Qu’est-ce que la maintenance préventive ?
Au-delà de l’objectif de permettre de maintenir la production d’un objet industriel en évitant au maximum l’arrêt de ses lignes de fabrication, la maintenance préventive a des enjeux plus globaux. La notion de maintenance est née aux États-Unis dans les années 1950. À l’heure où la France industrielle évoquait encore « l’entretien » de ses chaînes de production, les ingénieurs américains travaillaient déjà sur le concept de la défaillance. Le concept de « maintenance », où l’industriel maîtrise ses conditions d’intervention, a ainsi remplacé le concept « d’entretien », où l’industriel subit les défaillances de son matériel.
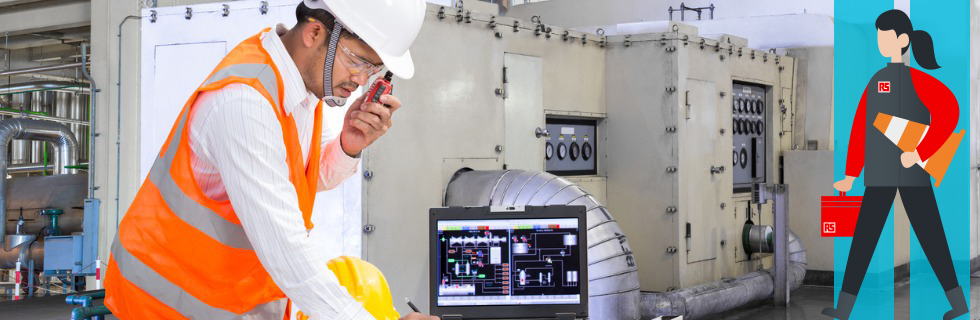
Article publié le 18/08/2021, mis à jour le 28/04/2022
En quoi consiste la maintenance préventive ?
La maintenance préventive sur les matériels permet de vérifier leur état de fonctionnement et l’usure de leurs composants, de manière planifiée selon une périodicité définie. L’objectif visé est de voir l’évolution de leur dégradation afin de prévenir les pannes.
Un programme de maintenance préventive est donc constitué de contrôles, visites périodiques, CND et interventions de maintenance effectuées en prévention. Il s’oppose en cela à la maintenance corrective, qui survient à cause d’une panne ou d’une perturbation du process.
Quels sont les objectifs de la maintenance préventive ?
Les objectifs de la maintenance préventive portent sur les produits, mais aussi sur les aspects humains.
- l’amélioration de la fiabilité du produit ;
- l’amélioration de la planification des travaux ;
- l’amélioration de la gestion des stocks de pièces de rechange ;
- la garantie de la qualité des produits ;
- la garantie sur la sécurité des employés ;
- l’amélioration des relations entre services de production et de maintenance.
La maintenance préventive en quelques chiffres
Il existe peu de chiffres sur le gain de productivité des lignes de production par rapport à la maintenance curative ou en termes de déploiement de la maintenance préventive. Les seuls éléments chiffrés sur les gains observés par les services de maintenance sont fournis par l’AFIM (Association Française des Ingénieurs de Maintenance). Ils ont diffusé un exemple des moyennes observées auprès de plusieurs entreprises ayant déployé une GMAO (Gestion de la Maintenance Assistée par Ordinateur).
- Les temps de préparation pour les travaux ont diminué de 20 à 30 %.
- Les durées d’intervention ont diminué de 10 à 30 %.
- La durée de vie de l’équipement a augmenté de 50 %.
- Le coût du stock a diminué de 10 à 20 %.
Quels sont les principes élémentaires de la maintenance préventive ?
Ses principes élémentaires se situent sur trois axes :
- Respecter les principes de « bonne conduite » des matériels : pilotage et nettoyage soignés de l’installation, réparations précises et bonne lubrification des organes à graisser.
- Limiter le nombre de démontages-remontages, qui font perdre de la fiabilité à l’installation.
- Effectuer la maintenance selon les 5 niveaux définis dans la norme NF X60-000.
- Niveau 1 : relevé des paramètres de fonctionnement des machines et contrôle visuel ;
- Niveau 2 : opérations de maintenance préventive régulièrement effectuées sur les équipements comme les remplacements de filtres, la vidange d’huile moteur, etc. ;
- Niveau 3 : opérations de maintenance préventive, curative, de réglages ou réparations mécaniques ou électriques mineurs. À titre d’exemple, le remplacement et le réglage d’injecteurs, le remplacement d’un disjoncteur, etc. ;
- Niveau 4 : opérations complexes, comme le contrôle d’alignement moteur/alternateur ;
- Niveau 5 : opérations lourdes de rénovation ou de reconstruction d’un équipement, qui nécessitent le démontage de l’équipement et son transport dans un atelier spécialisé.
Les contrôles périodiques réglementaires
Certains appareils sont soumis à la réglementation et nécessitent des contrôles périodiques, réalisés par des organismes agréés comme APAVE ou SOCOTEC.
Les matériels qui nécessitent des visites périodiques obligatoires sont listés par catégories :
- les appareils de levage (monte-charges, ponts roulants, ascenseurs, grues, palans et élingues),
- les appareils à pression, de type générateurs ou récipients sous pression de gaz ou de vapeur, qui nécessitent une épreuve hydraulique,
- les installations électriques basse tension et haute tension,
- les sources radioactives, pour lesquels le personnel de maintenance doit posséder la qualification DATR,
- les machines dangereuses,
- les véhicules.
Comment élaborer un plan de maintenance préventive ?
La méthode permettant la mise en place d’un plan de maintenance préventive nécessite l’adhésion et la participation de tous les collaborateurs de l’entreprise. Par ailleurs, l’avènement de la GMAO dans les entreprises industrielles implique que toutes les opérations qui suivent sont réalisées à l’aide d’un logiciel de GMAO performant et adapté aux besoins de l’entreprise.
Étape 1 : rassembler les données de base indispensables
L’objectif visé est la constitution d’une structure de nomenclature des matériels de l’entreprise. Ce travail nécessite la mise en commun des données de base, qui se situent dans tous les services : production, études, qualité, maintenance, jusqu’ à la comptabilité, qui possède toutes les factures d’achat de pièces de rechange. La participation active de tous les collaborateurs de ces services est indispensable à la réussite de cette analyse.
Les données de base doivent également rassembler des fiches pratiques pour chaque type de matériel, qui explicitent les actions de maintenance préventive à réaliser. Et ceci pour chaque typologie de matériel :
- mécanique : pompes, roulements, transmissions, courroies…
- pneumatique : compresseurs, vérins…
- électricité : moteurs, batteries, transformateurs…
- contrôles non destructifs : analyses vibratoires, métrologie, détection de fuites, etc.
Des arborescences fonctionnelles, géographiques (par secteurs dans un bâtiment) et par famille de matériels doivent ainsi être constituées. Cette analyse doit aboutir à la sélectivité des machines et matériels à introduire dans le plan de maintenance préventive.
Ces nomenclatures de matériels seront introduites dans le logiciel de GMAO.
Étape 2 : réaliser les analyses AMDEC
Les études AMDEC (Analyse des Modes de Défaillance de leurs Effets et de leur Criticité) permettent d’identifier, sur la base des nomenclatures précédentes, les dysfonctionnements possibles des différents composants d'un système et d’évaluer les risques en cas d’apparition de ces défaillances.
Ces analyses fonctionnelles seront, à leur tour, introduites dans le logiciel de GMAO.
Étape 3 : élaboration du plan de maintenance préventive
Le plan de maintenance préventive est ainsi constitué grâce au logiciel de GMAO, dans lequel les intervenants de production et de maintenance retrouveront les documents opérationnels. Il sera documenté par les fiches techniques de chaque matériel, de réparation et d’entretien fournis par le constructeur. Le plan de maintenance intégrera aussi toutes les opérations de contrôles réglementaires.
La planification des travaux de maintenance préventive sera ainsi intégrée dans le logiciel de GMAO, qui permettra de suivre également :
- la préparation des arrêts de production, avec leur calendrier de réalisation,
- leur suivi de réalisation,
- l’historique des interventions, matériel par matériel,
- la gestion des pièces de rechange,
- les analyses quotidiennes à réaliser selon la liste des points de contrôle.
Pourquoi la maintenance prédictive est-elle la suite logique à la maintenance préventive ?
Les programmes de maintenance préventive se basent sur des paramètres tels que le nombre de cycles de fonctionnement ou la durée de vie d’un matériel, en fonction de ses caractéristiques « constructeur ». Mais ces paramètres ne prennent pas en compte les conditions d’utilisation de l’installation (par exemple sous ambiance radioactive ou avec un degré d’hygrométrie élevé). A contrario, quand un matériel est utilisé en deçà des performances pour lesquelles il a été conçu, son remplacement survient alors que la pièce n’a pas encore besoin d’être remplacée, ce qui occasionne des coûts inutiles…
La maintenance prédictive permet alors logiquement d’éviter ce genre de situations, puisqu’elle prévoit les opérations de maintenance à partir des paramètres de fonctionnement collectés en temps réel. Elle constitue donc une véritable suite logique à la maintenance préventive, grâce à la précision d’analyse de ses données temps réel.
Vous souhaitez en savoir plus sur les concepts de maintenance préventive systématique et de maintenance préventive conditionnelle ? N’hésitez pas à consulter notre article…
Pour approfondir
Apprenez en plus sur deux autres types de maintenance : la curative et la prédictive.
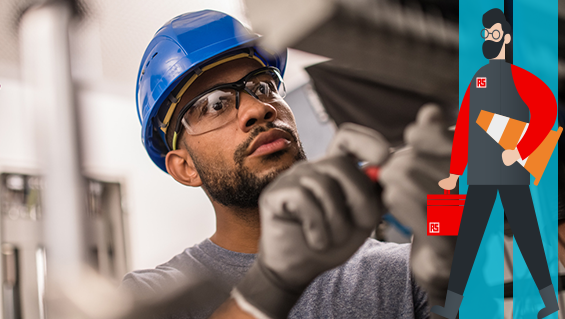
Qu'est-ce que la maintenance curative ?
Un serveur informatique qui tombe en panne après une première intervention, une ligne de production en fin de vie qui est à l'arrêt ou une machine déjà réparée qui ne répond plus. Ce sont trois exemples qui nécessitent l'intervention urgente de techniciens pour faire face à la défaillance d'un équipement. Cette démarche, c'est ce qu'on appelle la maintenance curative.
Qu’est-ce que la maintenance prédictive ?
Intervenir sur une machine, une ligne de production ou un équipement industriel juste au moment où ce dernier en a besoin. Voici le principe de la maintenance prédictive.
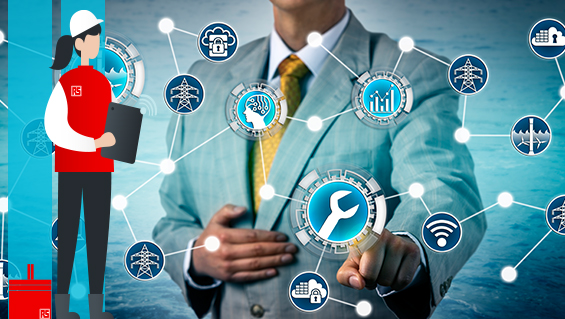