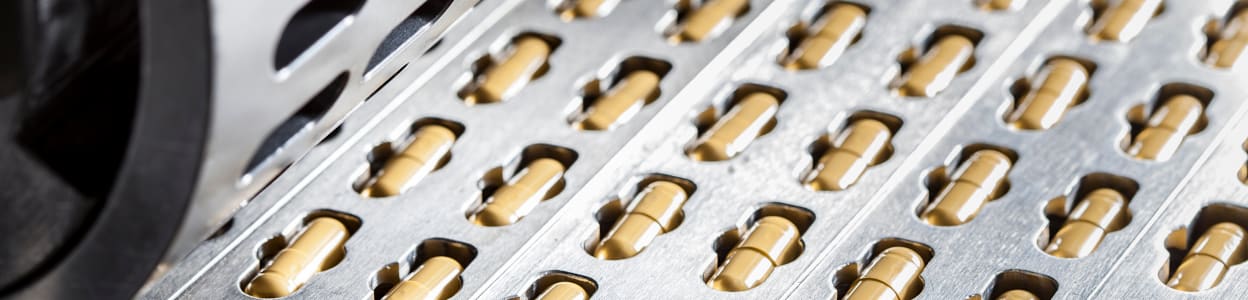
Planifiés ou non, les temps d’arrêt engendrent des coûts directs et indirects considérables aux entreprises faisant appel aux SKID. La maintenance proactive, couplée aux technologies IoT et à une gestion optimisée des stocks favorise la réduction du temps d’arrêt de ces systèmes de production. De la surveillance prédictive, à la formation des équipes, focus sur les différentes stratégies pour maximiser la disponibilité de ces équipements de pointe.
L'impact des temps d'arrêt : enjeux et répercussions sur la production
Un arrêt imprévu d’un SKID, et c’est toute la chaîne de production qui en subit les répercussions. Au-delà des pertes directes, ces interruptions non planifiées déstabilisent l'ensemble du processus et peuvent générer des coûts cachés substantiels.
L’impact financier se mesure à plusieurs niveaux. Les pertes directes, liées à l'interruption de production, peuvent représenter entre 5 et 20 % du chiffre d'affaires annuel selon la criticité du SKID concerné. À ces montants, s'ajoutent les coûts indirects : mobilisation des équipes techniques, risques qualité potentiels, reprogrammation des cycles de production. Une étude récente évalue ces pertes additionnelles à 2,5 fois le coût de l'arrêt initial.
Sur la chaîne d'approvisionnement, les conséquences s'avèrent tout aussi significatives. Les retards de livraison entraînent des pénalités contractuelles, tandis que la désorganisation des plannings de production complexifie la gestion des stocks. Les arrêts imprévus perturbent également les approvisionnements en matières premières, créant un effet domino sur l'ensemble du processus manufacturier.
Un arrêt non planifié de 4 heures engendre en moyenne 18 heures de perturbations sur l'ensemble de la chaîne de production.
Le calcul précis du coût d'un arrêt intègre de multiples facteurs :
- Perte de production horaire (15 000 à 50 000 € selon les installations)
- Coûts de la main-d'œuvre (techniciens, opérateurs, qualité)
- Impact sur les équipements connexes
- Gestion des produits en cours de fabrication
- Requalification des installations
Bon à savoir : les interruptions non planifiées représentent entre 3 et 7 % du temps de production total. Une maintenance proactive permet de réduire ce taux à moins de 2 %
La performance globale des installations dépend ainsi directement de la maîtrise des temps d'arrêt. Les systèmes modernes de monitoring, couplés à une stratégie de maintenance adaptée, transforment ces interruptions subies en opérations maîtrisées.
Méthodologie de maintenance proactive : au-delà de la prévention classique
La maintenance proactive des SKID pharmaceutiques marque une rupture avec les approches préventives traditionnelles. Cette méthodologie innovante s'appuie sur l'analyse prédictive des données et l'anticipation des défaillances potentielles, dépassant ainsi le simple respect des échéanciers d'intervention planifiés.
À la différence de la maintenance préventive classique, basée sur des intervalles fixes, l'approche proactive ajuste ses interventions de façon dynamique. Les algorithmes d'intelligence artificielle analysent en continu les paramètres de fonctionnement pour détecter les prémices de certains dysfonctionnements.
Le monitoring en temps réel s'articule autour de points de contrôle stratégiques :
- Analyse vibratoire des pompes et moteurs
- Surveillance thermographique des composants critiques
- Contrôle des paramètres électriques
- Mesure des débits et pressions différentielles
- Analyse des cycles de fonctionnement
Les technologies IoT industrielles enrichissent cette surveillance [2]. Des capteurs connectés, installés sur les points névralgiques du SKID, transmettent en continu leurs données vers des plateformes d'analyse. Ces systèmes intelligents établissent des corrélations entre les différents paramètres et génèrent des alertes précoces.
Bon à savoir : l'intégration de capteurs IoT permet d'identifier jusqu'à 85 % des anomalies potentielles, huit semaines avant leur manifestation critique.
L'infrastructure digitale déployée autour des SKID s'accompagne d'outils d'aide à la décision sophistiqués. Cette visibilité accrue permet aux équipes techniques d'orchestrer leurs interventions avec précision, limitant ainsi les temps d'arrêt aux seules opérations strictement nécessaires.
[2] Source : https://fr.rs-online.com/web/content/blog-discovery/maintenance/optimiser-maintenance-predictive-iot
Planification et compétences : les clés d'une maintenance optimale
Une planification méticuleuse des interventions s’avère être une stratégie de maintenance proactive, efficace. Cette orchestration complexe harmonise les impératifs de production avec les exigences de maintenance, tout en garantissant la disponibilité des ressources techniques qualifiées.
La synchronisation avec les cycles de production constitue la base de cette optimisation. L'analyse des données historiques permet d'identifier les fenêtres d'intervention idéales. Les opérations de maintenance s'intègrent ainsi naturellement dans le flux de production, minimisant leur impact sur la productivité globale des installations. Une synchronisation optimale des interventions réduit, par ailleurs, de 40 % la durée des arrêts planifiés.
La planification s'articule autour de critères stratégiques :
- Criticité des équipements
- Historique des interventions précédentes
- Disponibilité des pièces de rechange
- Charge de travail des équipes techniques
- Contraintes réglementaires GMP
Les logiciels de GMAO nouvelle génération facilitent également cette mise en place. Dotés d'algorithmes d'optimisation, ils proposent des scénarios de planification tenant compte de l'ensemble des contraintes opérationnelles.
La formation des équipes techniques est, elle aussi, un facteur clé de succès. Au-delà des compétences techniques traditionnelles, les techniciens maîtrisent désormais les outils digitaux de diagnostic et de maintenance. Cette montée en compétences s'organise autour de modules spécialisés, tels que :
- L’utilisation des plateformes de monitoring
- L’interprétation des données prédictives
- La gestion des interventions en environnement GMP
- La maîtrise des procédures d'urgence
- La documentation réglementaire des interventions
Cette approche structurée de la formation, couplée à une planification rigoureuse, garantit l'efficacité maximale des opérations de maintenance, tout en préservant la conformité des installations.
Stratégie d'approvisionnement : sécuriser la disponibilité des pièces critiques
La performance d'une maintenance proactive dépend directement de la disponibilité des pièces de rechange. Une stratégie d'approvisionnement rigoureuse, associée à une gestion optimisée des stocks, garantit la réactivité des interventions tout en maîtrisant les coûts.
La gestion des stocks critiques s'appuie sur une analyse précise des composants stratégiques. Cette cartographie identifie les éléments prioritaires selon plusieurs critères :
- Criticité pour le fonctionnement du SKID
- Délais d'approvisionnement
- Taux de rotation
- Durée de vie moyenne
- Contraintes de stockage
💡 Bon à savoir : la digitalisation de la gestion des stocks réduit de 30 % les ruptures d'approvisionnement sur les composants critiques
Le choix d'un partenaire fiable pour l'approvisionnement des pièces détachées s'avère déterminant. Les distributeurs spécialisés, à l'image de RS, proposent un accompagnement technique complet : disponibilité des composants certifiés, traçabilité des lots, documentation réglementaire et support technique. Cette collaboration étroite optimise la chaîne d'approvisionnement tout en garantissant la conformité des pièces aux exigences pharmaceutiques.