Un système robotisé collaboratif reste une machine
Quel que soit le mode de fonctionnement du robot (coexistence, coopération, collaboration), l’installation automatisée au sein de laquelle il est intégré demeure une machine comme une autre. Le robot sans outil monté sur celui-ci est une quasi-machine qui ne peut assurer à lui seul une application définie. Un système robotisé collaboratif comprend un ou plusieurs robots industriels ainsi que tous les outillages, composants et capteurs nécessaires à son fonctionnement. Il est soumis à la directive dite ''Machines'' 2006/42/CE. L’intégrateur ou le constructeur de machine qui l’a conçu doit respecter des exigences essentielles de santé et de sécurité énumérées dans cette directive.
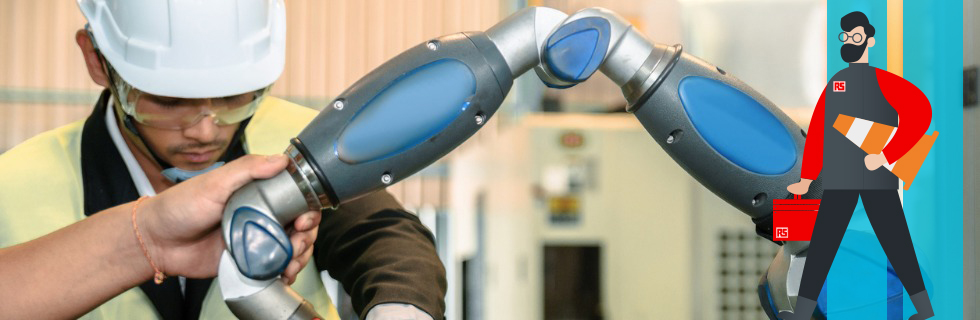
Article publié le 10/03/2021
Les principales normes en vigueur
L’installation robotisée collaborative d’un système robotisé collaboratif doit donc faire l’objet comme toute machine d’une analyse de risque. Une évaluation des risques doit être effectuée afin de déterminer les exigences de santé et de sécurité qui s'appliquent à la machine. La cellule robotisée doit ensuite être conçue et construite en prenant en compte les résultats de cette évaluation.
Des normes internationales (NF EN ISO 10218-1 et 2 : 2011) spécifient les exigences de sécurité pour l’intégration des robots industriels. Elles ont été élaborées dans le but d’aider les fabricants de robots et les intégrateurs de systèmes robotisés à atteindre les objectifs de sécurité fixés par la réglementation, notamment, à respecter les exigences essentielles de santé et de sécurité énoncées dans la directive « Machines » 2006/42/CE. En complément de ces normes, une spécification technique référencée ISO/TS 15066 : 2016 dédiée aux applications collaboratives robotisées, a été rédigée. Celle-ci vise à préciser les principes de sécurité à appliquer aux modes de fonctionnement collaboratif et à accompagner l’analyse de risques qui doit être mise en œuvre pendant la phase d’étude et de réalisation du projet d’intégration.
L’ISO 10218-1, qui ne traite pas le robot comme une machine complète, spécifie les exigences et les recommandations pour la prévention intrinsèque, les mesures de protection et les informations pour l’utilisation des robots industriels. Elle décrit les phénomènes dangereux de base associés aux robots et fournit des exigences pour éliminer ou réduire de manière appropriée les risques associés à ces phénomènes dangereux.
L’ISO 10218-2, spécifie les exigences de sécurité pour l'intégration des robots industriels et des systèmes robots industriels tels que définis dans l'ISO 10218-1, et de la (ou des) cellule(s) robotisées industrielles. Elle ne traite pas spécifiquement des phénomènes dangereux liés aux processus (par exemple rayonnement laser, éjection de copeaux, fumée de soudage). D'autres normes peuvent être appliquées pour le traitement de ces phénomènes dangereux.
La norme ISO/TS 15066 spécifie les exigences de sécurité pour les systèmes de robots industriels collaboratifs et l'environnement de travail, et complète les exigences et les conseils sur le fonctionnement des robots industriels collaboratifs donnés dans les normes ISO 10218-1 et ISO 10218-2.
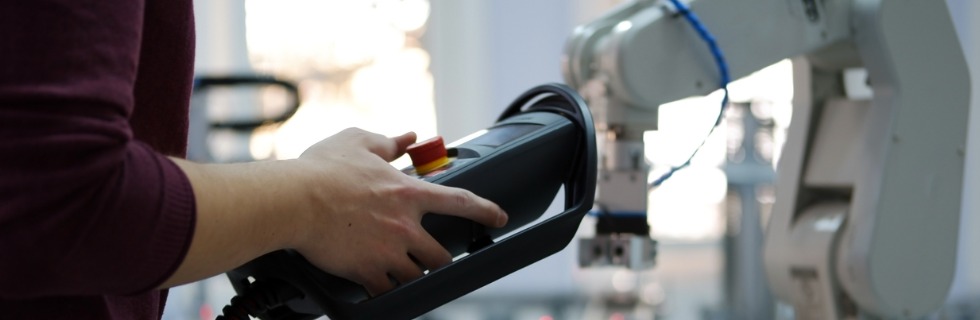
Analyse des risques
Toute intégration d’un robot dans une application collaborative doit donc démarrer par une analyse de risque de l’installation à laquelle il est associé. Même si cette installation exploite un cobot conçu pour opérer à vitesse très réduite et de manière tout à fait inoffensive, elle est soumise à la directive machine et donc à une indispensable analyse de risque. Les cobots sont initialement développés pour ne pas causer de blessures irréversibles. Ils ne sont pas censés apporter de danger à l’opérateur sauf si le robot manipule par exemple un outil coupant ou perforant.
L’analyse des risques consiste à identifier tous les phénomènes dangereux à partir des caractéristiques, performances et modes opératoires de la machine. Elle permet de déterminer quels risques nécessitent la mise en place de mesures de protection et d’évaluer rapidement les besoins en sécurité de la machine, servant ainsi de base à sa conception. Elle consiste à proportionner les moyens techniques à mettre en œuvre en fonction du risque à traiter. Elle a pour objectif de prévenir tout mauvais usage raisonnablement prévisible. En fonction de la tâche réalisée par le robot collaboratif et selon les conclusions de l’analyse de risques menée, il est possible de recourir à des éléments de sécurité externes : équipements de protection individuelle, barrières matérielles et immatérielles, tapis sensibles, scrutateur laser... Pour chaque application, il faut évaluer la fréquence d’exposition, la possibilité d’évitement, la dangerosité… afin de mettre en place l’environnement de sécurité approprié et garantir que le robot ne blesse pas l’opérateur.
Pour approfondir
Si vous souhaitez en savoir plus sur l'univers des cobots, nous vous proposons les articles suivants pour parfaire votre connaissance ou pour simplement répondre à votre curiosité.
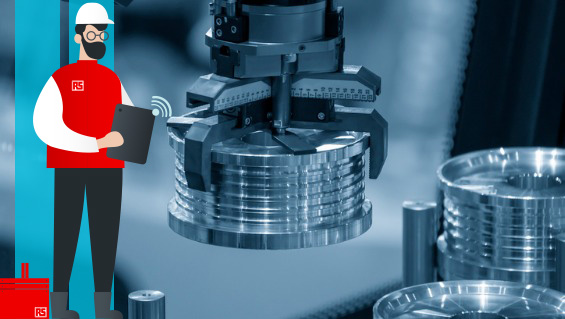
Du robot au cobot
Les premiers robots ont été initialement déployés pour opérer dans des environnements dangereux comme dans le secteur nucléaire. Ils se sont au fil des ans invités dans tous les secteurs industriels. Depuis leur première utilisation sur les lignes de production automobile au début des années soixante, les robots ont fait bien du chemin.
Mise en sécurité des robots collaboratifs
Qu'importe le mode d'interaction choisi, les mesures de prévention associées à la mise en œuvre d’un robot collaboratif sont encadrées par la norme NF EN ISO 10218-2 qui repose sur quatre principes de mise en sécurité, combinables entre eux. Quels sont ces 4 principes et qu'est-ce que cela implique ?
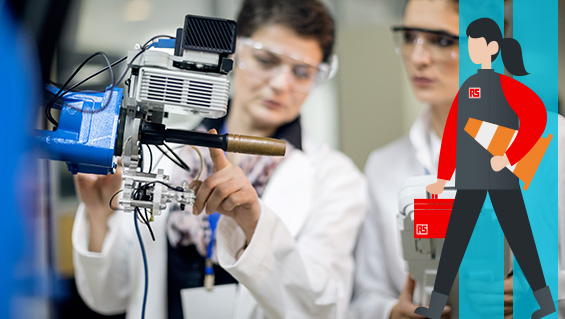
Produits associés
Système verrouillage
Les interrupteurs de verrouillage de sécurité sont conçus pour la sécurité où des portes/des protections sont utilisées proches de machines.
Scanners
La détection de lumière et la portée sont essentielles dans une grande variété d'applications de contrôle de mouvement.
Barrières sécurité
Les barrières de sécurité permettent de délimiter la zone de travail, et donc d’interdire/prévenir du danger dans la zone concernée.
Relais de sécurité
Un relais de sécurité est un dispositif de surveillance des erreurs ou défaillances potentielles dans les machines ou les usines.