Qu’est-ce qu’un AGV ?
Un AGV est l’acronyme de Automated Guided Vehicle. C’est donc un véhicule guidé automatiquement. A priori, il peut s’agir de n’importe quel véhicule tel qu’une navette ou un métro qui, sans conducteur, transportent des passagers d’un point à un autre. Cependant, dans le domaine logistique et industriel, le terme AGV est plus généralement employé pour les engins de manutention auto-guidé.
Les AGV sont traditionnellement guidés dans leurs déplacements par des systèmes de guidage ou des marquages au sol. Ils exploitent aujourd’hui davantage des technologies optiques ne nécessitant pas d’infrastructures matérielles contraignantes. Ce qui permet de modifier plus aisément leurs trajets.
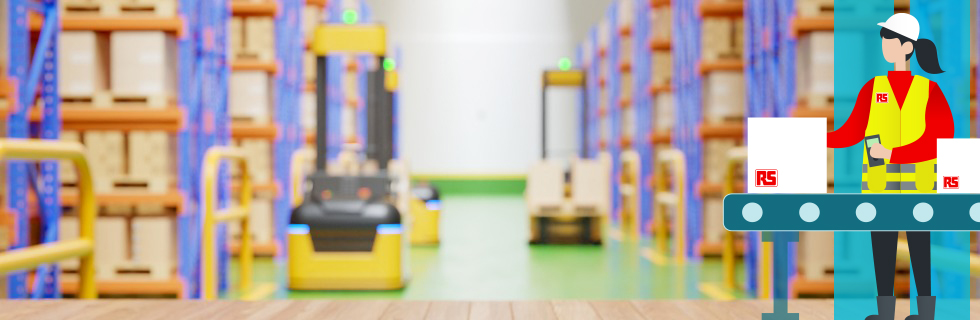
Article publié le 30/03/2021
Cela fait des années que les AGV sont exploités pour acheminer et manutentionner sans cariste des palettes, des bobines ou des charges de divers formats d'une ligne de production à une autre, d'un quai de déchargement à leur zone d'entreposage ou entre des sites extérieurs distants. Les AGV transportent donc des charges automatiquement et inlassablement d’un point à un autre selon une mission et un parcours bien défini. Bien souvent, les AGV manutentionnent des charges lourdes sous forme de palettes ou de bobines par exemple. Historiquement, les AGV sont des chariots traditionnels tels que des transpalettes, des gerbeurs, des chariots élévateurs auxquels ont été intégrés des équipements permettant leur automatisation et leur fonctionnement autonome.
Mais des AGV sont aussi développés pour le transport de charges très spécifiques. Il peut s’agir de plateformes automotrices dimensionnées selon la forme et le poids des charges à transporter ou de chariots élévateurs conçus sur mesure pour réaliser des manutentions particulières : du levage latéral de charges au transport de rouleaux de papier de plusieurs tonnes en passant par la rotation de pièces disposées sur étagère ou tout autre support.
Au fil des ans, les AGV ont fait la preuve de leur efficacité et de leur fiabilité sur le terrain. Mais malgré les efforts de leurs constructeurs pour standardiser leurs gammes, leur spécificité et leur fabrication en faible volume renchérissent leur coût. Car finalement, il s’agit bien souvent de machines spéciales qui doivent être adaptées aux exigences de l’application industrielle et aux caractéristiques des charges à transporter et des opérations de manutention à réaliser.
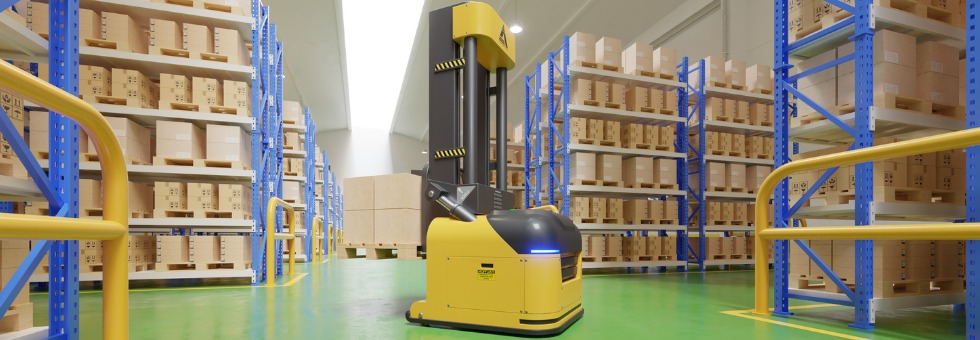
Du filoguidage au guidage optique
Les AGV sont guidés dans leur déplacement. A l’instar d’un train sur les rails, ils suivent une voie toute tracée. Il existe différentes techniques de guidage. Chaque technique répond aux spécificités de l’environnement industriels et de l’application. Le filoguidage consiste à guider le chariot par des pistes physiques intégrées au sol, rail métallique, fil électrique, plots ou bandes magnétiques. La machine va ainsi suivre un trajet prédéfini et réaliser une tâche préétablie de façon automatique et sans nécessiter la présence d’un opérateur. Ces techniques sont contraignantes puisqu’elles impliquent l’installation d’une infrastructure de guidage qui doit être reconfigurée si l’on veut modifier le trajet et les missions des AGV. Ce qui ne répond pas à la flexibilité attendue par certains industriels qui souhaitent adapter plus simplement leur flux logistiques aux évolutions de leur processus de production.
Les systèmes de guidage ont donc évolué pour adopter des technologies permettant la reconfiguration des missions des AGV avec une plus grande liberté. Les technologies optiques exploitant des dispositifs laser permettent notamment de se passer de rails et autres guides physiques au sol. Elles permettent ainsi aux chariots de naviguer dans les entrepôts ou les usines sans ajout d’infrastructures matérielles contraignantes. Elles rendent également possible la transformation d’équipements de manutention traditionnels tels qu’un transpalette ou un gerbeur en chariot robotisé guidé automatiquement.
De l’AGV au chariot robotisé
L'une des grandes différences entre un AGV et un chariot robotisé est que ce dernier est un équipement standard sur lequel sont embarqués les dispositifs de guidage et de sécurité reposant le plus souvent sur des technologies laser. Un chariot robotisé peut même être utilisé dans certains cas par un cariste si l'on déconnecte le système de pilotage et de guidage automatique.
Tracteurs, transpalettes, gerbeurs ou encore chariots à mât rétractable et tri-directionnels, tous les équipements standards dédiés aux flux intralogistiques peuvent être robotisés. Leur surcoût est alors uniquement lié à l'intégration des dispositifs de navigation et de sécurité ainsi qu'à leur mise en service. Leur maintenance ou leur dépannage ne se distinguent pas de celles des gammes standards. Au contraire des AGV qui sont le plus souvent des machines spéciales, fabriquées en moindre volume et qui réclament donc des pièces particulières.
La mise en œuvre de chariots robotisés ne nécessite donc pas l’installation de système de guidage inductif ou de rail sur le sol. Ces engins de manutention peuvent donc se déplacer sans contrainte dans différentes zones d'un site de production ou d'un entrepôt et s'adapter aux diverses missions qui leur sont assignées au gré de l'évolution des besoins. Le géo-guidage peut s’effectuer par le biais d'un scanner laser surélevé qui balaye l'environnement qui l'entoure sur 270°. Il s’appuie sur la reconnaissance d’éléments existants dans l’environnement : murs, colonnes, et racks pour permettre aux chariots de se repérer en temps réel. D'autres solutions reposent sur la technique de triangulation laser exigeant la mise en place de quelques réflecteurs dans les allées ou au pied des racks de stockage pour recaler la position du chariot à intervalle régulier.
Toutes entreprises, de toutes tailles et quel que soit leur secteur d'activité peuvent tirer parti des avantages des chariots robotisés. La rentabilité d'un tel investissement ne dépend pas de la taille de la flotte mais avant tout du nombre de caristes employés à des tâches de manutention spécifiques et répétitives. Si par exemple le transfert régulier de palettes entre deux postes, sur un site qui tourne en 2x8, réclame l'emploi d'au moins deux caristes, le coût annuel de leurs salaires correspond, selon certains fournisseurs, à peu près à l'investissement dans un transpalette robotisé. Selon certains spécialistes, le retour sur investissement peut être obtenu en 18 à 24 mois dès qu’un site opère en 2x8 et en 12 mois pour une utilisation en 3x8.
Leur mission : décharger l’homme des tâches répétitives et rébarbatives en assurant le transport de charges sans cariste ou conducteur.
Leurs objectifs : absorber la croissance des flux intra-logistiques, réduire les coûts d'exploitation tout en gagnant en productivité, éliminer les risques de TMS qui sont assez fréquents chez les caristes, libérer les opérateurs des tâches de manutention afin qu'ils se concentrent sur des missions à plus forte valeur ajoutée, et améliorer la qualité puisque les AGV, contrairement à un cariste dont l’attention n’est pas sans faille, ne risquent pas de provoquer une collision ou renverser leur chargement.
Pour approfondir
Si vous souhaitez en savoir plus sur de nouvelles technologies, nous vous proposons les articles suivants pour parfaire votre connaissance ou pour simplement répondre à votre curiosité.
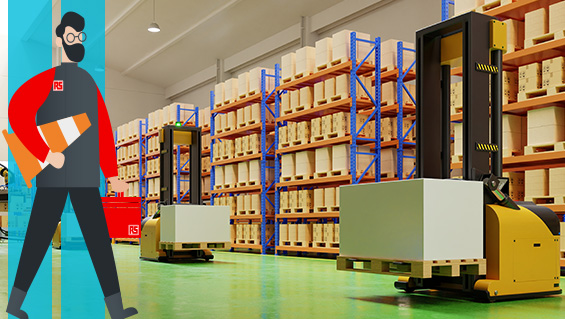
Les principales techniques de guidage des AGV
L'AGV permet de décharger le personnel des tâches répétitives et réduire les coûts de manutention de charges régulièrement transportées d’un point à un autre d’un atelier industriel ou d’un centre logistique.
Diverses technologies sont mises en œuvre pour assurer le guidage automatique des AGV depuis le filoguidage jusqu’à des solutions reposant sur des technologies laser.
Mise en sécurité des robots collaboratifs
Qu'importe le mode d'interaction choisi, les mesures de prévention associées à la mise en œuvre d’un robot collaboratif sont encadrées par la norme NF EN ISO 10218-2 qui repose sur quatre principes de mise en sécurité, combinables entre eux. Quels sont ces 4 principes et qu'est-ce que cela implique ?
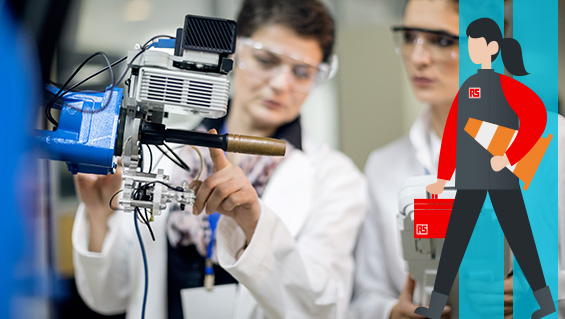
Produits associés
Barrières sécurité
Les barrières de sécurité permettent de délimiter la zone de travail, et donc d’interdire/prévenir du danger dans la zone concernée.
Arrêt d'urgence
Un bouton-poussoir d'arrêt d'urgence est une commande de commutation, ou interrupteur, qui assure un arrêt complet sécurisé des machines.
Scanners
La détection de lumière et la portée sont essentielles dans une grande variété d'applications de contrôle de mouvement.
Barrières IR
Ces dispositifs optoélectroniques sont utilisés pour détecter les personnes présentes à proximité de machines mobiles.