- Publié le 17 déc. 2024
- Mis à jour le 17 déc. 2024
- 10 min
Comment déterminer le besoin de remplacer une pièce mécanique en urgence ?
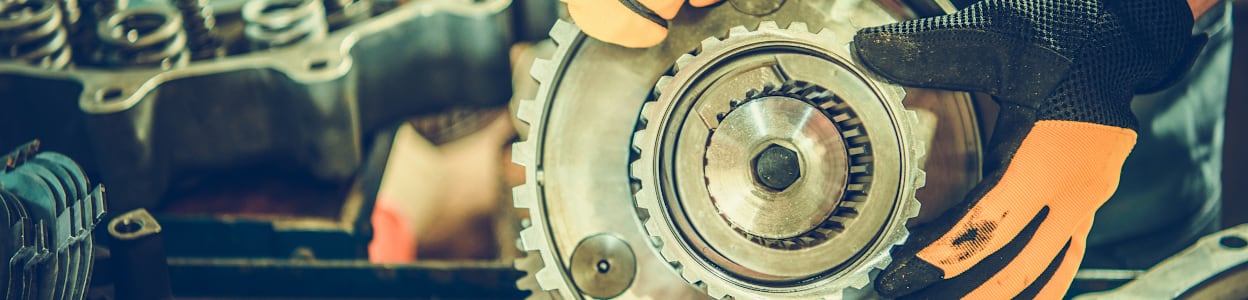
Dans l’industrie, la maintenance des équipements joue un rôle déterminant pour garantir la continuité des opérations et éviter des coûts élevés liés aux pannes. L’usure des roulements, les défaillances des engrenages ou encore les ruptures de vérins hydrauliques peuvent entraîner des arrêts prolongés et coûteux s’ils ne sont pas anticipés. Pourtant, identifier le moment exact où une pièce mécanique doit être remplacée reste un défi, car il faut intervenir ni trop tard (pour éviter des arrêts de production), ni trop tôt (pour éviter le remplacement de pièces encore opérationnelles). Pour cela, les industriels doivent connaître non seulement les pannes mécaniques les plus fréquentes, mais aussi les méthodes pour contrôler l’usure des pièces. Aujourd’hui, les systèmes de surveillance connectés révolutionnent la maintenance industrielle en optimisant la gestion des équipements.
Les pannes mécaniques les plus courantes sur les machines de production
Dans l’industrie, les pannes mécaniques représentent l’un des principaux obstacles à la productivité. Bien que les équipements modernes soient conçus pour durer, certaines pièces restent particulièrement vulnérables à l’usure ou à des conditions d’utilisation exigeantes. Comprendre les causes, mesurer les conséquences et connaître les moyens d’éviter ces pannes est essentiel pour mettre en place une maintenance efficace.
Les ruptures de roulements à billes
Les roulements à billes sont omniprésents dans les machines de production et soumis à des charges importantes. Les ruptures de roulement sont principalement causées par :
- une lubrification insuffisante ou inadéquate ;
- la contamination par des particules (poussière, copeaux métalliques…) ;
- des charges excessives ou mal réparties.
Une rupture de roulement peut entraîner la dégradation des axes et des paliers, provoquant des vibrations importantes, une surchauffe et des arrêts soudains de la machine. Pour éviter ces pannes, mettez en place une surveillance régulière avec des capteurs de vibrations pour détecter des anomalies et des inspections périodiques. Les lubrifiants doivent aussi être correctement appliqués et adaptés aux conditions d’utilisation, en systématisant le nettoyage des environnements de travail.
L’usure des engrenages
Les engrenages transmettent la puissance dans les machines et leur usure peut entraîner des conséquences comme des bruits inhabituels, une perte d’efficacité et des dommages sur les transmissions.
- L’usure des engrenages est généralement causée par :
- un mauvais alignement des composants ;
- une charge excessive, dépassant les tolérances prévues ;
- un défaut de lubrification ou l’utilisation de lubrifiants inappropriés.
Pour prévenir ce type de pannes, les opérateurs de maintenance doivent veiller à conserver un alignement précis lors de l’installation et après les interventions. Des contrôles dimensionnels réguliers permettent par ailleurs de vérifier l’état des dents.
Les ruptures de courroies ou de chaînes
Ces composants jouent également un rôle dans la transmission de puissance. Une courroie rompue arrête immédiatement le fonctionnement de la machine, tandis qu’une chaîne défaillante peut endommager d’autres pièces comme les pignons. Les ruptures trouvent leur origine dans le vieillissement naturel des matériaux, une tension excessive ou au contraire insuffisante et la contamination par des huiles, poussières ou débris.
Pour y remédier, il faut procéder à des inspections visuelles fréquentes pour détecter les fissures ou l’usure et ajuster la tension selon les recommandations du fabricant. L’utilisation de matériaux de haute qualité résistant aux conditions spécifiques est aussi recommandée.
La défaillance des vérins hydrauliques ou pneumatiques
Ces éléments essentiels assurent le mouvement des composants dans de nombreuses machines. Des vérins défaillants entraînent perte de puissance et mouvements irréguliers, voire un blocage complet de la machine. En cause, des fuites de fluide hydraulique ou d’air comprimé, de la corrosion interne ou externe des cylindres et des joints endommagés ou usés.
Là encore, en prévention, les opérateurs doivent inspecter les joints et les remplacer préventivement s’ils sont dégradés. Les fluides doivent aussi être régulièrement contrôlés et notamment l’absence de contamination. Enfin, le nettoyage des surfaces exposées évite la corrosion.
La rupture de pièces structurelles
Les composants structurels sont les supports de machines, les lignes de production ou les cadres qui subissent eux aussi des contraintes élevées dans l’industrie. S’ils cassent, les équipements sont immobilisés pendant de longues périodes et les réparations sont parfois coûteuses. La rupture de ces pièces structurelles est généralement due à :
- l’usure des matériaux générée par des charges répétées ;
- une conception inadéquate de l’aménagement ;
- la faiblesse des matériaux choisis ;
- des surcharges exceptionnelles ou des chocs imprévus.
Pour y remédier, on peut procéder à des contrôles réguliers à l’aide de techniques non destructives (radiographie, ultrasons…). Il faut aussi bien étudier la conception en analysant les contraintes appliquées sur les structures afin d’utiliser des matériaux robustes et adaptés.
Quelles sont les méthodes de contrôle de l'usure des pièces mécaniques ?
L’identification des signes d’usure avant qu’ils ne provoquent des défaillances coûteuses ou dangereuses reste le meilleur moyen de prévenir les pannes. Pour cela, différentes méthodes permettent d’évaluer l’état des pièces mécaniques pour intervenir à temps. Elles s’appuient sur des outils et techniques adaptés aux caractéristiques des machines et aux types de composants à surveiller.
Les inspections visuelles
La méthode la plus directe consiste à examiner visuellement les pièces à la recherche de signes d’usure ou de dommages visibles (fissures, déformations, traces de frottement...). Cette méthode a l’avantage d’être facile à mettre en œuvre et peu coûteuse pour faire des vérifications rapides lors des opérations de maintenance de routine. En revanche, l’inspection visuelle ne détecte pas toujours les anomalies internes ou microscopiques.
Des outils comme les lampes UV ou les loupes à haute précision peuvent améliorer la qualité des inspections visuelles, notamment pour les matériaux sensibles aux microfissures.
Les mesures dimensionnelles
Le contrôle des dimensions des pièces consiste à vérifier leur conformité après une certaine période d’utilisation. On utilise des instruments comme les micromètres, les calibres ou les pieds à coulisse pour mesurer l’épaisseur, le diamètre ou la longueur des composants. Par exemple, on contrôle l’usure des engrenages pour vérifier si les dents restent dans les tolérances spécifiées.
Cette technique précise et fiable, surtout pour les pièces critiques, utilise parfois des équipements modernes comme les machines à mesurer tridimensionnelles (MMT) qui offrent une précision accrue et permettent de scanner les pièces pour créer des modèles 3D détaillés.
Les analyses vibratoires
Les vibrations anormales sont souvent un signe précurseur de problèmes mécaniques. Les capteurs installés sur les machines détectent et analysent les variations de fréquence et d’amplitude des vibrations. Par exemple, ils identifient des défauts dans les roulements ou les déséquilibres dans les arbres rotatifs.
Cette méthode est non invasive et fournit des résultats en temps réel, ce qui facilite l’intervention rapide. Grâce aux systèmes modernes qui intègrent des algorithmes avancés, les capteurs permettent de distinguer les vibrations normales de celles signalant un problème.
La surveillance de la température
Les anomalies thermiques indiquent souvent des frottements excessifs ou des surcharges mécaniques, grâce à des capteurs infrarouges ou des caméras thermiques qui mesurent les variations de température.
La méthode non destructive est adaptée à la surveillance continue des machines en fonctionnement. Les caméras thermiques modernes, combinées à des logiciels de traitement d’images, permettent d’obtenir des **cartes thermiques détaillées **pour une analyse approfondie.
Les analyses de lubrifiants et de fluides
Le contrôle des fluides permet de détecter des contaminants ou des débris indiquant une usure excessive. Le principe consiste à prélever des échantillons de lubrifiants pour analyser leur composition à la recherche de particules métalliques, d’eau ou de produits de dégradation. Il s’agit d’une méthode indirecte très fiable pour identifier les dégradations internes des pièces.
Cette approche s’inscrit parfaitement dans les stratégies de maintenance prédictive, en fournissant des indicateurs sur l’état global des machines.
Les inspections endoscopiques
Pour les composants difficiles d’accès, comme les cavités internes ou les tuyaux, l’endoscopie industrielle offre une solution efficace. On utilise des caméras miniatures montées sur des sondes pour explorer visuellement l’intérieur des machines. Cela permet de visualiser les zones cachées sans avoir besoin de les démonter, ce qui réduit ainsi le temps d’arrêt.
Les endoscopes modernes peuvent capturer des images haute résolution et sont parfois équipés de capteurs supplémentaires pour des analyses complémentaires.
Ces méthodes, souvent utilisées en combinaison, permettent de planifier des interventions ciblées qui réduisent les coûts et les risques d’arrêt imprévu. Leur choix dépend des caractéristiques des machines, des conditions d’exploitation et des objectifs de maintenance.
L’intégration de systèmes de surveillance sur les machines grâce à l’IoT industriel
L’avènement de l’Internet des Objets (IoT) transforme les pratiques de maintenance industrielle. Les systèmes connectés surveillent en temps réel les équipements et réduisent considérablement les risques de pannes majeures. Cette technologie offre aux gestionnaires des informations détaillées pour mieux planifier les remplacements ou réparations des pièces mécaniques.
Les capteurs intelligents, cœur de la maintenance connectée
Les capteurs intelligents jouent un rôle clé en capturant des données sur divers paramètres comme les vibrations, la température ou encore la pression. Ces capteurs, intégrés directement sur les machines, envoient en temps réel des alertes aux gestionnaires lorsqu’un seuil critique est atteint. La détection précoce réduit les temps d’arrêt non planifiés.
L’analyse des données pour une maintenance prédictive efficace
Les données collectées par les capteurs sont centralisées dans des logiciels de gestion (GMAO par exemple), souvent associés à des technologies d’intelligence artificielle. Ces systèmes analysent les tendances pour anticiper les défaillances.
Les entreprises équipées de ces systèmes profitent d’une meilleure planification des interventions et améliorent ainsi la durée de vie des équipements.
Une infrastructure connectée pour une vue d’ensemble globale
En intégrant les technologies IoT, il devient possible de surveiller plusieurs machines ou sites industriels simultanément via une plateforme unique. Par exemple, dans l’industrie agroalimentaire, les systèmes connectés permettent de suivre à distance les performances des équipements de conditionnement pour garantir un fonctionnement optimal. Par ailleurs, la centralisation des données facilite le reporting et la prise de décision.
La gestion proactive des pièces mécaniques est essentielle pour maintenir la productivité des machines de production. Identifier les causes des pannes courantes permet d’appliquer des méthodes de contrôle adaptées. L’intégration de systèmes de surveillance basés sur l’IoT permet par ailleurs d’anticiper les défaillances et limiter les temps d’arrêt coûteux. Adopter ces stratégies, c’est aussi investir dans une maintenance plus intelligente, alignée sur les exigences de l’industrie 4.0.