- Publié le 30 oct. 2023
- Mis à jour le 9 juil. 2024
- 8 min
Détecteur de pression : Principe de fonctionnement
Un capteur de pression est un instrument de mesure ayant des propriétés déterminées comme la résolution, l'exactitude et la marge des erreurs. Il est utilisé dans différentes applications industrielles.
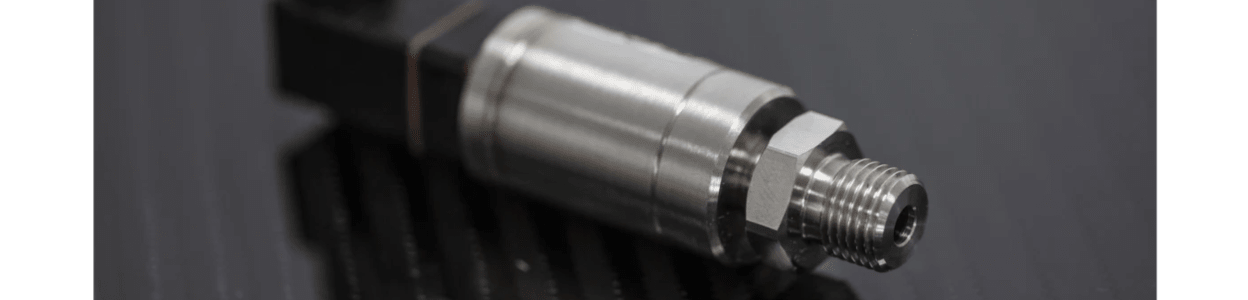
Un détecteur de pression (également appelé capteur) est un instrument de mesure ayant des propriétés déterminées comme la résolution, l'exactitude et la marge des erreurs. Il est utilisé dans différentes applications industrielles.
La mesure de pression dans les laboratoires et les installations pneumatiques et hydrauliques est essentielle pour prévoir les erreurs et les défaillances qui peuvent s'y produire à un instant donné. Nous expliquons ici le principe de mesure de la pression et le fonctionnement de chaque capteur de pression.
Qu’est-ce qu’un capteur de pression ?
Définition du capteur de pression
Un capteur de pression est un instrument de mesure capable de convertir la pression hydraulique ou pneumatique en un signal électrique analogique ou numérique qui sera envoyé ultérieurement comme une donnée à traiter par d'autres dispositifs.
À quoi sert un capteur de pression ?
Le détecteur de pression est utilisé pour contrôler la pression en question et pour aider à la détection des défauts apparents ou intermittents dans les processus industriels. Il est largement utilisé dans diverses applications et dans plusieurs secteurs industriels, tels que l'énergie, l'automobile, l'aérospatiale, la production et les traitements chimiques…
Comment fonctionnent les capteurs de pression ?
Un capteur de pression est composé principalement d'un élément sensible à la pression et d'un élément transducteur. La pression du fluide dans une canalisation peut varier au cours du temps. Cette variation de pression est détectée et mesurée par l'élément sensible du capteur. L'élément transducteur convertit cette grandeur physique en un signal électrique envoyé vers des calculateurs ou des automates pour le traiter, si nécessaire.
Qu’est-ce qu’une mesure de pression ?
Les fluides s'écoulent dans les canalisations pour remplir ou vider des réservoirs ou des cuves de stockage. Étant donné que ces fluides peuvent avoir des propriétés totalement différentes, il existe différents principes pour mesurer la pression. Cette dernière est le résultat d'une force agissant sur une surface. Elle est calculée comme suit :
P=F / S
F: force de fluide appliquée en N
S: surface d´application en m²
P: pression de fluide en N/m²
Lorsque la pression est appliquée, l'élément sensible se déforme et une variation de capacité, de résistance ou de fréquence est indiquée. Elle est traduite en termes de pression par l'intermédiaire de l'élément transducteur.
Quelles sont les unités de mesure de pression les plus courantes ?
Comme indiqué auparavant, la pression P est une force F exercée par un fluide mesurée en N sur une surface S mesurée en m². Elle est équivalente à l'unité N/m² (Newton par mètre carré) ou Psi (Pound per square inch).
Les origines scientifiques de la mesure de pression remontent au milieu du 17ème siècle. Galileo Galilei a tenté de s'affranchir des différences d'altitude à l'aide d'une pompe. Evangelista Torricelli a mené des recherches avec des colonnes de mercure et a découvert l'état de vide. Blaise Pascal poursuit les recherches pour déterminer la pression de l'air. La pression s'exprime dans le système international par le Pascal (Pa). Elle est aussi exprimée en hauteur de colonne de mercure : millimètre de mercure (mmHg). Elle peut être mesurée en bars.
Le tableau ci-dessous représente les conversions des unités de mesure de pression les plus couramment utilisées :
Pa | N/m² | bar | mmHg | |
---|---|---|---|---|
1 Pa | 1 | 1 | 0.00001 | 0.0075 |
1 N/m² | 1 | 1 | 0.0013 | 0.0013 |
1 bar | 100 000 | 100 000 | 1 | 750 |
1 mmHg | 133.3 | 133.3 | 0.0013 | 1 |
Quelle est la différence entre les pressions absolue et relative ?
Une pression absolue est mesurée dans une cellule absolue ou dans une chambre dite de référence qui est presque vide. Sa pression de référence est égale à 0 bar. Le capteur de pression absolue relève une valeur de pression appliquée sur une membrane. Cette pression ne s'affecte ni des variations de pression atmosphérique, ni des changements de température.
Une pression relative est mesurée dans une cellule relative qui permet la compensation de la pression atmosphérique. Le capteur de pression relative mesure une valeur de pression par rapport à la pression atmosphérique ou ambiante.
Les différents types de capteurs de pression
Plusieurs types de capteurs de pression sont utilisés dans des systèmes pneumatiques ou hydrauliques pour mesurer la pression du fluide. Cette diversité est due essentiellement à la technologie adaptée pour effectuer les mesures. Découvrez les différents exemples de capteurs de pression disponibles sur le marché :
- Les capteurs de pression piézorésistifs
- Les capteurs de pression capacitifs
- Les capteurs de pression résistifs à couche mince
- Les capteurs de pression à fibre optique
- Les capteurs de pression hydrostatique
Le capteur de pression piézorésistif
Un capteur de pression piézorésistif est constitué d'un matériau résistif dont sa résistance varie lorsqu'il est soumis à une force ou une contrainte mécanique. La variation de résistance est proportionnelle à une force de fluide appliquée sur la cellule du capteur. Un transducteur convertit cette variation de la résistance en un signal électrique. Le capteur de pression piézorésistif permet d'avoir des mesures dotées d'une très bonne précision et une marge d'erreurs minimisée.
Le capteur de pression capacitif
Comme un condensateur, le capteur de pression capacitif est composé d'une cellule constituée d'une armature et une membrane positionnées entre eux d'une distance formant un volume rempli d'un liquide. Ce volume est appelé une capacité. Lorsqu'une pression est appliquée. la membrane se déforme pour varier cette capacité. Cette variation mesurée est transmise via un transducteur sous forme d'un signal électrique à traiter.
Le capteur de pression résistif
Un capteur de pression résistif à couche mince possède une sensibilité très élevée aux variations de la pression grâce à une couche de matériau résistif à quelques nanomètres d'épaisseur. Ce type de capteur est utilisé pour effectuer des mesures exactes dans certaines applications industrielles.
Le capteur de pression à fibre optique
Comme son nom l'indique, le capteur de pression à fibre optique est composé des fibres optiques capables de mesurer la pression appliquée. Lorsqu'une pression est appliquée sur ces fibres et un faisceau lumineux les traverse, la longueur d'onde varie pour relever les différentes variations de la pression. Ce capteur permet de remplacer les instruments de mesure conventionnels dans des milieux exigeants comme les environnements à une température ou à une humidité élevée.
Le capteur de pression hydrostatique
Le capteur de pression hydrostatique est composé d'une cellule développée spécialement pour mesurer les pressions hydrostatiques. Cette cellule utilise la technologie des résistances déposés sur un élément en silicium sous la forme d'un pont de Wheatstone. La pression hydrostatique est mesurée en fonction de la gravité, de la masse volumique et de la hauteur de liquide. En considérant le même liquide et une gravité constante, la pression hydrostatique est proportionnelle au niveau de remplissage du liquide en question. A la variation de la hauteur, une huile incompressible transmet la pression de la membrane vers l'élément en Silicium qui la traduit en un signal électrique.
Les différentes applications des détecteurs de pression par secteur
Les capteurs de pression piézorésistifs sont installés dans les circuits d'alimentation des véhicules. Les capteurs de pression pneumatiques mesurent la pression d'air d'admission entrant dans le collecteur. D'autres capteurs sont utilisés pour mesurer la pression du carburant et la régler si nécessaire. Les capteurs TPMS sont utilisés pour mesurer la pression en temps réel des pneus de véhicules. En cas de défaillance, ces capteurs de pression alertent le système de commande pour y intervenir. Les capteurs de pression capacitifs sont utilisés dans les installations de gaz et des hydrocarbures, d'agroalimentaire, et d'autres secteurs industriels. Les capteurs de pression à fibre optique sont utilisés dans l'industrie nucléaire.
Les capteurs de pression dans l’industrie agroalimentaire
Essentiels à l’industrie agroalimentaire, les détecteurs de pression jouent un rôle crucial pour garantie la sécurité, la qualité et l’efficacité des processus de production. Utilisés pour surveiller et contrôler la pression dans les systèmes de traitement et d’emballage, ils empêchent de nombreuses défaillances techniques, à l’image de la surpression, pouvant compromettre la qualité des produits alimentaires. Ces capteurs répondent à des normes strictes de sécurité alimentaire, doivent résister à des environnements de nettoyage rigoureux et effectuer des mesures avec précision. Autre point à ne pas négliger, les capteurs de pression à destination de l’industrie agroalimentaire doivent être fabriqués dans des matériaux compatibles avec les aliments afin d’éviter toute contamination.
Les détecteurs de pression continuent alors à évoluer pour les exploiter dans une variété d'applications industrielles. Alors, veillez à ce que votre choix de capteur soit le plus adapté à votre installation pneumatique ou hydraulique en consultant, sur notre site web, les fiches techniques de noscapteursdisponibles maintenant sur le marché.
Pour aller plus loin
Liens connexes
- CI de capteur de pression
- Détection de niveau : choisir le capteur adapté à vos besoins...
- Capteurs photoélectriques - Les 3 modes
- Guide complet sur les capteurs de proximité inductifs
- Comprendre les fondements des capteurs photoélectriques
- Capteur de pression barométrique Infineon 120kPa CMS, VLGA 8 broches
- Capteur de pression Telemecanique Sensors XMEP pour Air Huile...
- Capteurs de proximité RS PRO : Faire le bon choix de référence...