- Publié le 9 janv. 2023
- Mis à jour le 18 nov. 2024
- 10 min
Maîtriser la sécurité pendant les maintenances
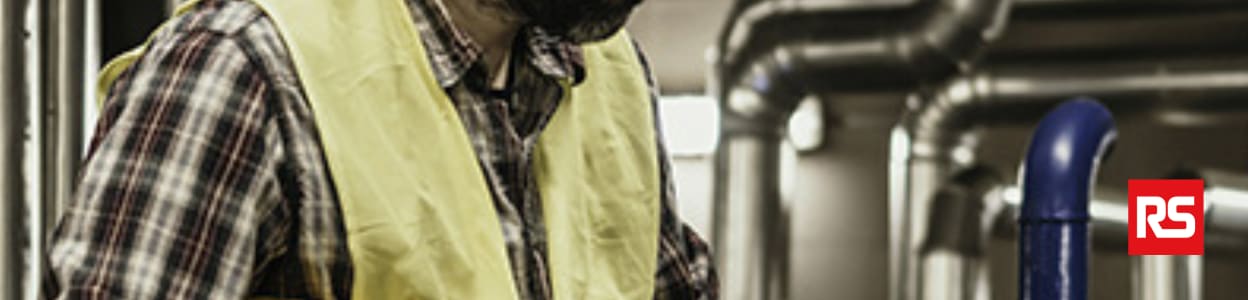
Dans le secteur pharmaceutique, si la maintenance est un vecteur d’amélioration des performances techniques et économiques, il est indispensable de maîtriser la sécurité sanitaire et celle du personnel lors des interventions. Quels sont les risques pour les agents de maintenance ? Quelles mesures d’hygiène et de sécurité adopter ? Comment sécuriser les opérations ? Un point pour comprendre comment adopter une conception de l’organisation du travail de maintenance adaptée.
L’évaluation des risques pour les agents de maintenance
Si la démarche classique est appliquée (analyse des tâches, inventaire des produits et de leur niveau de dangerosité, mise en place d’un plan d’action et de moyens de prévention), il est important de rappeler que le personnel de maintenance est amené à réaliser de très nombreuses interventions.
Entre les tâches répétitives et les maintenances de machines dangereuses, parfois difficiles à manipuler ou à atteindre, les opérations sont très variées. Sans compter que les agents de maintenance sont amenés à travailler de jour comme de nuit. Piliers du bon fonctionnement de la production, ils subissent souvent une très forte pression mentale.
L’AFIM, Association Française des Ingénieurs et responsables de Maintenance, dresse un bilan préoccupant et déplore encore de trop nombreux accidents. Leur nombre y est en effet 3 fois plus élevé que la moyenne nationale. 2 accidents du travail sur 10 sont liés aux activités de maintenance. Les risques de développer des maladies professionnelles, trouble musculo-squelettique, TMS, cancers, surdité…, sont 6 fois plus importants. Enfin, 1 accident mortel sur 10 est dû à la maintenance.
On estime aussi que 50% des accidents de maintenance sont causés par le manque de maîtrise des énergies électriques, hydrauliques et pneumatiques. Il est donc absolument essentiel de renforcer la sécurité du personnel tout en sécurisant les interventions grâce à la norme NFX 60-400 et à la démarche Securafim conçue par l’AFIM et l’INRS. Dans le secteur pharmaceutique, s’ajoutent les risques chimiques et biologiques impliquant le strict respect des règles HSE.
Les règles HSE, Hygiène Sécurité et Environnement
Si le Code du travail s’applique en termes de sécurité et d’hygiène, les exigences HSE apportent des mesures spécifiques en fonction du secteur d’activité. La convention collective nationale de l'industrie pharmaceutique impose ainsi une prévention des risques “compte tenu de l’accueil de tout public dans l’entreprise”. Celle-ci est donc tenue d’évaluer et d’identifier les risques afin de mettre en place des modalités précises de fonctionnement.
Hygiène : les opérations de nettoyage
Plusieurs interventions se distinguent :
- Le pré-désinfection Un détergent bactéricide permet d’éliminer les micro-organismes indésirables.
- Le nettoyage Mécanique (par ultrasons) ou chimique (avec une machine à laver), il permet de nettoyer les traces de salissures sur les surfaces de travail.
- La désinfection : Cette opération intervient ensuite pour tuer les bactéries, virus et champignons présents. Les méthodes dépendent des matériels (sols, machines, verreries, pipettes automatiques, milieux de culture…). Sont utilisés des produits bactéricides, fongicides et virucides comme la Javel ou l’alcool à 70°.
- La stérilisation : Un autoclavage permet d’éliminer les micro-organismes restants.
- L'antisepsie : Cette opération permet d’inactiver des virus sur des tissus vivants.
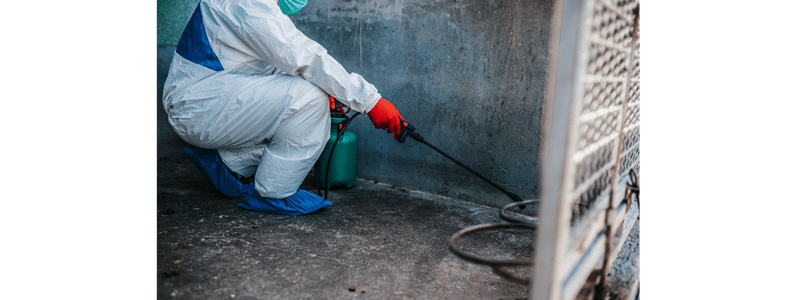
3 niveaux de sécurité en fonction des environnements
Ces niveaux déterminent le degré de dangerosité du lieu de travail. Les contrats de maintenance précisent les délais et consignes d’intervention.
Dans les zones confinées, si le nettoyage est généralement assuré par les utilisateurs, une intervention extérieure doit être réalisée après désinfection des locaux et des ustensiles. Par exemple, dans les salles blanches, appelées aussi clean rooms, le nombre de particules est contrôlé pour limiter la présence de poussières dans l’air. Les équipements respectent la classification ISO en fonction du niveau de sécurité. Dans ces espaces confinés de niveau 3, sont généralement prévues une maintenance préventive mensuelle et un entretien de tous les équipements une fois par an.
Les équipements de protection individuelle
Les règles HSE imposent aussi le port d’EPI : blouse de travail, surchaussures, charlotte, gants, lunettes, masque… Les EPI protègent les opérateurs mais permettent aussi de limiter les risques de pollution et de contamination. Ainsi, dans une zone stérile, comme sur des lignes de production d’injectables, le personnel doit être équipé d’une combinaison intégrale de protection.
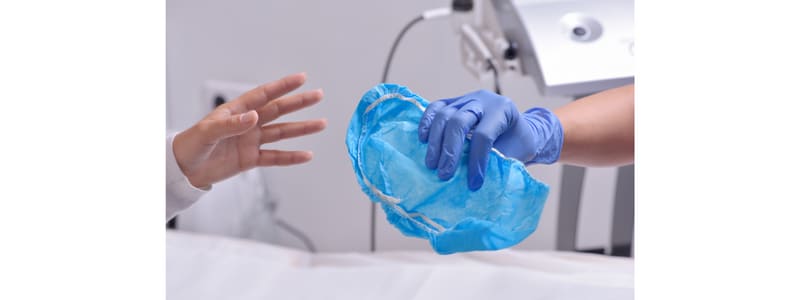
Les interventions de maintenance internalisée et externalisée
Il est important de distinguer ces deux types d'intervention qui sont très différentes.
La maintenance internalisée
Les ouvriers de maintenance font partie du service technique de l’entreprise, leur intervention est assez rapide mais ces techniciens ne sont pas toujours spécialisés ou formés pour procéder à des maintenances nécessitant des connaissances techniques plus poussées.
La maintenance externalisée
Ses principaux avantages sont la flexibilité, les compétences des intervenants et la réduction globale des coûts. Qu’elle soit totale ou partielle, la maintenance externalisée doit être définie de façon très précise dans un cahier des charges et dûment contractualisée.
Par ailleurs, certaines difficultés ne sont pas négligeables : la méconnaissance des équipements, des procédures ainsi que des environnements de travail sont autant d’éléments qui peuvent être source d’accidents. Notons que la formation et l’encadrement des agents sous-traitants est un enjeu majeur pour réduire les risques d’accident.
Comment garantir plus de sécurité lors des opérations de maintenance ?
Coordonner les interventions
Lorsque plusieurs opérations de maintenance externalisée sont prévues, il est obligatoire de déterminer un plan de prévention . Ce planning permet d’organiser les interventions pour assurer la sécurité des techniciens et éviter des accidents.
Former les agents à la sécurité
Si la méconnaissance des opérations en cours est une réelle source d’accident pour le personnel des entreprises intervenantes, d’autres ignorances sont aussi dangereuses : l’environnement de travail, les agents biologiques, leurs dangers... La formation permet ainsi de pallier ces manques mais aussi d’informer les agents de maintenance des risques pour leur santé et des mesures d’hygiène à adopter. Il s’agit de leur apprendre les bonnes pratiques en laboratoire, les consignes, le port et l’utilisation des EPI, équipements de protection individuelle…
Mettre en place une maintenance préventive
Si elle paraît de prime abord relativement onéreuse, le suivi est meilleur et l’investissement plus rentable dans le temps. Pour déterminer les situations à risques et les points critiques, la première des étapes est de réaliser une étude de criticité pour déceler les éventuels défauts et anticiper les risques de panne. La maintenance préventive permet ainsi de fournir des recommandations et des améliorations à prévoir. Pour prévenir les arrêts de production, il est conseillé de stocker certaines pièces dites “critiques” qui sont nécessaires pour intervenir rapidement en urgence.
Faciliter les opérations de maintenance grâce à la GMAO
La GMAO, Gestion de Maintenance Assistée par Ordinateur, est une innovation au service de la maintenance. Pour l’industrie pharmaceutique, elle garantit de s’inscrire dans le respect de la réglementation en sécurisant les opérations de maintenance tout en offrant une amélioration de la productivité. Le logiciel GMAO, très facile d’accès, permet d’être utilisé par tous les opérateurs de maintenance.
Les différents types d'opérations de maintenance
La maintenance se décline en plusieurs catégories distinctes, chacune ayant son importance dans le maintien optimal des équipements.
La maintenance préventive
Comme nous l’avons évoqué précédement. Cette approche proactive vise à anticiper les pannes avant qu'elles ne surviennent. Elle s'appuie sur des inspections régulières, des mesures et des analyses de données pour détecter les signes précurseurs de défaillance. Les interventions sont planifiées selon un calendrier précis, ce qui permet d'optimiser les ressources et de minimiser les temps d'arrêt.
La maintenance corrective
Également appelée maintenance curative, elle intervient après la détection d'une panne. Son objectif est de remettre rapidement l'équipement en état de fonctionnement. Bien que parfois inévitable, ce type de maintenance doit être limité car il engendre souvent des coûts plus élevés et des interruptions non planifiées.
L'importance de la documentation technique
Les procédures standardisées
Chaque intervention doit suivre des procédures précises, documentées dans des fiches techniques. Ces documents détaillent les étapes à suivre, les outils nécessaires et les mesures de sécurité à respecter.
La traçabilité des interventions
Un système de suivi rigoureux permet de :
- Documenter l'historique des interventions
- Analyser les causes récurrentes de pannes
- Optimiser les plannings de maintenance
- Améliorer continuellement les processus
Les niveaux de maintenance : une approche structurée
La maintenance industrielle s'organise selon différents niveaux d'intervention, chacun nécessitant des compétences et des ressources spécifiques. Cette hiérarchisation permet d'optimiser la gestion des équipements tout au long de leur cycle de vie.
Le premier niveau de maintenance
Il correspond aux actions simples réalisées par les opérateurs au quotidien : contrôles visuels, nettoyage, réglages basiques. Ces interventions préventives permettent de détecter rapidement les anomalies et constituent la première ligne de défense contre les pannes.
La maintenance de niveau intermédiaire
Réalisée par des techniciens qualifiés, elle comprend les opérations de maintenance préventive systématique et conditionnelle. Ces interventions programmées incluent le remplacement des pièces d'usure, les contrôles approfondis et les réglages complexes. La maintenance conditionnelle s'appuie sur des mesures et analyses pour déterminer le moment optimal d'intervention.
La maintenance spécialisée
Ce niveau supérieur concerne les interventions complexes nécessitant une expertise pointue. Les techniciens spécialisés interviennent pour :
- Les réparations majeures
- Les modifications techniques
- Les améliorations de performance
- Les diagnostics approfondis
La maintenance prédictive
Représentant l'évolution la plus récente, elle utilise l'analyse des données et l'intelligence artificielle pour anticiper les défaillances. Cette approche permet d'optimiser les interventions en fonction de l'état réel des équipements, réduisant ainsi les temps d'arrêt et les coûts de maintenance.
L'importance d'une stratégie globale
La mise en place d'une stratégie de maintenance efficace nécessite la prise en compte de l'équipement dans sa globalité. Chaque modification d'un élément peut avoir des répercussions sur l'ensemble du système. Un programme de maintenance préventive bien conçu, associé à une gestion rigoureuse des interventions, permet d'optimiser la disponibilité des équipements tout en maîtrisant les coûts.
Services & Produits associés
Gestion Maintenance Assistée par Ordinateur (GMAO)
Anticiper les pannes, détecter les anomalies et traiter les urgences facilement
Vêtements protection
Les vêtements de protection font partie des équipements de protection individuelle et des vêtements de travail.