- Publié le 9 janv. 2023
- Mis à jour le 29 août 2023
- 4 min
Comment bien se préparer pour l'industrie 4.0 ?
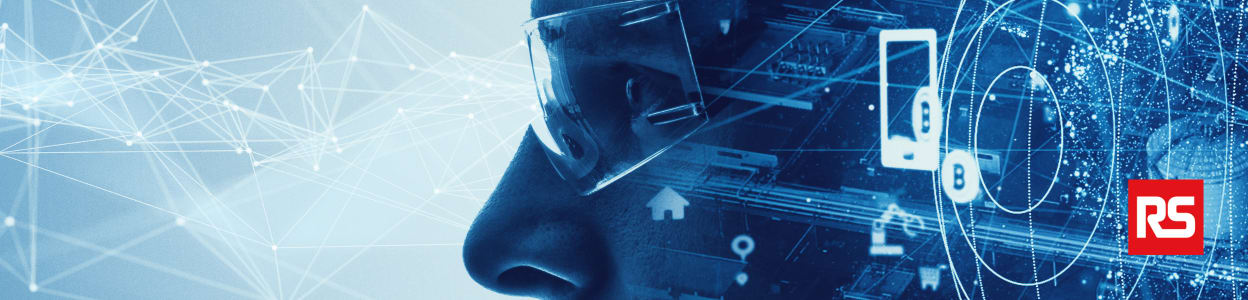
Article publié le 20/03/2020
Quand on évoque l’industrie du futur, on pense dans un premier temps aux lourds investissements nécessaires pour le remplacement du matériel mais également aux nouvelles compétences à acquérir… Et bien, ce n’est pas une fatalité, la transition peut se faire plus sereinement !
De plus, le remplacement d’un parc de machines a des conséquences majeures sur les entreprises. Outre, les investissements couteux imputés au remplacement du matériel pouvant atteindre des centaines de milliers voire des millions d’euros, ces changements impliquent l’acquisition de nouvelles compétences. En effet, tous les intervenants opérant sur les équipements de production, agents de maintenance et opérateurs, doivent acquérir les nouvelles connaissances requises.
Alors ne serait-il pas possible de conserver le parc de machines ?
L’usine du futur
Elle est considérée comme la quatrième révolution industrielle. Elle est appelée également Industrie 4.0. Ses atouts principaux permettent une production plus sûre, une flexibilité accrue et une surveillance augmentée aux outils industriels. Cependant, les entreprises se doivent de surmonter un certain nombre d’obstacles pour mettre en place cette nouvelle manière de produire.
Basée sur le concept de l’internet des objets, la version industrielle de cette technologie mise sur la collecte des données capteurs pour informer, optimiser, anticiper et prédire le fonctionnement des outils de production.
Quel est l’élément clé de l’industrie 4.0 ?
Le concept de l’usine du futur tient essentiellement sur le partage de données, non seulement entre les machines et le système central mais aussi entre machines.
Les données capteurs permettent de surveiller les performances des outils de production, d’anticiper l’approvisionnement des matières premières, de gérer la maintenance des différentes machines. De plus, elles offrent des moyens de contrôle plus évolués, intuitifs et conviviaux, utilisant des tablettes, smartphones ou encore lunettes de réalité augmentée.
Quelle est la problématique majeure de la transition vers l’usine du futur ?
Dans la plupart des entreprises, l’outil de production s’est constitué au fur et la mesure des besoins rencontrés. Ainsi l’atelier de production se compose de nombreuses machines provenant de marques hétéroclites. Ces machines ont été conçues pour communiquer uniquement avec un logiciel propriétaire. Dotés de leur propre langage, elles sont incapables de communiquer avec les autres machines de l’atelier.
La plupart des machines sont dotées d’une intelligence restreinte, d’une capacité de mémoire quasi nulle et d’un protocole de communication datant des années 80-90. A défaut de langage commun, la collecte des données machines doit être opérée de façon individuelle, un procédé incompatible avec le concept de partage des données de l’usine du futur.
Dans le cas d’une communication inexistante, les données sont collectées sur chaque machine individuellement soit par chargement de clé USB ou tout simplement relevées manuellement et intégrées à un fichier de type tableur pour analyse. Ce procédé est consommateur de temps et risqué en termes d’erreur.
Quelle est la réponse aux problèmes de communication ?
La mise à niveau « retrofit » en anglais des machines existantes est aujourd’hui parfaitement envisageable. Elle est rendue possible grâce à des ordinateurs industriels conçus pour apporter l’intelligence aux parcs de machines de production existants.
Ces dispositifs ont pour priorité de traduire en un langage commun les différents protocoles de communication, datant de la fin du siècle dernier. Ainsi, ils opèrent comme de véritables passerelles entre la machine et le système de contrôle de production MES (Manufacturing Execution System).
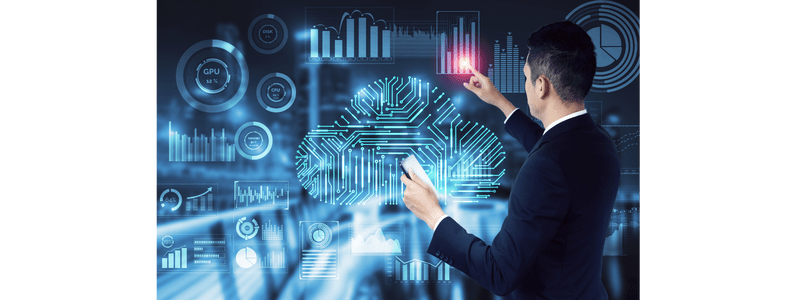
Les dirigeants d’entreprises pouvaient penser jusqu’à présent que la digitalisation des outils de production était réservée uniquement aux grandes entreprises pouvant réaliser de lourds investissements, mais ceci était sans compter sur les possibilités de mettre à niveau le matériel existant. Cette solution a pour bénéfice de limiter le coût de la transition et la formation des opérateurs et agents de maintenance. Il n’y a ainsi plus aucune raison de ne pas envisager la transition vers le monde de l’industrie du futur!
Services & produits associés
Ordinateur industriel
Un ordinateur industriel est un système informatique robuste conçu pour les applications à long terme dans les environnements difficiles où le système nécessite une protection contre les températures extrêmes etc.
RS Smart Inventory Management
Une solution intelligente pour la gestion et l'optimisation de vos stocks.
Pour aller plus loin
Liens connexes
- Comment bien débuter avec l'Arduino ?
- Comment bien choisir sa caméra thermique ?
- Comment bien choisir ses gants de protection ?
- Facturation électronique : profitez du report pour mieux préparer...
- Guide : comment bien choisir ses protections auditives ?
- 3 Conseils Pour Définir Et Bien Choisir Ses Joints Toriques
- Comment nettoyer en fonction de la surface ?
- Comment réduire le coût de la maintenance dans l'industrie ?