Présentation de la fabrication additive
La fabrication additive est un procédé permettant de réaliser des pièces par ajout de matière contrairement aux procédés d'usinage traditionnels qui en retirent pour obtenir la pièce de la forme souhaitée.
Cette technique de fabrication est parfois appelée impression 3D mais en réalité, il ne s’agit pas vraiment d’impression mais de la mise en forme d’une pièce à partir de son modèle numérique (fichier CAO) en superposant successivement différentes couches de particules d’un matériau d’apport et de les fusionner entre elles pour finalement obtenir la pièce de la géométrie et la forme souhaitées.
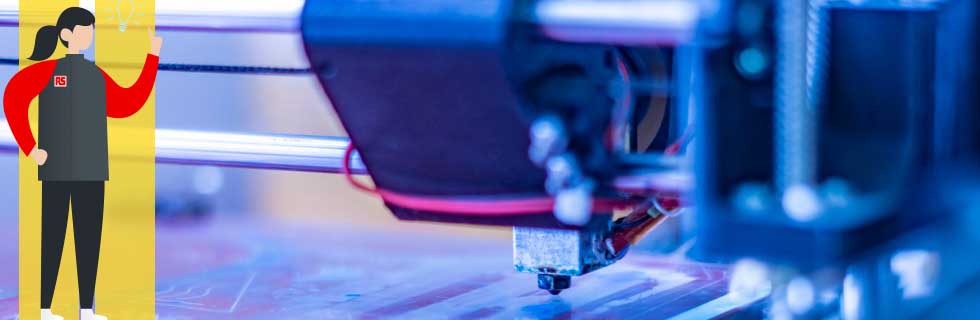
Article publié le 07/06/2021
Les techniques de fabrication additive rendent possible la réalisation de formes gauches et de pièces de géométries complexes avec des mailles fines, des canaux et autres cavités internes impossibles à effectuer avec des technologies de fabrication conventionnelle. Il est notamment possible de produire des pièces intégrant un assemblage fonctionnel tel que des charnières.
Divers procédés de fabrication additive ont été développés. Ils sont adaptés à une variété de matériaux d’apport (métaux, céramiques, polymères) utilisés sous forme de poudre, de fil, ou de résine. Selon le procédé mis en œuvre, le matériau sous forme de résine peut être durci par ultra-violet ou s’il est solide (poudre, fil), il est fusionné par diverses sources d'énergie : laser, faisceau d'électrons, plasma, arc électrique... Bien que certains procédés soient similaires, chaque machine sera dédiée à un type de matériau (métaux, céramiques, polymères). Impossible de produire une pièce en plastique avec une machine conçue pour produire des pièces métalliques.
Certaines technologies s’adressent exclusivement aux matières plastiques, comme la stéréolithographie ou la fabrication par un dépôt de filament en fusion. D’autres concernent uniquement la réalisation de pièces en métal comme le dépôt direct de métal par une buse d’alimentation qui propulse la poudre directement dans le faisceau du laser utilisé pour la faire fondre. Enfin, certaines technologies comme la fusion ou le frittage sur lit de poudre ou le Binder Jetting (projection de liant) s’appliquent à la fois aux plastiques et aux métaux.
Fusion sur lit de poudre
La technologie de fusion sur lit de poudre et celle de projection de liant sont deux méthodes couramment employées. En ce qui concerne les technologies de fabrication sur lit de poudre (métallique ou polymère), les procédés et les équipements de fabrication diffèrent selon la matière des pièces fabriquées. S'ils présentent des spécificités, ils partagent cependant des principes communs notamment concernant la mise en couche de la poudre. La technologie de fusion de lit de poudre métallique consiste à fusionner de manière sélective sur des régions extrêmement précises du lit de poudre de fines particules couche après couche afin de réaliser une section de la pièce souhaitée et de construire couche après couche la pièce en 3D. La fusion s’effectue généralement par laser mais il existe des systèmes employant des plasmas ou des faisceaux d’électrons. La création du lit de poudre peut s’effectuer avec une racle, un rouleau, par gravité... Chaque constructeur de machines a développé son propre système d’étalement.
Projection de liant
La technologie par projection de liant (Binder Jetting) diffère singulièrement de la fabrication additive par fusion sur lit de poudre. Elle se déroule en deux phases. La première consiste à la mise en forme de la pièce par superposition de couches de poudre agglomérée par un liant organique projeté sélectivement par une rampe d'impression multijet. Cette phase n'est pas suffisante pour fournir une pièce de la résistance attendue. Après avoir éliminé le liant par combustion (déliantage), la pièce dite « à vert » est consolidée et densifiée dans un four de frittage pour brûler le liant et donner la cohésion aux grains de poudre afin d'obtenir un composant métallique fonctionnel.
Finition et répétabilité
La production de pièces métalliques par technologie additive exige toujours des opérations de finition : retrait du support, découpage, nettoyage, sablage, traitement chimique ou mécanique pour améliorer les états de surface, ou encore traitement thermique pour éliminer d’éventuelles contraintes résiduelles. Les post-traitements thermiques permettent notamment d'améliorer les propriétés mécaniques de la pièce.
Le procédé de fabrication additive est par nature sujet à variations. Que l’on travaille à partir de poudre, de résine ou de fil, le plus difficile est de s’assurer de la répétabilité et la reproductibilité des processus afin d’être capable de réaliser plusieurs fois de suite exactement la même pièce.
À chaque procédé ses exigences
Les matériaux les plus couramment utilisés en fabrication additive sont les plastiques et les métaux. Pour la fabrication de pièces en plastique, il existe des machines relativement compactes qui peuvent être employées par des particuliers ou sur les établis des ateliers. En revanche, les machines produisant des pièces métalliques sont généralement plus volumineuses et techniquement plus complexes à mettre en œuvre. Elles sont donc plutôt destinées à un usage industriel.
Chaque machine, chaque procédé, chaque technologie et chaque application de fabrication additive présentent des exigences spécifiques. Le plus souvent, il n’est donc possible d’utiliser avec une machine donnée uniquement des poudres de certains alliages ou de polymères qualifiés par le fabricant de la machine. Même lorsque deux machines exploitent le même principe de fabrication additive, chacune d’elle aura ses propres exigences concernant les caractéristiques du matériau d’apport.
Les matériaux
Les procédés de fabrication par fusion laser sur lit de poudre peuvent mettre en forme des matériaux soudables comme par exemple des aciers inox, des alliages titane, des alliages à base de nickel ou de cobalt tels que l’Inconel (superalliage base nickel), l’aluminium, etc. Les techniques par projection de liant tel que le Metal Binder Jetting, qui ne fonctionnent pas par fusion mais par frittage, permettent d'adresser certains matériaux difficilement soudables. Elle peut par exemple traiter certains aciers inoxydables, le cuivre, le carbure de tungstène, certains alliages titane et certains types d’Inconel. Parmi les métaux, certaines nuances sont difficiles à mettre en œuvre pour la fabrication additive. Cependant, de nombreux travaux de R&D permettent d’étendre régulièrement la liste des matériaux éligibles.
Du côté des matières plastiques, la plupart des polymères courants sont aujourd’hui disponibles pour l’impression 3D. Il est même possible de mettre en forme des polymères techniques tel que le PEEK (polyétheréthercétone). Comme pour les métaux, leurs caractéristiques (couleurs, transparence, biocompatibilité, résistance, de rigidité, dureté, élasticité, etc.) déterminent le choix du matériau approprié à l’application. Ils se présentent sous forme de poudre, de granulé ou de filament.
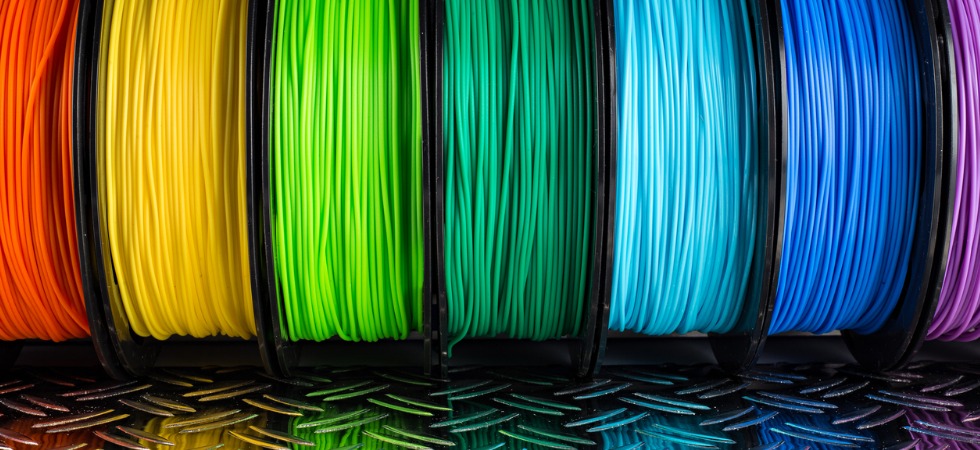
On distingue deux catégories de matières plastiques. Les thermoplastiques qui peuvent être refondus peuvent être mis en forme par des technologies FDM (Fused Deposition Modeling / Dépôt de Fil) et SLS (Selective Laser Sintering ou FLS en français, pour Frittage Sélectif par Laser). Les plastiques photosensibles, des matériaux polymères liquides ou malléables à des températures basses mais qui ne peuvent être fondus qu’une seule fois. Ces derniers permettent notamment la fabrication de pièces par le procédé SLA (Stereolithograph Apparatus), qui exploite le principe de photopolymérisation : une lumière UV solidifie couche après couche la résine.
Certains constructeurs de machines de fabrication additive imposent de travailler uniquement avec les matériaux qu’ils fournissent, tandis que d’autres laissent à l’utilisateur la liberté de choisir leur fournisseur de matière première dont les caractéristiques devront toutefois être conformes aux exigences de la méthode de fabrication envisagée et du domaine d’application visé (aéronautique, automobile, médical, luxe, …).
Exemple d’applications
Compte tenu des cadences de production et des dimensions de pièces relativement limitées, la fabrication additive est plutôt réservée à la réalisation de prototypes, de pièces unitaires ou en petites séries. Les procédés de fabrication additive ne sont donc pas adaptés à la production en très grandes séries de pièces massives et de formes simples. Ils sont notamment appréciés dans le domaine aéronautique car ils permettent de réaliser en une seule opération une pièce qui exigeait l’assemblage de plusieurs composants produits par des techniques de fabrication traditionnelles. Leur faible productivité est compensée par la possibilité de réaliser une pièce de géométrie complexe d’un seul bloc sur une même machine. Par ailleurs, la fabrication additive trouve son intérêt lorsqu’elle permet de travailler sur des métaux coûteux et difficiles à usiner. Elle permet la consommation de la juste quantité de matière et la réalisation d’économie en termes d’outils de coupe.
Les techniques de fabrication additive métal n’offrent pas le même niveau de répétitivité et de productivité que les procédés de production traditionnels. Les pièces métalliques produites sont généralement plus coûteuses. Elles sont néanmoins de plus en plus employées dans l’industrie pour alléger des pièces en optimisant leur topologie ou pour leur ajouter de nouvelles fonctionnalités. Elles sont d’ors et déjà exploitées à l'échelle industrielle pour la fabrication de pièces spécifiques dans le domaine du spatial, l’aéronautique et le médical.
Dans le domaine spatial
La tête d’injection du moteur cryogénique Vulcain 2.1, qui propulsera le lanceur Ariane 6 d’ArianeGroup pendant les huit premières minutes du vol, est produite par un procédé de fabrication additive. Elle était auparavant composée d’une centaine d’éléments. Cette pièce, en alliage base nickel de géométrie complexe et renfermant de nombreuses cavités, est aujourd’hui produite d’un seul bloc.
Dans le secteur aéronautique
Le moteur LEAP, conçu par Safran Aircraft Engines et GE, est destiné à équiper les avions monocouloirs de nouvelle génération tels que les Airbus A320neo, le Boeing 737 MAX, et le Boeing 777X. L’injecteur de carburant est produit par un procédé de fabrication additive afin de permettre son allègement et de réduire les coûts de production. Il est fabriqué en une seule pièce alors qu’il nécessitait auparavant l’assemblage de vingt composants soudés. L’optimisation topologique, combinée à l’absence de soudures et de fixations, ont permis de réduire le poids de l’injecteur de 25% tout en augmentant sa robustesse.
Dans l’industrie automobile
Volkswagen emploie par exemple la fabrication additive pour développer ses outils, accessoires et fixations qui sont utilisés sur ses chaînes de montage. Ce qui lui permet d’internaliser la fabrication de ces outillages et de diminuer les coûts et les délais de fabrication.
Dans le domaine médical
Des dispositifs tels que les prothèses ou les implants sont aujourd’hui couramment produits par des procédés de fabrication additive. La bio compatibilité de l’alliage de chrome cobalt et ses caractéristiques mécaniques rendent notamment possible la fabrication des prothèses et implants sur-mesure. Ce qui facilite leur pose et offre un plus grand confort au patient.
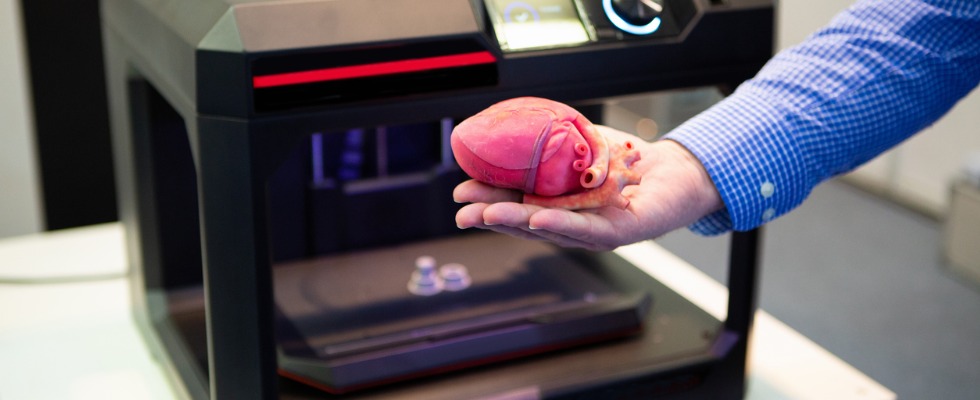
Pour approfondir
Pour en savoir plus sur les nouvelles technologies dans le monde de la maintenance, nous vous proposons une infographie listant les technologies majeures dans les lignes de production ou bien un article traitant spécifiquement des AGV.
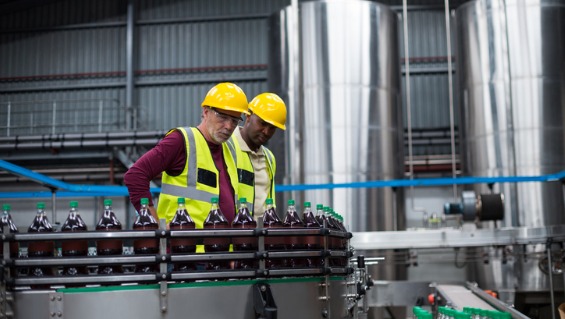
Innovations bouleversant les lignes de production
L’un des principaux défis dans l’industrie de demain est de migrer vers la maintenance prédictive. Cette méthode est plus efficace car elle se base sur le remplacement des pièces lorsqu’elles présentent des signes physiques de rupture. Découvrez en plus avec notre infographie vous présentant le top 9 des nouvelles technologies qui y sont associées.
Qu’est-ce qu’un AGV ?
Un AGV est l’acronyme de Automated Guided Vehicle. C’est donc un véhicule guidé automatiquement. A priori, il peut s’agir de n’importe quel véhicule.Cependant, dans le domaine logistique et industriel, le terme AGV est plus généralement employé pour les engins de manutention auto-guidé.
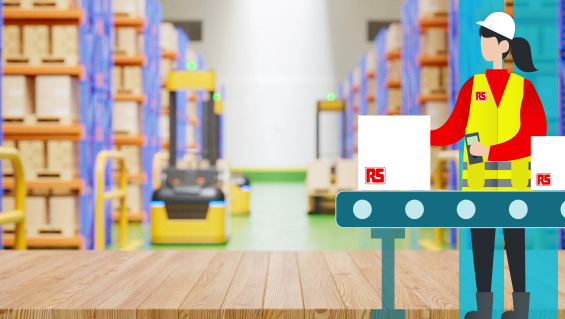
Services & produits associés
Service impression3D
Du virtuel à la réalité grâce à notre service impression 3D.
Logiciels
Le logiciel d'impression 3D est une suite d'outils logiciels qui aident à transformer des conceptions en prototypes avec des imprimantes 3D.
Imprimantes 3D
Les imprimantes 3D révolutionnent les processus de fabrication, fournissant des solutions pour le prototypage rapide et la fabrication addit
Matériaux
Une large gamme de matériaux adaptés à toutes sortes d'imprimantes 3D. Que vous optiez pour une imprimante à filament plastique ou à résine.