- Publié le 24 mai 2023
- Mis à jour le 9 janv. 2024
- 13 min
Comment détecter les pannes dans les armoires électriques ?
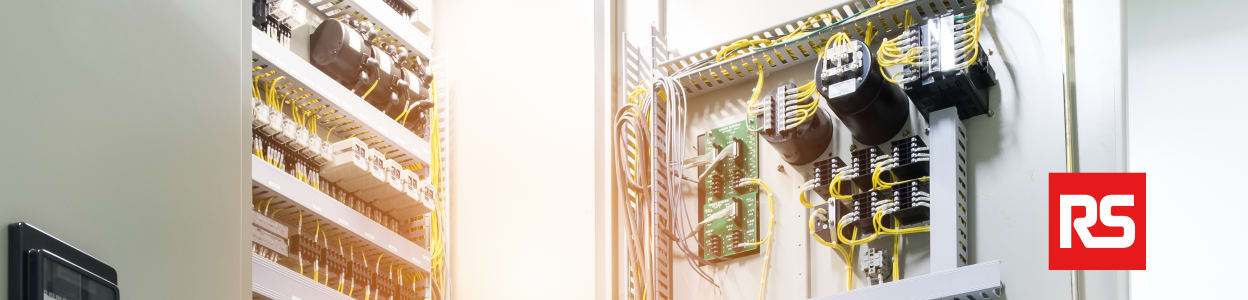
Article publié le 10/05/2023
Assurer les performances d’une armoire électrique dans le temps tout en évitant au maximum les défaillances, les pannes mais aussi et surtout les risques d’accidents… Telles sont les priorités des agents et responsables de maintenance. Mais comment s’y prendre et quelles sont les pratiques et les solutions à mettre en place ?
Une armoire électrique – ou armoire de distribution – joue un rôle primordial dans une entreprise. Elle sert en effet à abriter et à contrôler des équipements électriques, c’est pourquoi il est essentiel de veiller à ce que les mesures d'entretien et de sécurité adéquates soient mises en place. Rappelons que seuls des techniciens formés et certifiés sont habilités à effectuer des opérations de maintenance sur ce type d’équipement. L’Institut national de recherche et de sécurité (INRS) est clair sur ce point : « Il est obligatoire d’habiliter une personne qui réalise des opérations d’ordre électrique, qu’elle soit électricienne ou non. »
Aussi, toutes les précautions sont de mise, d’autant qu’une armoire électrique défectueuse peut avoir de graves conséquences et mettre en danger la vie des personnes, des biens et des équipements. Lors de l’intervention elle-même, le technicien devra également prendre les dispositions de sécurité les plus rigoureuses comme l'utilisation d'équipements de protection individuelle (EPI) appropriés ainsi que des outils adéquats requis pour son travail. Il s’agit aussi pour l’entreprise et le service maintenance de garantir que seule cette personne habilitée est en mesure d’intervenir, et pas une autre ; d’où la mise en place de dispositifs de protection et de barrières d’accès ou de verrouillage de l’équipement.
Ces éléments de protection sont essentiels et cela commence, d’une part, par l’emplacement même de l'armoire ; celle-ci doit être installée dans un endroit propre et sec, à l'abri de l'humidité et, naturellement, des fuites d'eau. D’autre part, il est pertinent d’installer des barrières physiques telles que des couvercles de protection et des écrans afin de protéger l'équipement contre les dommages accidentels ou le vandalisme ; d’ailleurs, dans tous les cas, l'accès à l'armoire électrique doit être limité et contrôlé afin de minimiser les risques d'accidents ou de modifications non autorisées du système. La mise à la terre est également une condition sine qua non pour éviter les chocs électriques et garantir le bon fonctionnement du système. Il en est de même pour la sécurité incendie qui nécessite la présence d'un extincteur par exemple. Enfin, outre le fait d’éviter de stocker des composants ou des matériaux inflammables à proximité, une bonne ventilation est nécessaire, tout comme le fait d’aérer les câbles (et ne pas les empiler).
Entretien et maintenance d’une armoire électrique : de l’inspection visuelle à la recherche de la panne
Pour une armoire électrique, avant même de parler de performance, l'entretien vise avant tout la sécurité. Celle-ci doit être considérée comme étant une priorité absolue. Pour ce faire, il est important que l'alimentation de l'armoire électrique soit coupée et qu’un système de verrouillage et d’étiquetage soit utilisé afin d’éviter toute mise sous tension accidentelle et tout risque d'électrocution ou de choc électrique au cours du processus de maintenance. Notons qu’une consignation et une mise en sécurité des énergies est indispensable pour intervenir en toute sécurité (et éviter qu’une personne ne remette accidentellement l’alimentation en route). Aussi, pour s'assurer que l'alimentation électrique a bien été coupée, il est recommandé d'utiliser un testeur de tension.
D’autres précautions sont à prendre en compte, comme l’inspection minutieuse de l'équipement, des connexions et des fixations dans le but d’identifier tout signe d'usure, de surchauffe (décoloration des fils ou fonte de l'isolation par exemple) ou des dommages pouvant s’avérer dangereux. Autre point de vigilance : la présence de poussière et de débris qui se sont accumulés à l'intérieur de l'armoire électrique. Le technicien doit ainsi bien examiner les filtres à air et s'assurer qu'ils ne soient pas obstrués.
Après avoir effectué les contrôles visuels et physiques initiaux, le technicien doit effectuer des tests électriques sur chaque composant de l'armoire électrique. Il vérifiera ainsi que chaque pièce est en bon état de fonctionnement et identifiera les éventuels problèmes à résoudre. Les tests de continuité, de résistance d'isolement, de tension et de charge sont quelques-uns des tests qu'il peut être nécessaire d'effectuer.
Une fois les tâches de maintenance et d'inspection terminées, l'armoire doit être réassemblée et la source d'alimentation remise en marche. Un étalonnage ou un réglage après la maintenance peuvent également s’avérer nécessaires. Enfin, tous les registres et schémas électriques pertinents doivent être mis à jour et bien documentés pour référence ultérieure.
Kit de consignation
Trouvez tout ce dont vous avez besoin pour la maintenance de vos armoires électriques avec nos kits de consignation.
Bien contrôler l’isolement, dont le défaut est facteur de risques importants
Un défaut d’isolement correspond à une fuite de courant. Quelle qu’en soit l’origine, il présente à la fois une surconsommation d’énergie mais aussi des risques, avant tout pour la vie des personnes. C’est le cas des chocs électriques comme l’électrisation (par contact direct ou indirect) ou de l’électrocution (provoquant la mort) ; la mise à la terre permet déjà d’évacuer vers la terre (d’où son nom) le courant de fuite en cas de défaut d'isolement sur un appareil électrique.
Mais au risque physique s’ajoute la détérioration des équipements eux-mêmes, qu’il s’agisse de chocs électriques et surtout des risques d’incendie (à l’origine électrique pour 25 % d’entre eux !) ou d’explosion, dont la source provient bien souvent, sinon d’un échauffement de câble (à cause d’une surcharge par exemple), d’un défaut d’isolement ou d’un court-circuit responsable d’un arc électrique. Aussi, le défaut d’isolement influe sur la disponibilité de l’énergie électrique. L’absence soudaine d’énergie est susceptible de détériorer à son tour les équipements les plus sensibles voire de se révéler également dangereuse pour les personnes (arrêt brusque d’une machine, de l’éclairage dans l’atelier etc.). La perte d’exploitation liée à l’arrêt de production entre aussi en ligne de compte.
Concernant les causes de défaut d’isolement, celles-ci sont diverses et se cumulent parfois. Il peut s’agir – le plus souvent sur des installations vieillissantes – de poussières, d’un isolant de câble détérioré ou de câbles défectueux, de problèmes d’isolation des conducteurs ou des fils de bobinage des transformateurs, de décharges électrostatiques, des phénomènes de surtension voire d’un effet de foudre.
Notons qu’il est nécessaire de se référer à la norme NF C 15-100 ; mise à jour en 2002, celle-ci définit les règles de conception, de réalisation et d'entretien des installations électriques basse tension en France. Elle s’applique aux particuliers ainsi qu’aux entreprises, aussi bien pour des constructions neuves qu’existantes. Si la norme énumère les éléments indissociables d’une installation électrique conforme (tableau et compteur électriques, disjoncteurs général et différentiels), elle impose également une vérification annuelle des installations (état du câblage et identification d’éventuelles fuites de courant), selon les exigences du Règlement général sur les installations électriques (RGIE). Enfin, l’installation doit être validée par le Comité national pour la sécurité des usagers de l'électricité (Consuel).
Quelles sont les normes électriques des bâtiments industriels ?
Tous les bâtiments, qu’ils soient domestiques, industriels ou tertiaires, sont soumis à des normes en ce qui concerne les installations électriques. Les bâtiments industriels sont concernés à plus d’un titre, car ils utilisent à la fois des installations à basse tension et à haute tension. Voici tout ce que vous devez savoir sur les normes électriques des bâtiments industriels.
Comment tester un appareil de protection électrique ?
Face aux multiples risques liés aux défaillances d’une armoire électrique, il existe heureusement des dispositifs de protection électrique ; il s’agit à la fois des disjoncteurs, des fusibles ou encore des relais et des DDFT (disjoncteur de fuite à la terre). Ceux-ci ont pour objectif de s'assurer que l’installation fonctionne correctement.
Conçus pour interrompre le flux de courant lors que survient un un court-circuit ou une surintensité, ils sont chargés de protéger le circuit électrique. Premier dispositif bien connu, le disjoncteur. Placé à l’extrémité du tableau électrique, il permet de couper l’électricité en cas d’anomalies. Quant aux disjoncteurs différentiels, à la différence du disjoncteur général, ils protègent en outre les personnes en cas de choc électrique en détectant les courants de fuite, ainsi que les équipements électriques contre les surtensions.
Une tâche importante de l’agent de maintenance consiste à tester ces disjoncteurs. Cette opération permet de vérifier l’état des raccordements et de s’assurer que l’installation est toujours en bon état de fonctionnement. Pour ce faire, il convient de respecter quelques règles de mise en pratique, à commencer par déconnecter le dispositif du circuit électrique.
Pour tester un dispositif de protection électrique, la première étape consiste à identifier le dispositif à tester. Cette étape est importante car les méthodes de test varient en fonction du type de dispositif de protection électrique. Parmi les types de dispositifs de protection électrique les plus courants figurent les disjoncteurs, les fusibles, les relais et les disjoncteurs de fuite à la terre (DDFT) et autres disjoncteurs magnéto-thermiques.
Une fois le dispositif à tester identifié, il est préférable de le déconnecter du circuit électrique qu'il protège. La méthode de test spécifique dépendant du type d'appareil, pour un disjoncteur par exemple, il est conseillé d’utiliser un multimètre. Il est aussi possible de simuler un courant de défaut pour s’assurer que le dispositif se déclenche au bon moment. Idem pour un disjoncteur de fuite à la terre où il est possible d’utiliser un bouton de test pour simuler un défaut à la terre et garantir qu’il se déclenche et interrompt le circuit.
Multimètres
Pour tester correctement vos appareils, utilisez un multimètre. Découvrez les produits proposés par RS France.
Pourquoi et comment contrôler la continuité d’une installation électrique ?
Indispensable pour garantir un système électrique sûr et durable, le contrôle et le test de continuité permettent de vérifier qu'il n'y a pas de rupture dans le circuit électrique, pouvant entraîner un risque pour la sécurité, endommager l'équipement ou provoquer une coupure de courant. Ce contrôle de la continuité doit être régulier. Celui-ci s’effectue – après avoir préalablement coupé l'alimentation électrique – à l’aide d’un multimètre ou d’un testeur de continuité, des outils conçus pour envoyer un petit courant électrique dans un conducteur situé entre deux points d'un circuit afin de déterminer si le chemin électrique est continu ou non.
Une multitude de solutions existent
L’objectif d’un agent ou d’un technicien de maintenance est de détecter tous signes de défaillance sur une armoire électrique, en particulier les signaux faibles sur des tableaux basse et moyenne tension car les principales causes de défaillance résident dans le serrage de connexion entre le tableau et le disjoncteur. Autres causes de défaillance : l’environnement poussiéreux ou humide, et donc générateur de corrosion, ou encore des défaillances dans le mécanisme du disjoncteur.
Heureusement, de nombreuses solutions et équipements existent, à commencer par des instruments de test et mesure destinés à contrôler l’installation électrique comme les contrôleur, les multimètres numériques, les pinces multimètre, les testeurs d’isolement, de terre et d’appareillages électriques… Pour l’isolement, des diélectromètres sont nécessaires pour mesurer la tenue diélectrique, et un mégohmmètre pour la mesure de la résistance d’isolement. En matière d’outillages aussi, il convient de s’équiper à la fois de pinces coupantes et d’une pince à dénuder, de tournevis, de jeux de cliquet et de clés plates, d’une pince et de colliers Colson ou encore d’une perceuse à batterie…
Pour des démarches relevant davantage de la maintenance prévisionnelle, il est aussi possible de monitorer les tableaux électriques et les équipements critiques, de recourir à la thermographie infrarouge même si, durant les intervalles de maintenance préventive, des défaillance peuvent survenir et déclencher un incendie. Des solutions de surveillance en temps réel se développent cependant de plus en plus, à l’image de capteurs de température auto-alimentés et positionnés entre le disjoncteur et le tableau ou les câbles, des capteurs d’humidité pour surveiller en temps réel les risques d’humidité, de corrosion et les points de rosé.
Enfin, il est important de ne pas négliger deux aspects. L’un est inhérent à la sécurité de l’opérateur que sont les équipements de protection tels que les harnais de sécurité et bien sûr les EPI contre les risques électriques : casque isolant et de protection contre les projections de particules en fusion, équipements de protection oculaire et faciale, sans oublier naturellement les gants, chaussures et combinaisons spécifiques et isolants. À ce titre, l’INRS précise que ces équipements (de catégorie III, c’est-à-dire présentant un risque mortel) doivent impérativement être marqués CE et répondre à une classification précise déterminée par la réglementation européenne. Second aspect, la gestion des pièces de rechange afin d’éviter la coupure d’alimentation et assurer la continuité de la production : ainsi, câbles, cosses, connecteurs, disjoncteur et disjoncteur différentiel, parafoudre… doivent être disponibles à tout moment en magasin de pièces.